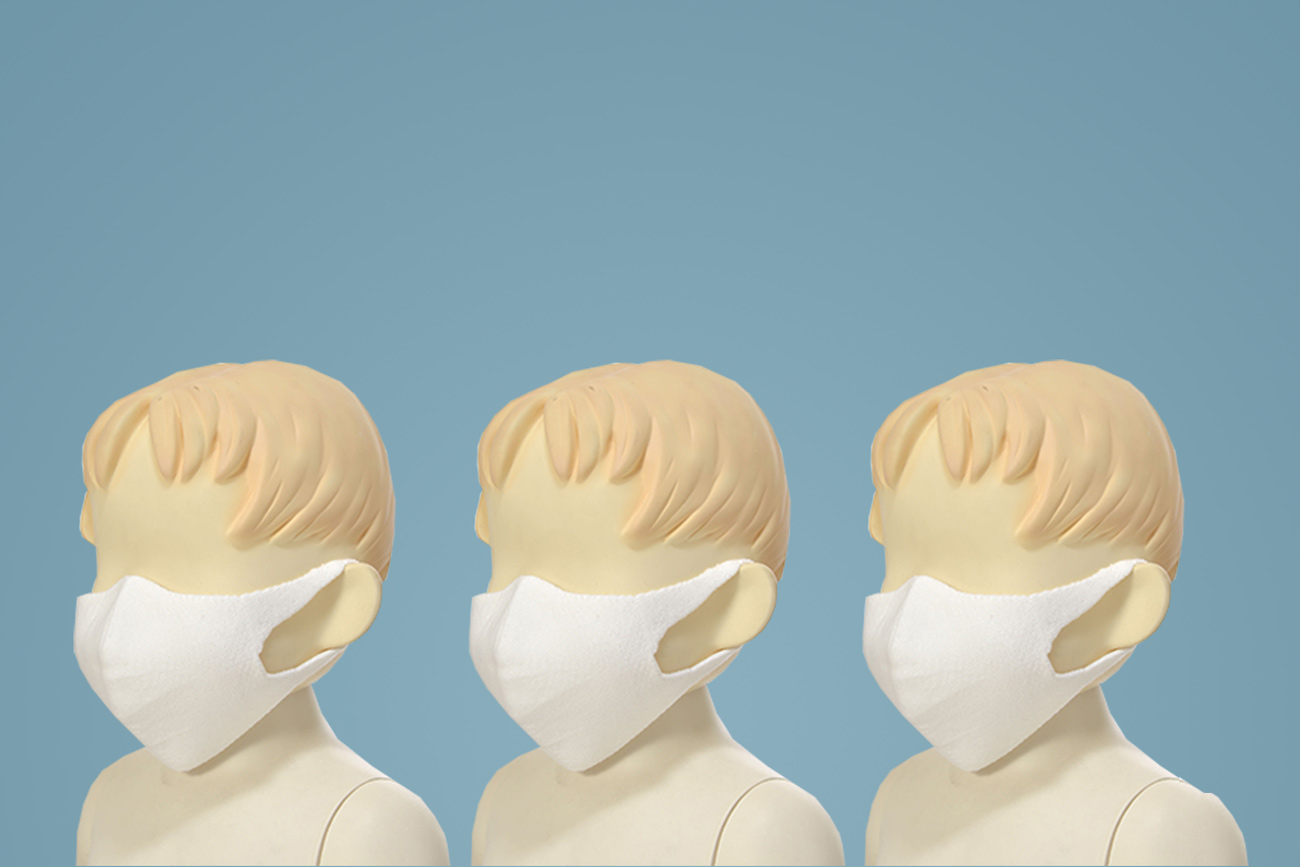
How the Past Informs Mask Development Today
How the Past Informs Mask Development Today
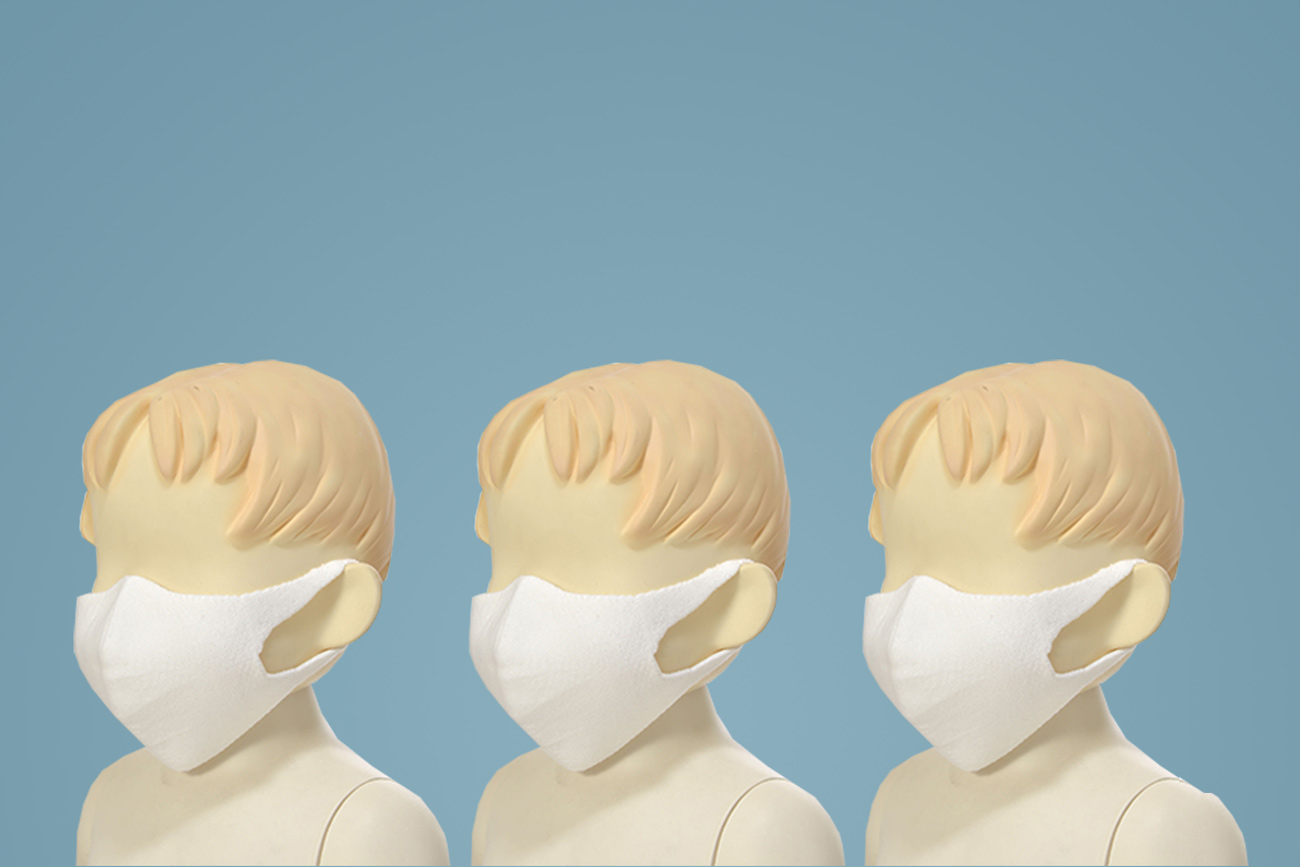
“The principles used in modern technology today in regard to safety and mitigating safety started a long time ago,” explained Dr. Bryan Ormond, assistant professor Textile Protection & Comfort Center at the Wilson School at College of Textiles, North Carolina State University (NCSU). “There are parallels between historical response to disease and our crisis to today. We can learn a lot from the past and that enables us to be better equipped to analyze this situation,“ said Ormond, who provided historical perspective on mask innovation in a talk during a NC State webinar series co-hosted by the IFAI titled, “Key Principles for Effective Protection with Masks & Respirators.”
Highlights of Ormond’s presentation included how Leonardo da Vinci advocated using wet cloths over the mouth to protect from disease, and how masks worn during the plague in the 1600s were shaped like large bird beaks, and that individuals carried sticks to point to people several feet away who they wanted to talk to – a precursor to social distancing. The first surgical mask came in 1857, and it was during the Manchurian plague of 1910-11 that a Dr. Lien-the Wu concluded that the virus was spread through the air. More recently, a designer/consultant for 3M in the 1960s, Sara Little Turnbull, is recognized as developing the N95 respirator during her research on expanded molded technology. Masks created for the mining industry and military applications also helped advance the category.
“What becomes clear is there is no single respirator that fits for every job application,” noted Ormond. “Fit is also key, and it all starts with the material.”
Ormond concluded, “We are going to see a shift to more, and different, size masks going forward.”
Indeed, Shima Seiki is already moving in that direction. The Japanese flat knitting solutions provider has produced 3D knitted masks for use at elementary schools and junior high schools in Wakayama Prefecture where the company is based.
The masks are produced at Shima Seiki headquarters by request of the prefectural government of Wakayama, in its effort to help alleviate the worldwide shortage of masks due to the spread of the COVID-19 coronavirus infection. Thus far, 8,000 children’s masks have been produced on Shima Seiki’s SVR093SP computerized flat knitting machine in 14 gauge. Although a conventional shaping machine, SVR093SP is capable of producing masks in one-piece without the need for sewing afterward. The children’s masks are available in three sizes to cover the wide age-range of school children.
The 3D form-fitted masks provide superior fit and comfort. Integral ear straps that are knitted along with the mask portion reduces stress on the ears, and require no further sewing for quick response production. A filter-pouch is knitted-in for inserting commercially available virus filters and other filtration fabrics. Holes are also knitted-in for insertion of wires that provide further adjustment for improved fit.
The knitted cotton masks can be washed and reused repeatedly. Unlike common non-woven surgical masks however, knit masks do not have virus- and pollen-filtration functionality. Their main purpose is to contain spray from coughing and sneezing, and for reducing exposure to allergens.
Mask making data is available for production on the company’s website: https://www.shimaseiki.com/