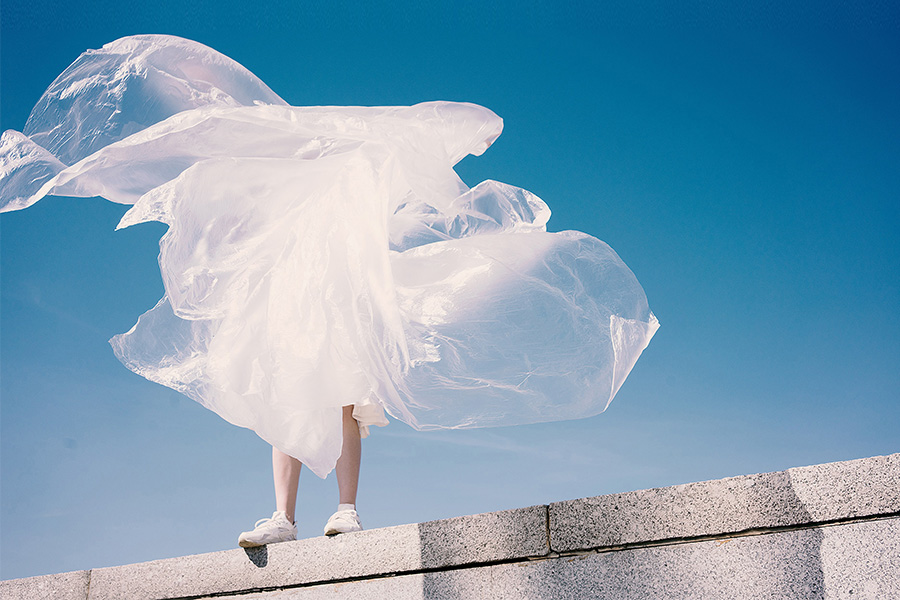
Circularity 3 Ways
A Smorgasbord of Textile Tech to Counter Climate Change.
Circularity 3 Ways
A Smorgasbord of Textile Tech to Counter Climate Change.
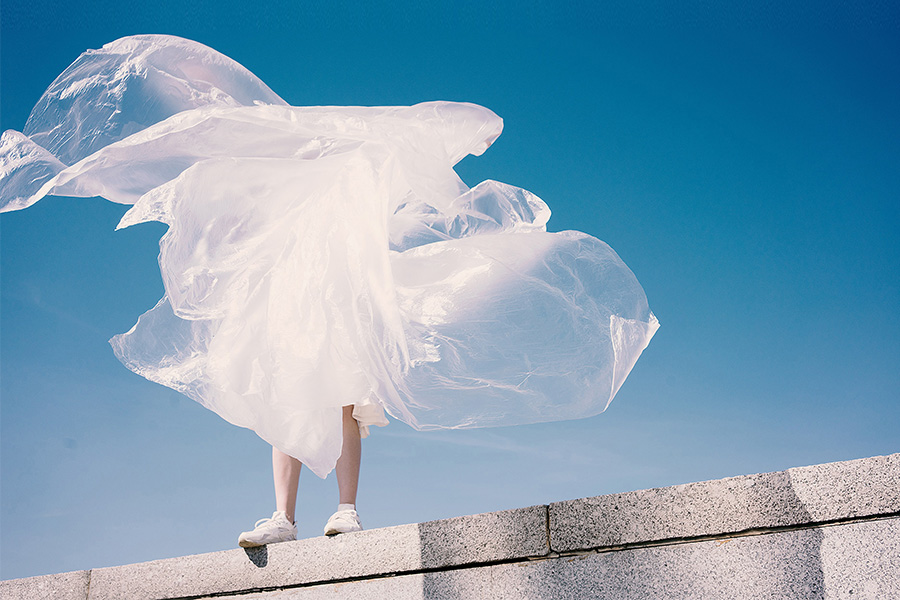
A recent New York Times article titled, “Climate Report Card Says Countries Are Trying, but Urgently Need Improvement,” noted that while the rate of greenhouse gas emissions (GHGe) has slowed, it needs to drop some 60 percent by 2035 to keep global warming at safer levels.
As we acknowledge the textile industry’s significant contribution to the problem, it’s clear that no one approach to reducing our industry’s raw material inputs, tons of waste, and GHGe will suffice. Happily, there’s an expanding menu of textile technologies working towards circular solutions to the climate challenge.
Organic Replacement for Plastic
Squitex is a protein-based, bio-derived, tunable fiber inspired by squid ring teeth, which exhibit highly durable, flexible and self-healing functionalities. Dr. Melik Demirel, the Huck Chair in Biomimetic Materials, director of the Center for Research on Advanced Fiber Technologies, and professor of engineering science and mechanics at Penn State University, led team research into the development of fibers with these characteristics as a biodegradable replacement for petroleum-based fibers.
“Five years ago, we decided that microfiber pollution was a big problem,” says Demirel. In 2017, Demirel, Dr. Gozde Senel Ayaz, and Dr. Benjamin Allen co-founded Tandem Repeat Technologies, Inc., with a portfolio of patents for creating fibers that replicated the properties of Squid Ring Teeth.
It turns out that the structural protein found in squid ring teeth is similar to the protein found in silk. By analyzing its genetic makeup, the team was able to use bacteria to grow a bio-synthetic version on a large scale, and to alter its various characteristics to create fibers with strength, stretch, and self-healing qualities.
“We are going back to nature to produce a biodegradable textile, using nature’s universal building blocks: lipids, protein, and sugar,” Demirel explains.
The bio-synthetic squid ring teeth proteins are extracted from the bacterial solution as a powder, which is dissolved in a solvent and wet spun in a process similar to lyocell. Squitex’ manufacturing process exhibits fewer environmental impacts and a smaller carbon footprint, compared with fibers made from fossil fuels. “Bacterial fermentation is a low-temperature process,” Demirel points out.
Winner of the 2021 Microfiber Innovation Challenge, Squitex can be used to create self-healing textiles, or to coat other fibers to limit microfiber shedding.
Squitex fiber blends well with natural or cellulosic fibers, and provides elasticity for activewear or denim without polyurethane’s biodegradability issues. The company is currently on the path to creating a capsule apparel collection, using a woven blend of Squitex and cotton; with a denim launch to come in 2024, and active wear in 2025.
“Our partners are lined up,” Demirel reveals. “But our challenge is the cost of Squitex vs. plastic.” His hope is to reach cost parity with lyocell.
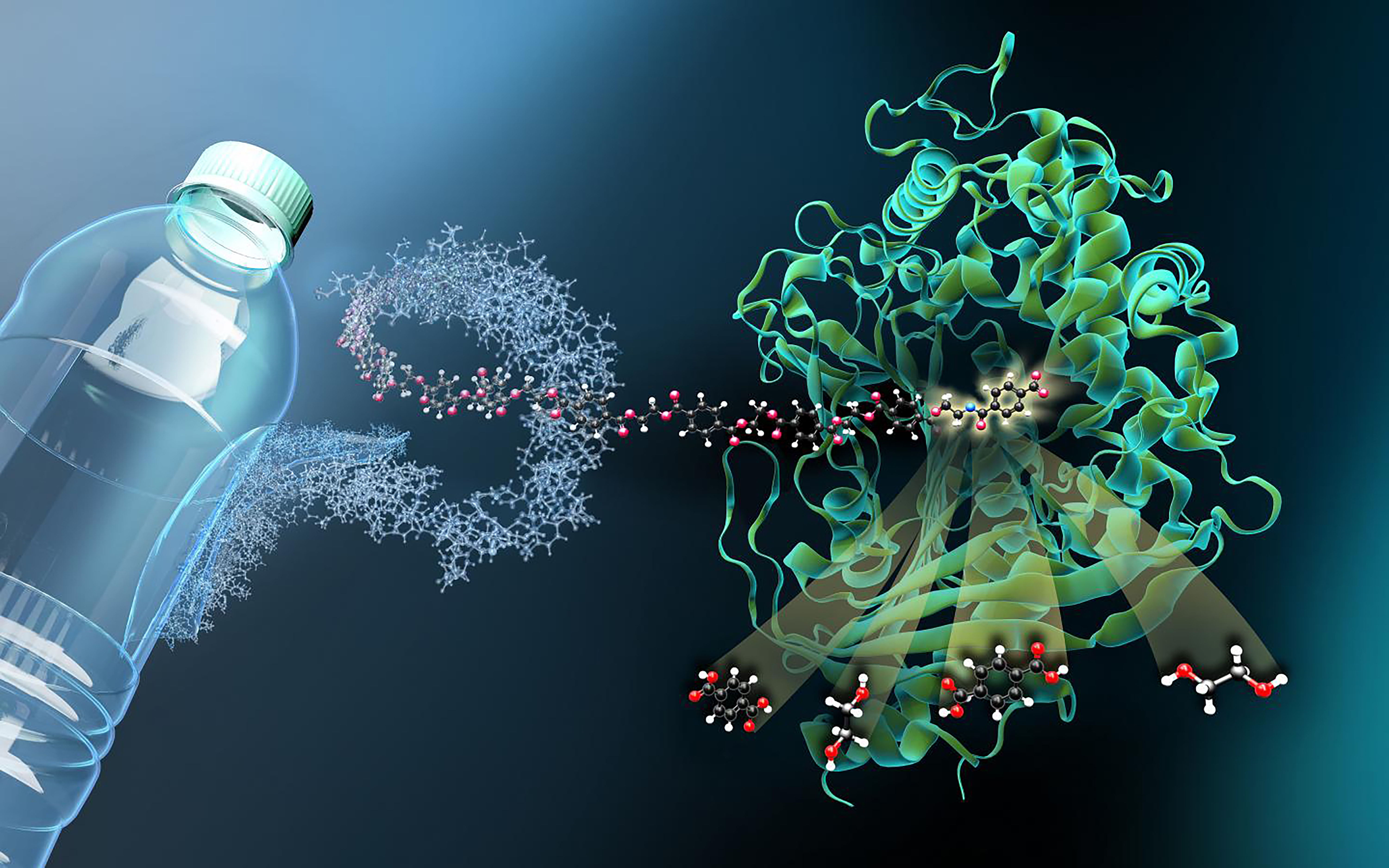
Creating Textiles from CO2 Emissions
Rubi Laboratories, Inc., is not the first biotech to recognize the potential for using CO2 emissions as a feedstock to create products; but the San Francisco Bay startup’s unique technology is the first of its kind to convert CO2e into cellulosic textiles through a cell-free, enzymatic biocatalysis process.
In other words, Rubi’s enzymatic process speeds up biochemical reactions to efficiently capture and convert CO2 into cellulose, which then can be made into pulp, fibers, yarns, and eventually fabrics.
CEO Neeka Mashouf explains, “Rubi’s patent-pending technology is built to capture CO2 from the waste streams of manufacturing facilities at any concentration using its proprietary enzyme system. Our goal is for the materials in the system required for carbon capture to be regenerated in its process, designed to be cyclical, rather than linear, in production.”
“The CO2 molecule is then transformed through a cascade of biochemical reactions,” she continues, “one-by-one shaping and crafting the base molecule that is polymerized into long cellulose chains.” The converted cellulose is used to create lyocell yarn for clothing and materials, with 100 percent of CO2 inputted to the end product.
Scientists Neeka and her twin sister Leila co-founded Rubi Labs in 2021 after inventing and prototyping the technology in a public biohacking lab.
According to Neeka, “We are currently deep in R&D which grants us the opportunity to experiment, learn and optimize our processes. We’ve run through the whole CO2-to-cellulose process and done it successfully. We’ve made yarn and tested it in textile settings. Rubi’s first material is lyocell, which we intend to get to price parity with standard man-made cellulosic fibers at scale.”
The company is in pilot partnerships with brands like Reformation, GANNI, Nuuly, H&M, Patagonia and Walmart. “Rubi and Walmart both believe all customers should have access to sustainable, affordable apparel—this is something that is critically important and top of mind for both teams as we work together on our initial pilot partnership,” Neeka insists.
According to the sisters, Rubi’s technology holds the potential to create planet-positive products beyond textiles, such as building materials, packaging, and food; creating a world where global supply chains are symbiotic with the planet.
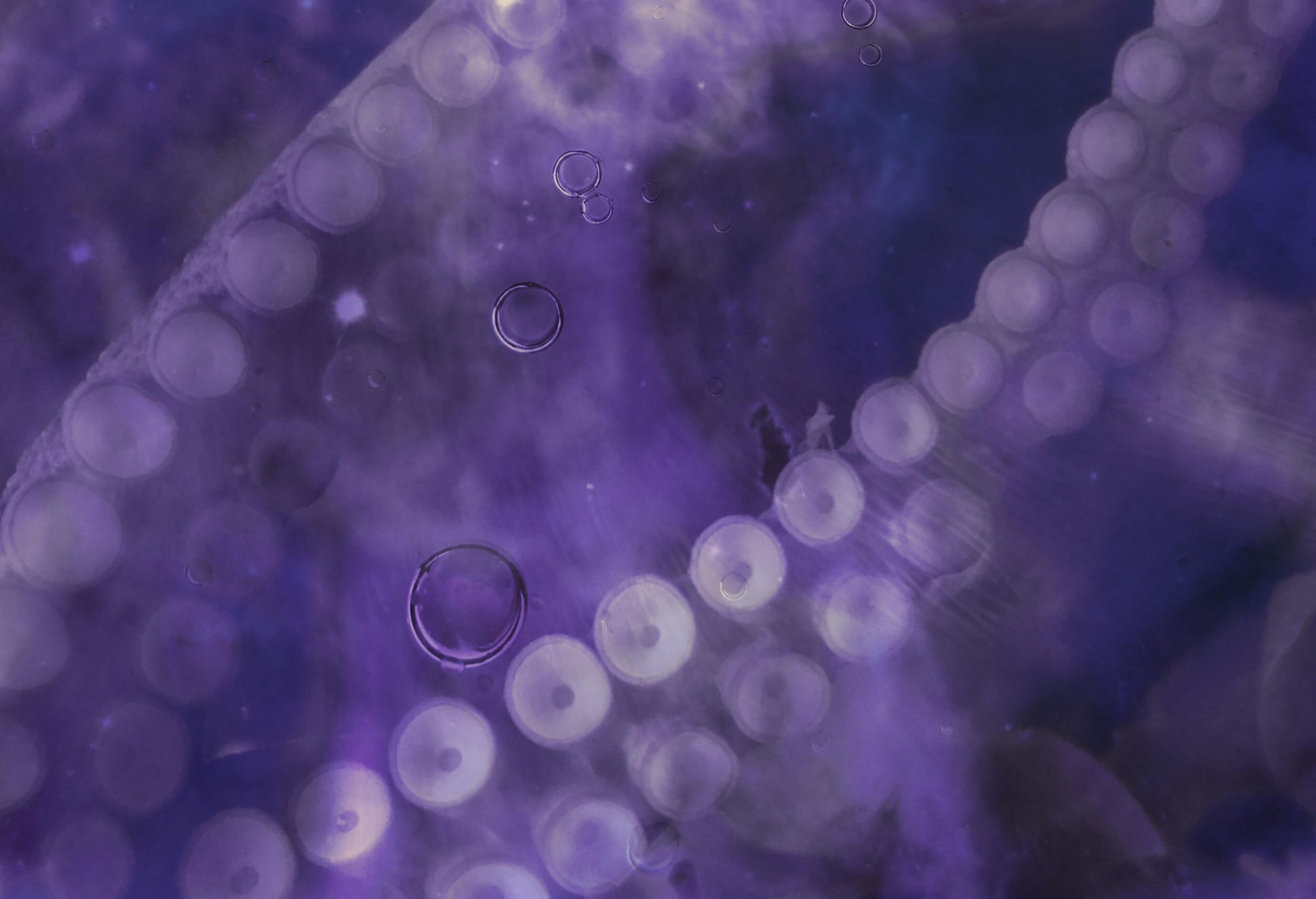
Recipe for Endless Plastic Recycling
Samsara Eco, an Australian startup described as an “enviro-tech,” has found a way to infinitely recycle plastic by using enzymes. The company’s proprietary technology creates bespoke enzymes to break down plastic polymers into their monomers, or original building blocks. The monomers can then be used to create virgin-quality plastic products.
“Our process is infinite because through reverting complex polymers into simple monomers, we can make new, virgin-grade plastics without ever needing fossil fuels again. A truly circular process,” says CEO Paul Riley. Samsara Eco’s technology is applicable to mixed plastics and fibers, including polyester, nylon 6,6, polypropylene, and polyurethane.
Samsara Eco launched in 2021 in partnership with the Australian National University (ANU), whose Jackson Lab/Research School of Chemistry are global leaders in enzyme-based depolymerization.
Current mechanical and chemical recycling technologies for fossil fuel-based textiles are considered inadequate; the bulk of rPET used in textiles comes from bottles. Repeated mechanical recycling of textiles results in poor quality fibers that are eventually down-cycled; while chemical recycling requires the use of solvents and high heat.
“Samsara’s enzymatic process is a low-heat and low-pressure process delivering a virgin equivalent polymer, with a carbon footprint substantially lower than virgin plastic while also meeting market price. The Samsara enzymatic process separates out any contamination including colors and additives, allowing for the recycling of a wider range of feedstocks. This includes our ability to process mixed polymer garments and deliver fiber to fiber recycling,” notes Riley.
In late 2022, Samsara Eco raised $56M in its Series A funding, which is being used to fund its first R&D facility, to be located in regional New South Wales. “We are in the process of scaling up our operations and hope to produce our first enzymatically recycled clothing at a small scale in the next 18 months,” says Riley.
Activewear brand Lululemon has taken a minority stake in Samsara Eco, and will partner with the company to create infinitely recyclable textiles, with the focus on polyester and nylon 6,6. “Nylon 6,6 is one of the textile and fashion industries’ most commonly used materials because its complex chemical structure makes it very versatile and resilient,” explains Riley. “But it’s also difficult to break down and recycle.”
Samsara Eco is also looking into expanding its operations into Europe and North America. Currently creating polyester fiber in its pilot plant, the company’s goal is to create enough capacity to recycle 1.5 million metric tons of plastic annually by 2030.
In conclusion, achieving circularity within the textile industry begins with innovative technologies such as these. “We must recognize that all materials have impacts, and that none are inherently good or bad. Instead, how materials are sourced and managed will determine their true impact,” writes Jon Smieja, VP Circularity for GreenBiz Group, in Circularity Weekly.
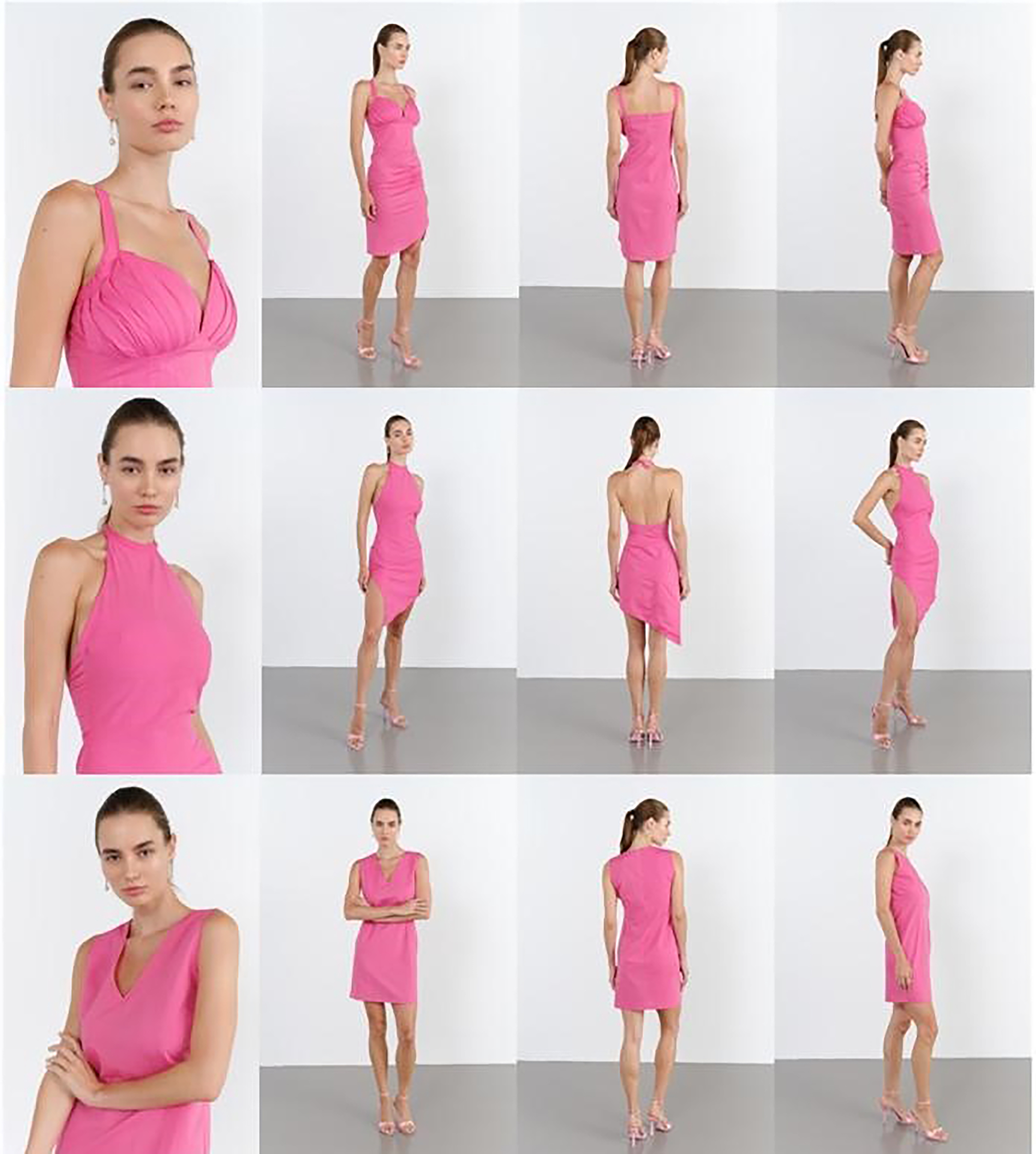