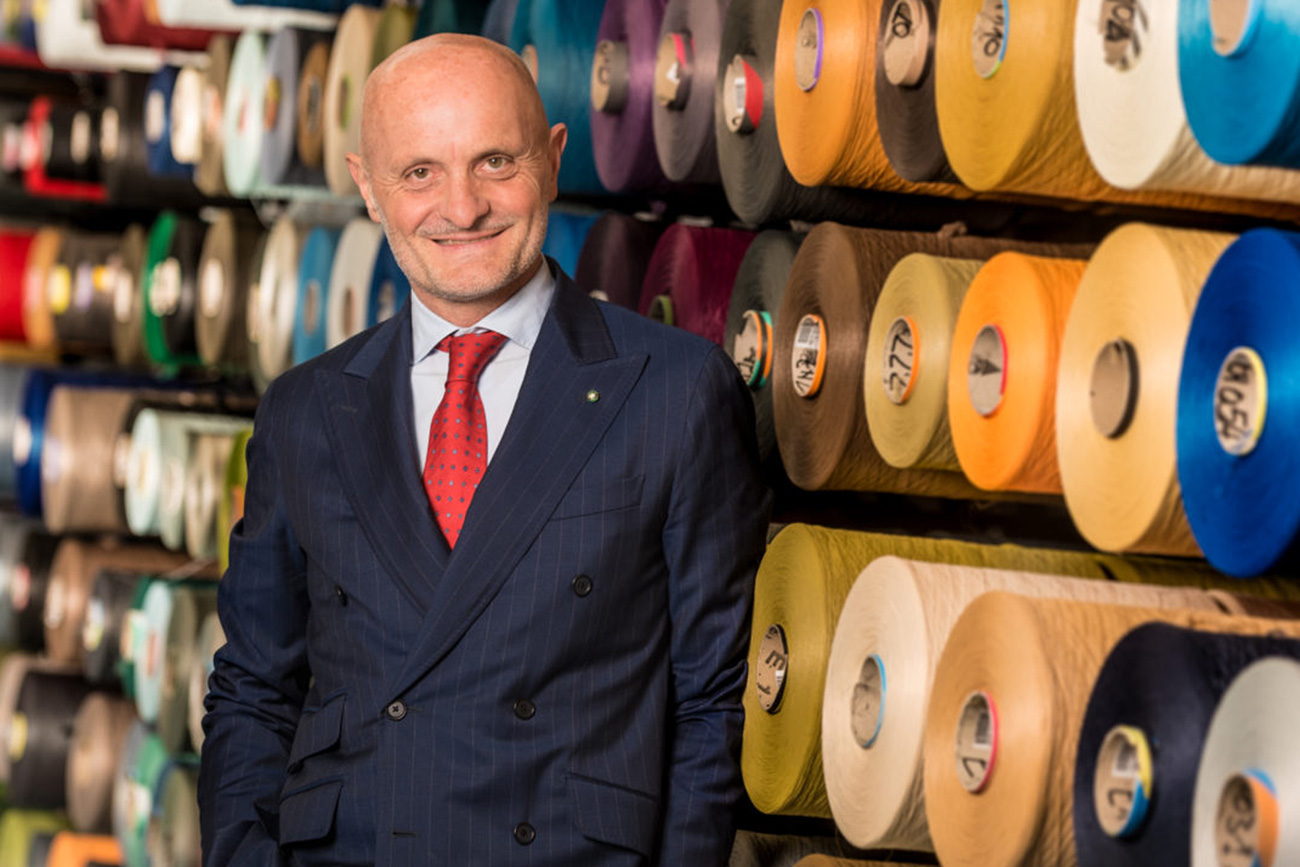
Netting Zero
Aquafil Bolsters ECONYL Portfolio with New, Wider Range of Applications.
Netting Zero
Aquafil Bolsters ECONYL Portfolio with New, Wider Range of Applications.
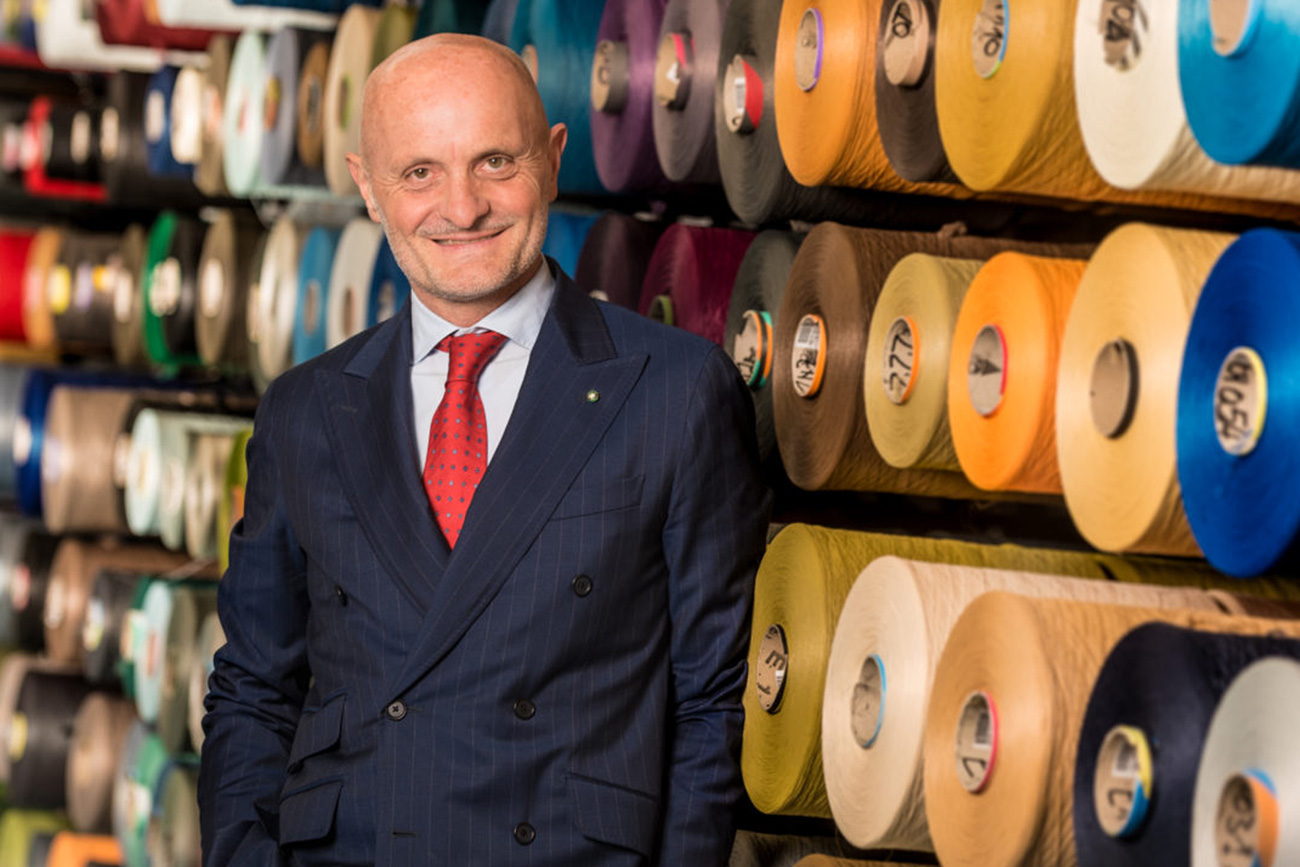
As industry continues its quest to advance from a linear system to a circular economy, Aquafil is expanding our understanding of what’s possible now, as well what will come next in terms of the continuous recyclability of products derived from waste.
Aquafil is best known for ECONYL, a sustainable regenerated nylon sourced from rescued fishing nets that has featured in collections ranging from high-profile active/outdoor brands like Outerknown to high-end fashion labels like Stella McCartney. Now the company, a multinational firm based in Italy, looks to advance its vision of circularity with a wider range of applications. “Our main businesses are carpet and fashion fibers, but now we are looking into making polymer for injection molding and even cable for 3D printing applications and film for the packaging industry,” explained Giulio Bonazzi, CEO and chairman, who joined the company in 1997, a business his family founded in 1965. ECONYL launched in 2011 for the carpet market.
“We want to create a system where people who want to can make a raincoat out of 100 percent of the same material. Or people who want to make a chair, can make it out of 100 percent the same material — from the cushions to every component of the chair,” Bonazzi stated, adding, “Because if you want to be able to recycle these products at the end of use, you have to design with end of life in mind.”
For example, following three years in development, Aquafil and brand partner Napapijri, a VF Corp company, have launched the Circular Series, with garments that feature a mono-material composition. The jacket fabric is made from ECONYL; filling and trims are made from Nylon 6. By using only one material it allows for an easier recycling process and as such the Circular Series jacket can enter the recycling machine as is, and fibers are upcycled without losing any of their original characteristic or quality. ECONYL can be recycled again and again whereas conventional synthetics break down, according to Bonazzi.
“The ECONYL system is so cool; instead of oil, it comes entirely from waste” — Giulio Bonazzi, CEO and chairman, Aquafil
“The ECONYL system is so cool; instead of oil, it comes entirely from waste,” said Bonazzi, during a recent webinar hosted by Material ConneXion titled, “Waste: An Ocean of Opportunity.” Simply stated, the Aquafil process regenerates the waste nylon to its original building blocks by using a system of steam, energy, a little bit of water and a catalyst to speed reaction. There is nothing harmful in the solvents, according to Bonazzi, who elaborated, “The efficiency of the de-polymerization system is close to 100 percent. Material is not lost during this process: One pound of nylon waste equals one pound of new ECONYL.”
When the topic of dyes was raised during the webinar discussion, Bonazzi noted that Aquafil “is the biggest solution dyed nylon company in the world. And all pigments are cradle-to-cradle certified.” Currently the company is creating natural colors to its solution dye systems. The firm achieves a lower footprint by using 65 percent less energy compared to conventional nylon processing and the company relies on renewable energy in its manufacturing facilities.
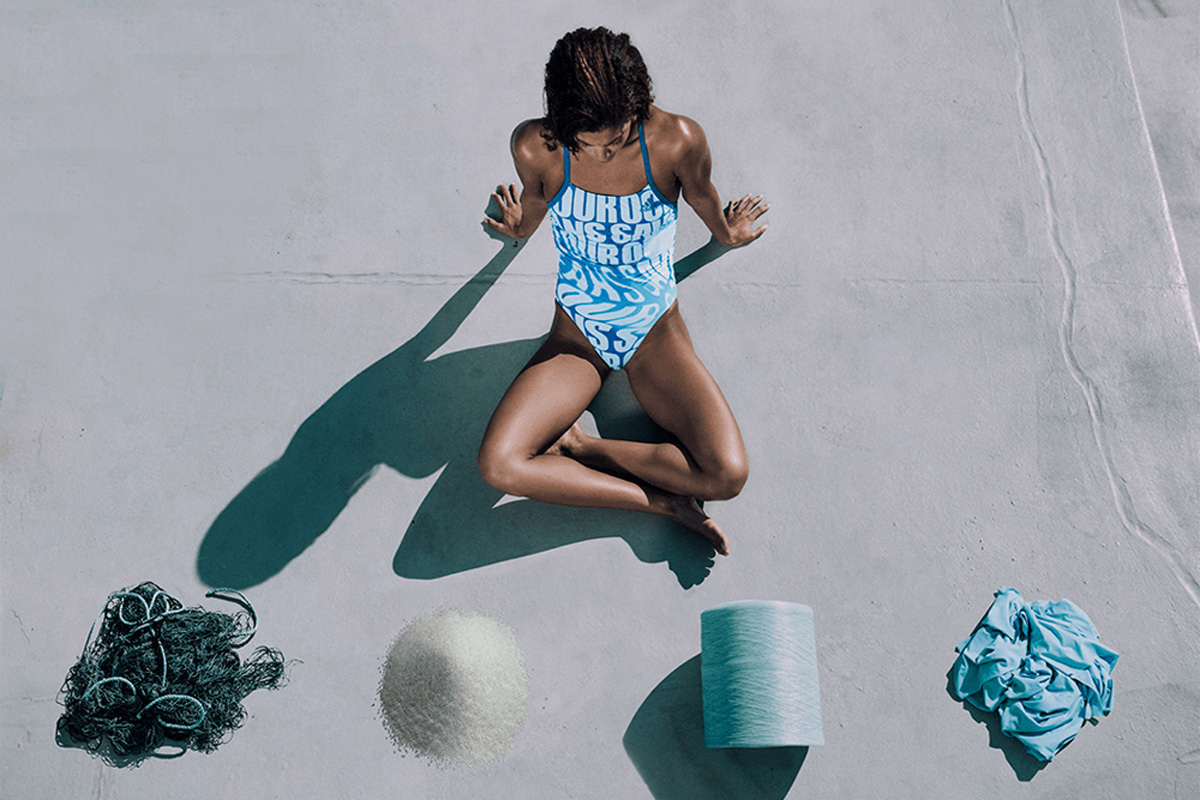
Developments are underway to expand business opportunities. In the near term, Bonazzi mentions a breakthrough in 3D printing, as “this may represent the future for society.” Looking further ahead, Aquafil is keen on bio-based Nylon 6 production. Aquafil, together with the biotech company Genomatica, based in San Diego, CA, have been working together on their first production run of a plant-based nylon having already succeeded in producing a couple thousand pounds. The renewable resource relies on a sugar fermentation. Bonazzi projects the demo plant to be completed in 2021.
“To have a complete disconnect from oil, one can start with renewal sources and infinite recyclability. It is easy to say, but more difficult to realize on an industrial scale,” offered Bonazzi responding to a webinar query on creating large volumes. He projects a four to five year timeframe to reach larger capacities.
Currently Aquafil has a capacity of about 100M pounds annually of ECONYL. “It is not a small amount, and we are growing every year, but it still represents a fraction of the nylon market,” Bonazzi shared. “We are still at the beginning.”