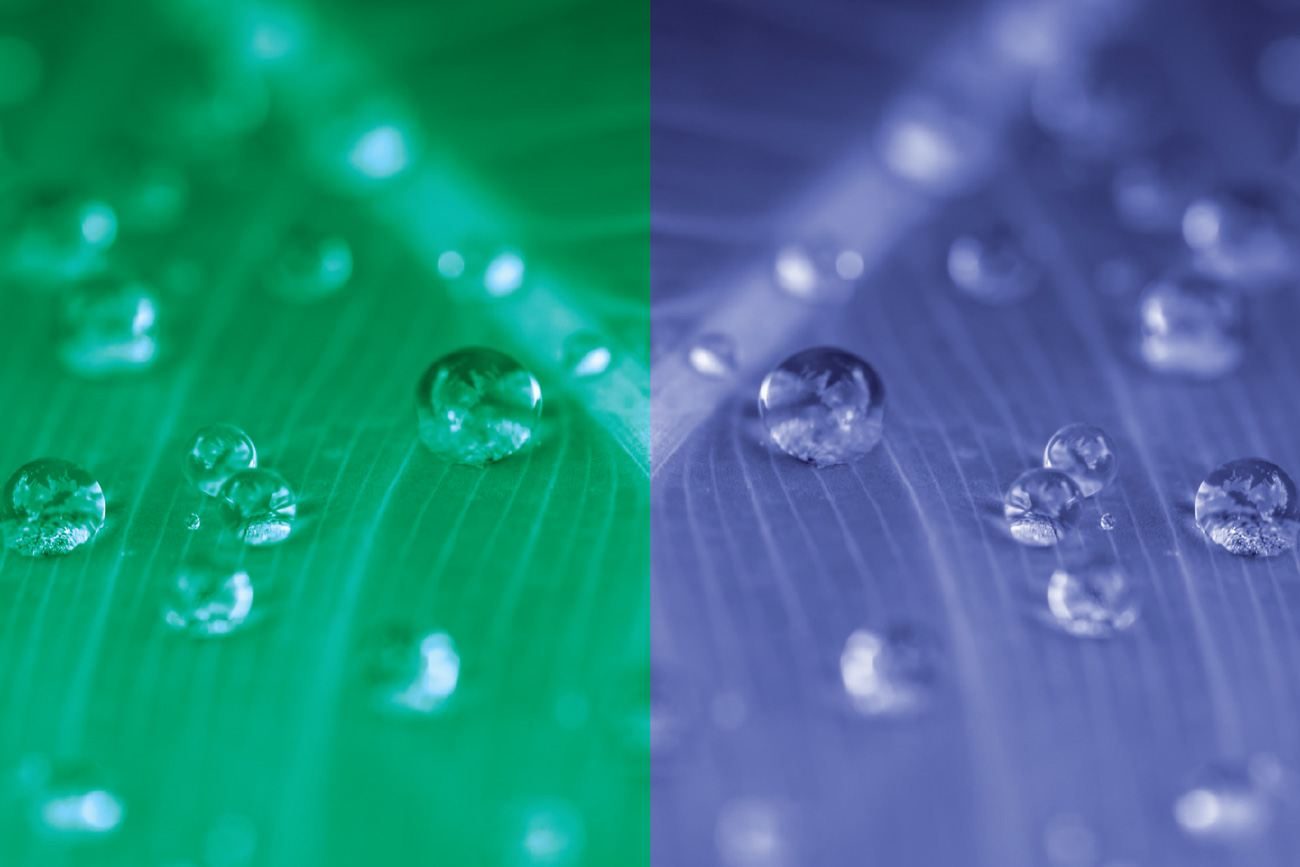
Good & Clean
As Earth-friendly Tech Developments Advance, Performance Improves.
Good & Clean
As Earth-friendly Tech Developments Advance, Performance Improves.
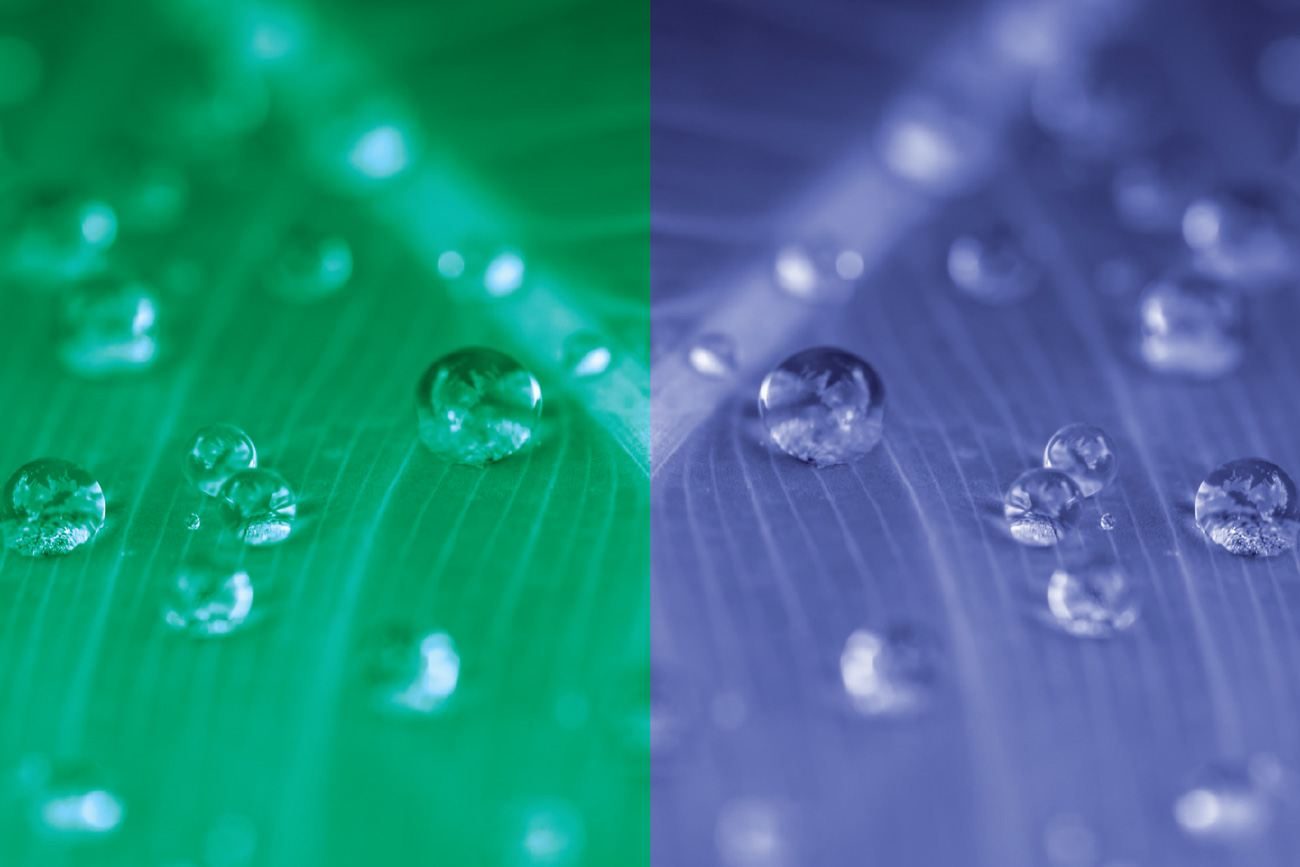
Sustainability has sparked a surge in responsible developments in functional fabrications in recent years, and continues to serve as a strong market driver. Yet despite recent advances in PFC-free and bio-based textile solutions, belief remains, especially among consumers, that going “green” means giving up performance.
Not any more. New earth-friendly textile finishes and membranes are raising the bar, often exceeding industry standards for water-repellency, breathability and durability, and as such raising consumer expectations on the ability of today’s textiles to be both high-tech performers and low impactors on the planet.
Textile execs point to climate as the critical factor influencing innovation, as a sense of urgency to curb weather extremes is accelerating material science research on reducing reliance on natural resources and lessen carbon emissions.
From fires and floods, to droughts and dangerous downpours, there is no escaping the role water plays in the big picture of climate change. This realization is central to Green Theme Technologies’ water-free EMPEL textile finishing process. “When you want to engage people with a sustainable option, incremental change is nice, but will not provide a big difference. You have to get to the root cause,” explained Martin Flora, VP business development, Green Theme Technologies, Inc., (GTT). “Water is the connective tissue between carbon footprint, effluent discharge, and toxic chemistry and is the main culprit, and foundational issue in our industry.”
By replacing traditional water-based wet finishing processes currently used to apply water repellents, dyes, and the EMPEL process, GTT, and its partner brands, can directly impact water pollution worldwide.
The technology is resonating, says Flora, who outlines a handful of recent GTT successes, that includes securing a Series A round of funding of $3.5M, inking a licensing agreement with YKK to use EMPEL technology on zippers, and a flurry of other developments taking shape, including footwear application (with major brands); FR innovation ( Department of Defense); new stain release testing; water-free dyeing for denim; and joint ventures to treat wool for a variety of properties.
“We’re really starting to ramp up now and expand,” said Flora.
Membrane Modern
Combining all-weather performance and sustainable solutions is the name of the game in membrane technology. This approach is the basis for eVent fabrics’ newest waterproof membrane, eVent BIO, that’s derived from highly renewable and sustainably sourced castor beans. Blended with virgin nylon, the bio-based membrane is light, durable and flexible while providing waterproof and windproof protection. eVent BIO is available with recycled face fabrics.
“As we evaluated a wide range of membrane technologies that met our sustainability targets, it was difficult to find a composition that provided the durability and waterproof protection users have come to expect from eVent,” said eVent fabrics president Chad Kelly. “We believe eVent BIO is one of the most sustainable and highest performing membrane technologies on the market today.”
Grown in semi-arid and sub-tropical climates in Asia and Africa, the castor bean is a fast-growing and naturally drought resistant perennial that doesn’t compete with food crops or contribute to deforestation. With its short growth cycle, the castor bean provides farmers with a highly profitable and renewable crop that can be harvested multiple times annually.
For Schoeller, Summer 2023 is all about responsibly-produced performance innovations that feature in the company’s new biocosmo line.
Schoeller’s Aerobrane membrane relies on an e-spinning platform. To produce an e-spinning membrane, a large number of ultra-light microscopic fibers are placed closely on top of each other, forming a clustered but firmly connected structure, that provides waterproofness and wind resistance with maximum breathability and high level of comfort.
Within the Schoeller Performance Collection, biocosmo zeros in on sustainability. The new Schoeller allweather three-layer fabric, for example, features Aerobrane membrane technology in combination with a high-quality, recycled polyamide and is finished with Schoeller’s water-repelling ecorepel Bio technology that is based on renewable raw materials.
The PFC-free, water-repellent ecorepel technology launched by Schoeller in 2012 has now been further developed to allow for successful application on textiles and apparel that are “dry clean only.”
Pertex has launched Pertex Shield Revolve, waterproof laminates where each layer of the fabric is made from a single polymer — a 100 percent recycled polyester. The mono-material composition makes Pertex Shield Revolve fabrics much easier to be recycled at the end of a garment’s life, thereby minimizing the waste of resources and reducing the overall environmental impact of the fabric.
“Conventional waterproof breathable fabrics are constructed from multiple different polymer layers, such as nylon, polyurethane, polyester, and fluoropolymers, which are laminated into a multi-material fabric,” said Steve Laycock, Pertex brand director. “These fabrics are very difficult to recycle at the end of the product’s life due to the major challenges of separating out the different polymers into their relevant waste streams.”
Pertex Shield Revolve fabrics are also completely free from per- and polyfluoroalkyl substances (PFAS), including the DWR and the membrane.
Rab introduced Pertex Shield Revolve in their Downpour Eco Jacket this Spring. A new 3-layer version for the Rab Arc Eco Jacket is now available. Apparel brands Klättermusen and Martini Sportswear have also adopted Pertex Shield Revolve for the upcoming season.
Environmentally-Focused Finishes & Treatments
Earlier this summer Polartec announced full use of Non-PFAS durable water repellent treatments. According to the company, that effort continues to be the focus, as Polartec works to switch to non-PFAS (per- and polyfluoralkyl substances) in its DWR treatments across its line of performance fabrics. This new weather protection fabric treatment will be used in Hardface, Power Shield, Power Shield Pro, NeoShell and Windbloc products. The technology will also extend to fleece and insulation treatments for greater moisture management on products like Thermal Pro and Alpha.
(Per- and polyfluoroalkyl substances - PFAS - are a group of man-made chemicals that includes PFOA, PFOS, GenX, and many other chemicals.)
“Trial results have exceeded even our expectations,” said Mike Rose, Polartec VP product development. “There is no loss of performance from a water repellency or durability standpoint.”
Chemours Teflon EcoElite is a finish containing 60 percent renewably sourced raw material derived from plant-based sources that offer durable water-based stain repellency on a range of fabrics. The bio-based and non-fluorinated stain repellent technology repels water and water-based stains and can be applied to a variety of fabrics without impacting feel or breathability.
The high-performance Teflon EcoElite finish is up to three times more durable than other non-fluorinated repellents, according to the company. The chemistry for Teflon EcoElite renewably sourced finish (Zelan R3) is bluesign approved.
Tidal Vision uses a biodegradable biopolymer from discarded crab and shrimp shells called chitosan to produce Tidal-Tex, a new non-toxic, eco-friendly water-based product. Tidal-Tex chitosan treatments with antimicrobial performance can be applied to fibers, yarn, woven or non-woven textiles.
A new partnership between Tidal Vision and Leigh Fibers spotlights sustainable performance. Tidal Vision, founded in 2015 and based in Bellingham, WA will open a 24,000 square-foot production facility within Leigh Fibers’ 1 million-square-foot Wellford, SC headquarters. According to the companies, this is Leigh Fibers first partnership in its 100-year history.
Leigh Fibers is one of the largest textile waste and byproduct reprocessing businesses in North America purchasing up to 300 million pounds of textile waste each year.
“Our mission is to create positive and systemic environmental impact,” said Tidal Vision CEO and co-founder, Craig Kasberg. “In the textile industry, to have the biggest impact it made sense to start with fibers treated at the top of the supply chain.”