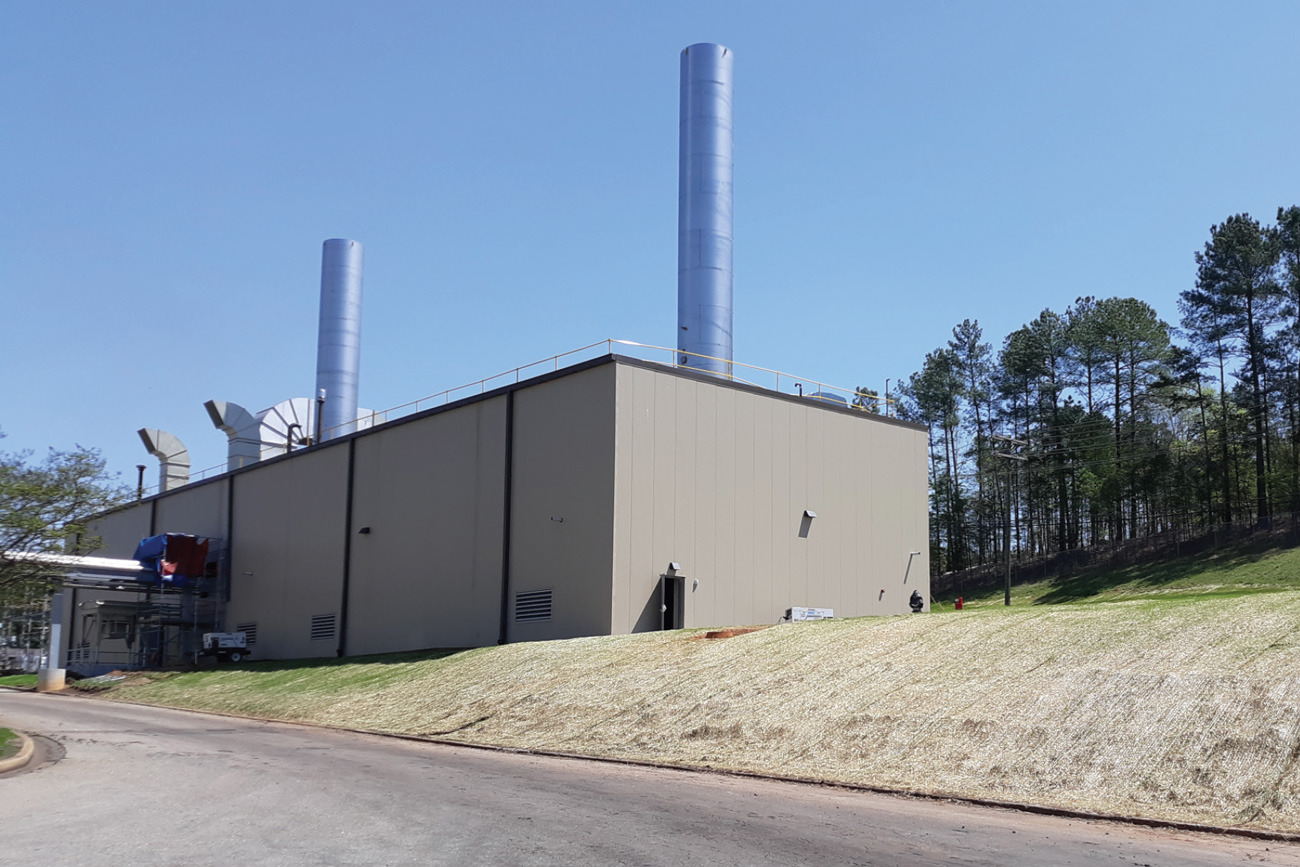
Generating Green Advantages
Milliken & Company Broadens Scope, Commitment to Sustainability.
Generating Green Advantages
Milliken & Company Broadens Scope, Commitment to Sustainability.
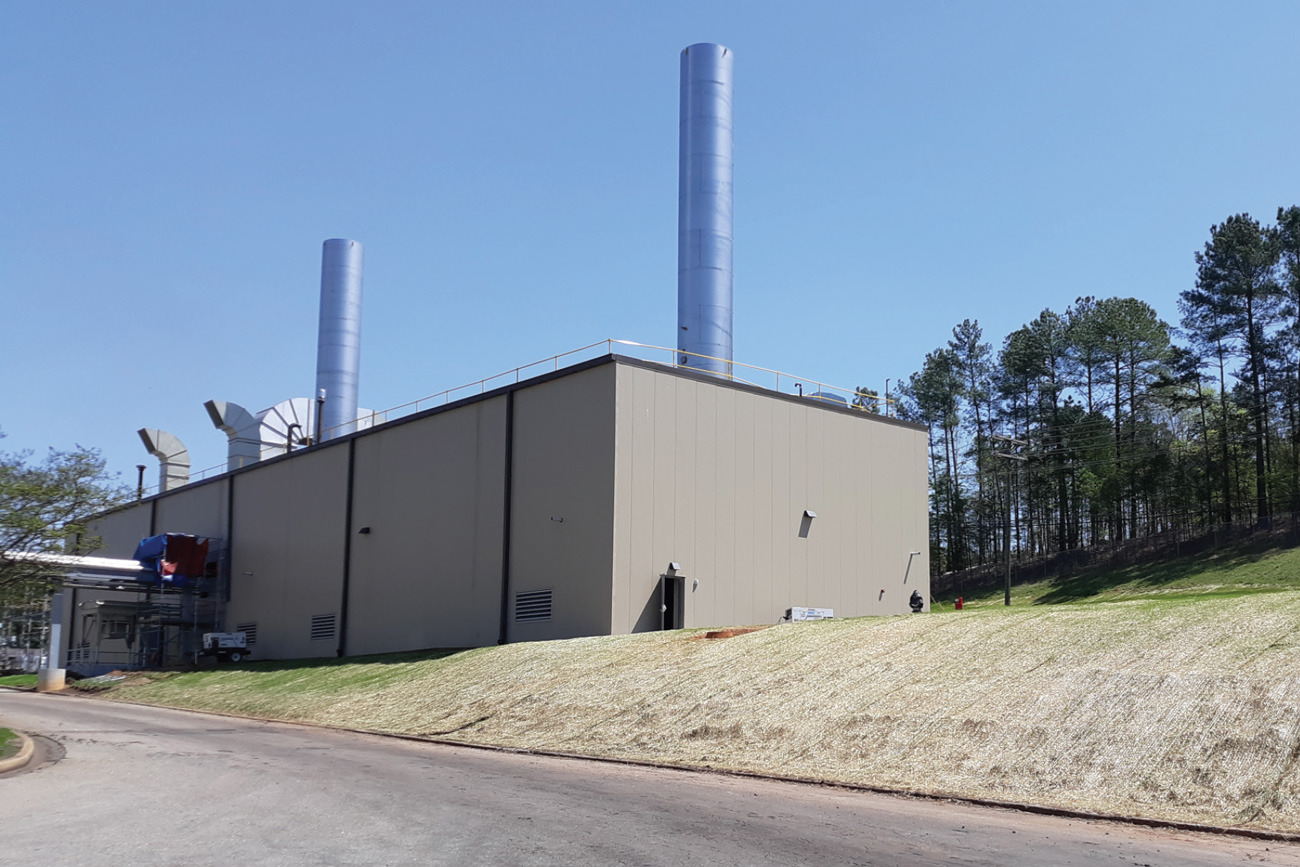
Sustainability is nothing new at Milliken & Company. The business was green when green was just a color in the rainbow. Founded in 1865, the company had a recycling policy in place in the 1900s and has been reporting on water usage and waste for decades all the while advocating for worker safety. What is new, however, is a broader focus on sustainable product development, complemented by heightened openness and transparency on eco-initiatives and a corporate commitment to meeting ambitious environmental responsibility goals.
For example, at global headquarters in Spartanburg, South Carolina, the manufacturer doubled solar capacity and completed a $1 million LED lighting upgrade. Changing the lighting reduced greenhouse gas emissions by 495 metric tons in addition to saving more than 1 million kilowatt hours of energy. Another example: The 156-year-old firm is publishing a comprehensive corporate sustainability report starting in 2018. Last year Milliken joined the UN Global Compact and the Alliance to End Plastic Waste.
These are big steps in advancing planet-positive business practices. But what feels really big is a brand new cogeneration project. The $25M investment in combined heat and power allows for reduced energy consumption by capturing wasted heat and increasing energy reliability by generating electricity onsite.
Main advantages of the cogeneration plant include: higher rate of efficiency, less dependency on coal, significant cost savings in the long run, and enhanced ability to meet corporate sustainability goals.
It is estimated that the initial investment in the cogeneration plant will result in savings of approximately $4M annually with a projected ROI in six to seven years.
“This project alone is projected to reduce greenhouse gas emissions for Milliken by 10 percent and reduce Milliken’s overall waste by five percent,” explained Jeff Strahan, Milliken & Company’s director of research, compliance & sustainability.
Reducing Greenhouse Emissions
The CoGen facility will be generating power and online by Fall 2021; It is currently in the commissioning phase (electrically connected). Located in Blacksburg, SC, the facility feeds two plants: the Magnolia textile plant and the Allen plant servicing the chemical division. Milliken corporation has 45 manufacturing locations globally, 28 are textile, eight flooring, seven chemical and two healthcare. Magnolia is one of the largest of the company’s textile plants; Allen is the largest chemical plant.
Once this cogeneration plant is up and running, coal will only be used as a backup energy supply for emergencies across the company. Milliken looks to continue to find ways to reduce greenhouse emissions, with solutions such as how to advance management of biosolids and make significant progress in waste reduction goals, according to company reports. In the latest CSR, the company aims to cut emissions 25 percent by 2025 against a 2018 baseline.
“Since I have joined Milliken, we have always had environmental goals. I remember hearing about water goals and seeing charts of water used per kg of product over time when I joined the company,” said Strahan, who joined Milliken a decade ago. “I think what has changed under Halsey Cook’s leadership is our openness and transparency around the topic. This CoGen project feels really big to me, but so does having a corporate sustainability report. So does our relationship with PureCycle and Polartec crossing the 1.5 billion bottle mark.”
Like most textile businesses, even those who have a long history of green practices, keeping pace with eco advances is a continuum of and ever-changing sustainable standards. The new cogeneration project represents by far the largest initiative in scope and investment the company has made. And, yet, executives realize there is more to do.
“We’re learning,” stated Strahan, explaining that every head of development across divisions meets monthly to discuss the gateway process and requirements for a sustainability assessment and application. “Textiles play a big role in enabling a circular economy,” said Strahan. “We are part of the problem so we have to be part of the solution.”