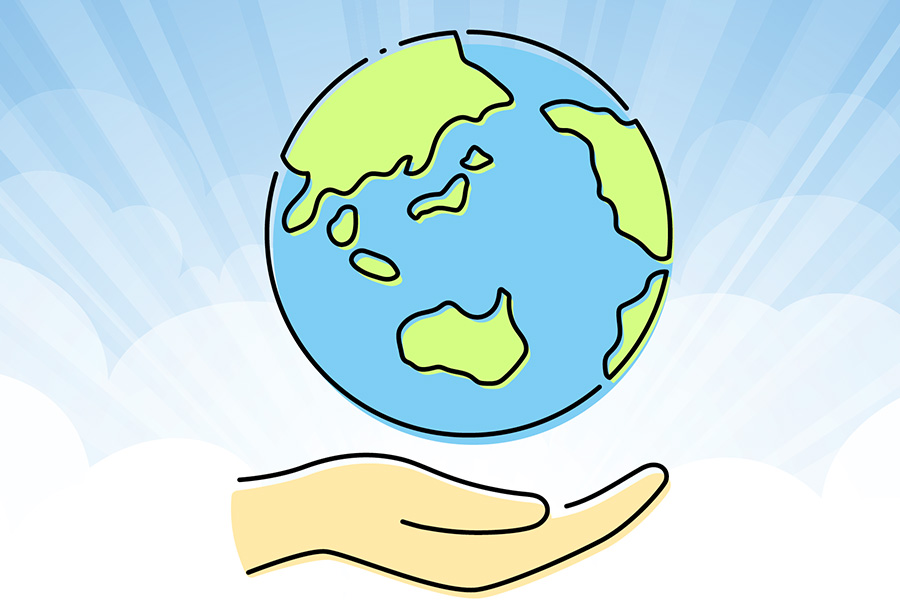
Planet-Positive Progress
With a Collective Effort, Industry Achieves a Deeper Shade of Green.
Planet-Positive Progress
With a Collective Effort, Industry Achieves a Deeper Shade of Green.
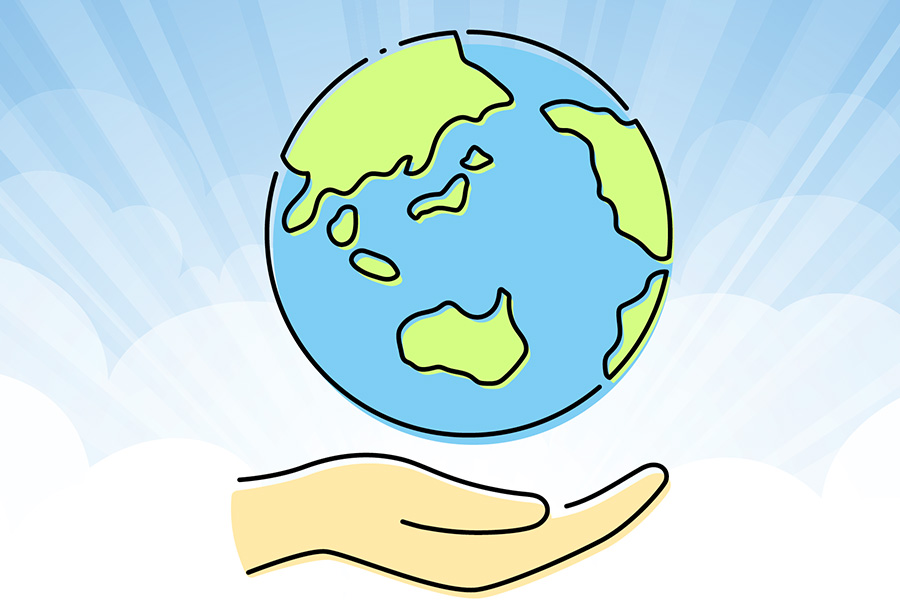
How long does it take for the textile industry to move the needle forward on sustainability?
Some would say “too long,” and depending on your sense of time, that response rings true, especially when you consider that it was 30 years ago when Polartec, in partnership with Patagonia, first launched recycled fleece, with fabric made from discarded plastic bottles in a color described as “soda-bottle green.” And it was the early 2000s when an idea started to form among leaders in the outdoor community for an OIA Sustainability Working Group and sparked the development of the Eco-Index in 2006. Another turning point in sustainability momentum within textiles came over a decade ago back in 2011 when Greenpeace announced its Detox campaign, taking aim at the industry to reduce hazardous toxins and motivating a new era of materials based on green chemistry.
However, if you shift your perspective and reflect on the trajectory of sustainability within our industry then maybe the answer “too long” doesn’t give the textile community its due. Indeed, the needle has moved significantly; conversation now revolves around universal issues of climate and circularity along with an escalation of highly sophisticated technologies like carbon capture that level up the sustainability factor of materials for activewear and athletic footwear made from an ever-widening range of eco-alternatives without downgrading performance. Traceability and transparency via blockchain and digital product passport concepts once unthinkable are now being adopted throughout the supply chain.
Of course, there is still much to be done. A quick internet search brings a flood of statistics. For example: The apparel industry’s global emissions will increase by 50 percent by 2030 according to Earth.org; The most recent EPA data reveals that in America, 66 percent of all unwanted clothes and textiles are landfilled, with individuals generating over 17 million tons of textile MSW (Municipal Solid Waste) per year. The fashion industry is responsible for 1.8 percent of global greenhouse gas emissions, the Apparel Impact Institute recently reported. And on it goes.
Faced with these obstacles, today’s textile leadership is realizing that a collective effort is critical to reaching sustainability goals. For an industry that has long put up silos, this idea of breaking down barriers and coming together to problem solve for shared solutions is radical. As such, nowadays textile execs find themselves in fields discussing regenerative practices with farmers and nowadays it’s not surprising that suppliers form bonds with competitors in a spirit of cooperation for the greater good.
It is often stated that sustainability is a journey not a destination. With eco-responsible targets fast approaching and milestone ESG goals in 2030 and 2050 on the agenda, textile execs are laser-focused on achieving a deeper shade of green for product, profits and the planet.
Power in Partnership
This Fall Hyosung is presenting expanded bio-based, recycled and multi-function offerings, building on its established strong traceable sustainability story. The company’s new Bio-Based elastane range includes a variety of options for the yarn to be made with a higher content of renewable resources. Hyosung was the first company to commercially introduce USDA and SGS-certified creora Bio-Based elastane made with 30 percent renewable resources in 2021. The manufacture of 1kg creora Bio-Based elastane reduces its carbon footprint by 20 percent as compared to the production of 1kg of conventional spandex, according to an independent third party LCA performed for the company.
“We are very excited to follow the success of our creora Bio-Based elastane with a second phase of third-party certified fibers made with a higher content of renewable resources to meet consumer demand for traceable, bio-based products,” said Simon Whitmarsh-Knight, Hyosung global marketing director - textiles.
In addition, Hyosung is presenting new innovations in its GRS-certified, 100 percent post-consumer recycled regen Ocean nylon made from discarded fishing nets at Fall trade events. To help fight ocean plastic pollution, Hyosung and Dimension-Polyant, a global sailcloth producer and maker of XPac waterproof laminates for bags and packs, have collaborated to introduce a fully sustainable version of Dimension-Polyant’s successful X-Pac VX21 four-layer laminate.
The X-Pac VX21 four-layer laminate face fabric is constructed with regen Ocean nylon strengthened by Dimension-Polyant’s patented X-PLY fiber reinforcement technology made with post-consumer recycled PET. A lightweight taffeta backing, also made with 100 percent recycled post-consumer PET, provides enhanced stitch holding. As with all X-Pac materials, the VX21 laminate is made in Dimension-Polyant’s 100 percent carbon neutral plant.
“We have been waiting for just the right 100 percent recycled material that meets our durability standards and sustainability story to collaborate with on the next phase of our best-selling VX21 laminate,” said Taylor North, head of technical fabrics, Dimension-Polyant U.S.
Roman Park, Hyosung performance leader - nylon and polyester, added “I believe that collaboration along the supply chain is how great products are created and we are thrilled that Dimension-Polyant has joined our growing number of valued partners who’ve adopted our specialty fibers.”
Pushing sustainability to the next level via partnerships is a Cordura priority. A recent collaboration with longstanding brand partner CamelBak serves as a good example of driving eco-innovation through collaboration. Cordura’s re/cor Recycled Nylon 6,6 (RN66) is the fabric behind CamelBak’s launch of its most sustainable backpack collection yet.
“When the Cordura brand launched its latest Cordura re/cor Recycled Nylon 6,6, collection, our design team at CamelBak knew there was a huge opportunity there. We were one of the first brands to ideate and implement a collection around it – and this time, for a new category: adventure-travel,” explained Emma Axtell, CamelBak product manager.
The new A.T.P packs feature a combination of Cordura re/cor Recycled Nylon 6,6, (RN66) and Recycled Nylon 6 (RN6), which is 100 percent post-industrial recycled fiber material that is Global Recycled Standard (GRS) certified. The pack body and bottom are both 100 percent post-industrial recycled 210 denier Cordura re/cor Recycled Nylon 6,6, (RN66) fabric. The pack liner is 100 percent post-industrial recycled 210 denier Cordura re/cor Nylon 6 fabric.
Other sustainable materials like aluminum hardware, recycled buckles, packaging and hangtags are made of recycled materials. “The undyed A.T.P. in both 20- and 26-liter variations are the first products ever to meet CamelBak’s Platinum Badge on our sustainability rating system. The undyed colorway uses less water, power, and emits fewer greenhouse gas emissions compared to traditional nylon manufacturing processes,” Axtell noted.
“The Cordura re/cor RN66 fabric collection challenges the throw-away mentality within the textile industry, making it easier for consumers to understand how one ingredient and quality craftsmanship can allow them to get the most from their gear and apparel,” said Cindy McNaull, Cordura brand business development director. “Our authorized mill partner Dong Jin International was instrumental in helping bring this fiber innovation to life, supporting its development efforts for more than two years.”
Cordura re/cor RN66 fabrics are made from material recycled from INVISTA operations, so the materials are carefully controlled, according to McNaull.
Expanding the Innovation EcoSystem
Planet Agenda is the name of The LYCRA Company’s sustainability framework that touches every aspect of its business and is built on three pillars: product sustainability, manufacturing excellence and corporate responsibility, and in addition, aligns with five of the United Nations Sustainability Goals (SDGs). In its latest Planet Agenda Update, the company reported on its sustainability progress versus 2030 targets. Steve Stewart, chief brand and innovation officer, The Lycra Company, stated, “We are proud of the advances we have made in pursuit of our 2030 goals. At the same time, we recognize the challenges in front of our industry are great, and we can only meet them by working together with our customers, suppliers, and third-party partners.”
Jean Hegedus, The Lycra Company’s director of sustainable business development, added,
“We see Planet Agenda as a shared endeavor with our customers and partners, united in the belief that to have a healthy business we must have a healthy planet.”
The report outlined three key outcomes. One highlight is a notable reduction in greenhouse gas emissions driven in part by the company’s Maydown, Northern Ireland site converting its purchased electricity to renewable sources through Energy Attribution Certificates (EACs). Three manufacturing sites achieved third-party verified top-quartile performance in the Higg Facility Environmental Module (FEM), with two achieving the same level in the Higg Facility Social & Labor Module (FSLM). Additionally, successful collaborations launched with industry partners on the leading edge of material science.
In the pursuit of replacing petroleum-based raw materials, The Lycra Company has entered a partnership with Qore, a joint venture between Cargill and HELM, allowing the company to produce at scale a Lycra fiber made from 70 percent renewable sources.
“Sustainability is really a collective effort,” said Julien Born, The Lycra Company CEO in a promotional video on the company’s website. “This kind of partnership is what brands and retailers are looking for.”
Lycra fiber is made with Qore’s branded Qira, a renewable Iowa field corn product. The bio-derived Qira will be converted into PTMEG, the key ingredient used in Lycra fiber, and will be available in large scale quantities in the fourth quarter of 2024, according to the companies.
The Lycra Company is also collaborating with HeiQ this year, and have jointly introduced Lycra naturalFX technology, a coating that can be applied to 100 percent cotton fabrics and garments for a soft hand feel and added shape retention. The company is also now the exclusive global distributor for HeiQ AeoniQ fiber, a high-performance cellulose with the potential to be carbon negative.
CovationBio, known for its Sorona, Susterra and Zemea product lines, along with the company’s supply chain partners, are reaping environmental benefits from regenerative practices and farm-to-finished product innovation strategies.
These efforts were showcased in a hands-on field day that took place in the heart of America’s Corn Belt this summer hosted by CovationBio CEO Dr. Michael Saltzberg, Primient chief sales officer Chris Guild, Truterra president Tom Ryan, and Kelly Garrett, a local farmer at Garrett Land & Cattle and co-founder of XtremeAg.farm.
“This is the first time we’ve had the chance to gather our value chain partners where our bio-based production begins—literally in a corn field,” said Saltzberg. “We wanted everyone to experience the win-win that we are creating by helping to replace fossil fuel-based materials with a plant-based alternative that is not only a renewable resource, but that also is being produced in a way that helps capture carbon from the atmosphere. That type of circularity is an excellent example of how we are doing our part to fight climate change.”
Ryan remarked, “Attendees saw first-hand how we’re bridging the gap between farmers and companies with sustainability goals who choose agriculture to be a part of their toolkit of solutions,” said Ryan. “I look forward to our continued work together to advance supply chain sustainability and scale on-farm practice change.”
Truterra, LLC, is the sustainability business of Land O’Lakes, Inc., specializing in creative solutions to reduce carbon emissions. Primient’s sustainable agriculture program with Truterra began in 2018 and currently includes over 1.2 million acres of sustainably grown row crops in the U.S. Midwest.
Strides in Sustainability
Eastman’s eco efforts range from brand partner collaboration to new facilities. Joy Gruver, biz development manager Fibers Division shared news of Patagonia’s new collection of super-soft performance shirts made from a versatile blend of Naia Renew staple fiber and recycled polyester. Naia Renew fibers are produced from renewable wood pulp and recycled waste materials.
Product includes a men’s Short-Sleeved Capilene Cool Trail shirt and women’s Capilene Cool Trail shirts in three styles. All feature moisture-wicking performance and comfort stretch. “These tops are perfect for outdoor activities and all-day wear,” said Gruver.
According to Eastman information, over 260 million metric tons of plastic are being thrown away and only 12 percent of that waste is currently being recycled. Eastman’s molecular recycling technology transforms hard-to-recycle plastics into new materials, cutting greenhouse gas emissions, and creating value from waste.
At its first methanolysis facility, currently under construction at the company’s corporate headquarters and Kingsport, TN manufacturing site, Eastman will be able to accept plastic waste that today often ends up in the environment and will convert this waste into brand new materials with recycled content. The Kingsport facility will use more than 100,000 metric tons of plastic waste every year that can’t be recycled by traditional methods. The facility is expected to be completed later this year.
This is the first of three planned methanolysis facilities. Earlier this year, Herve Morin, president of the Normandy region of France traveled to Eastman offices. Plans are in the works for a methanolysis facility to be constructed in Normandy, France, that is expected to be operational in 2026.