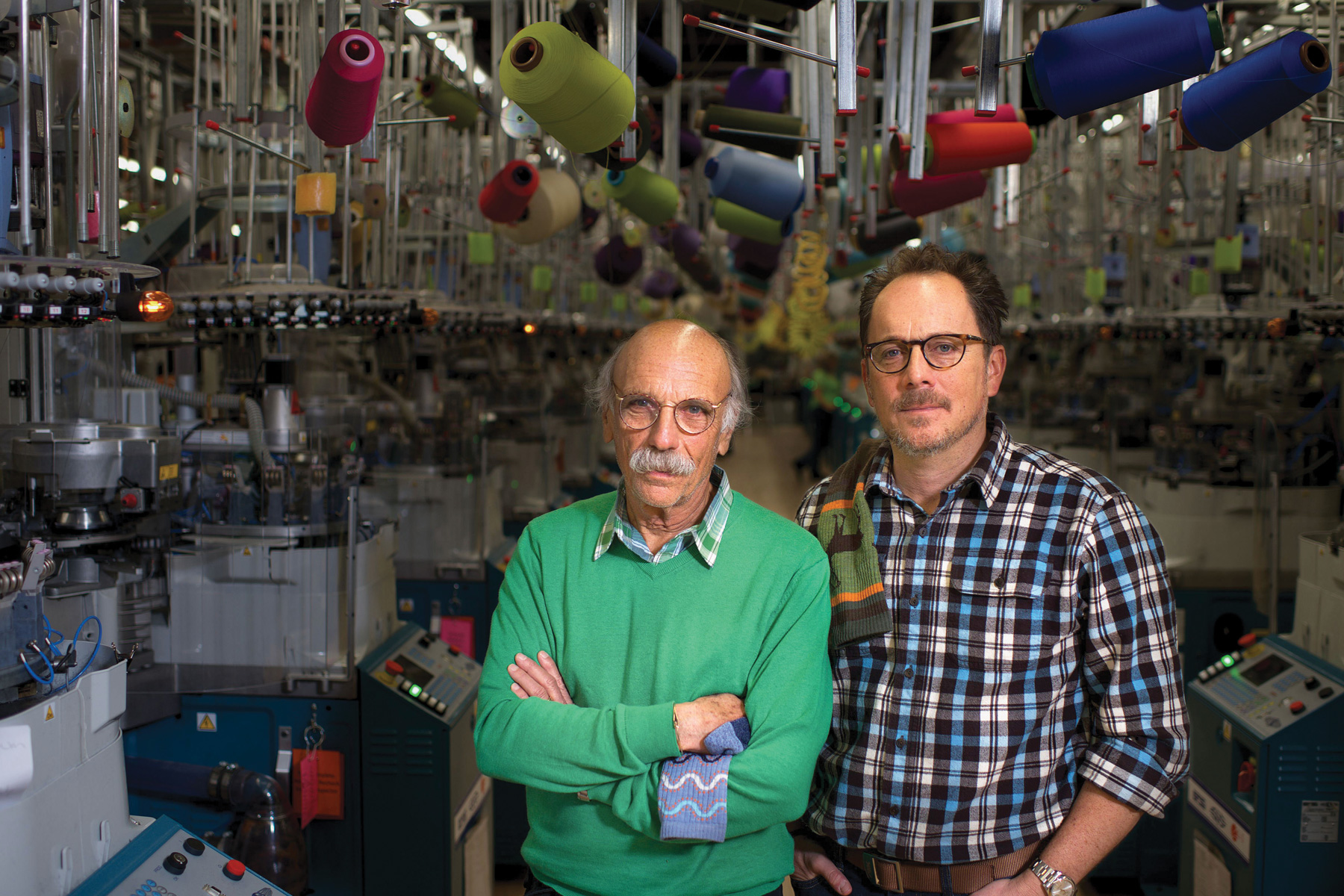
Finding Traction
How Suppliers are Moving the Needle in Domestic Make.
Finding Traction
How Suppliers are Moving the Needle in Domestic Make.
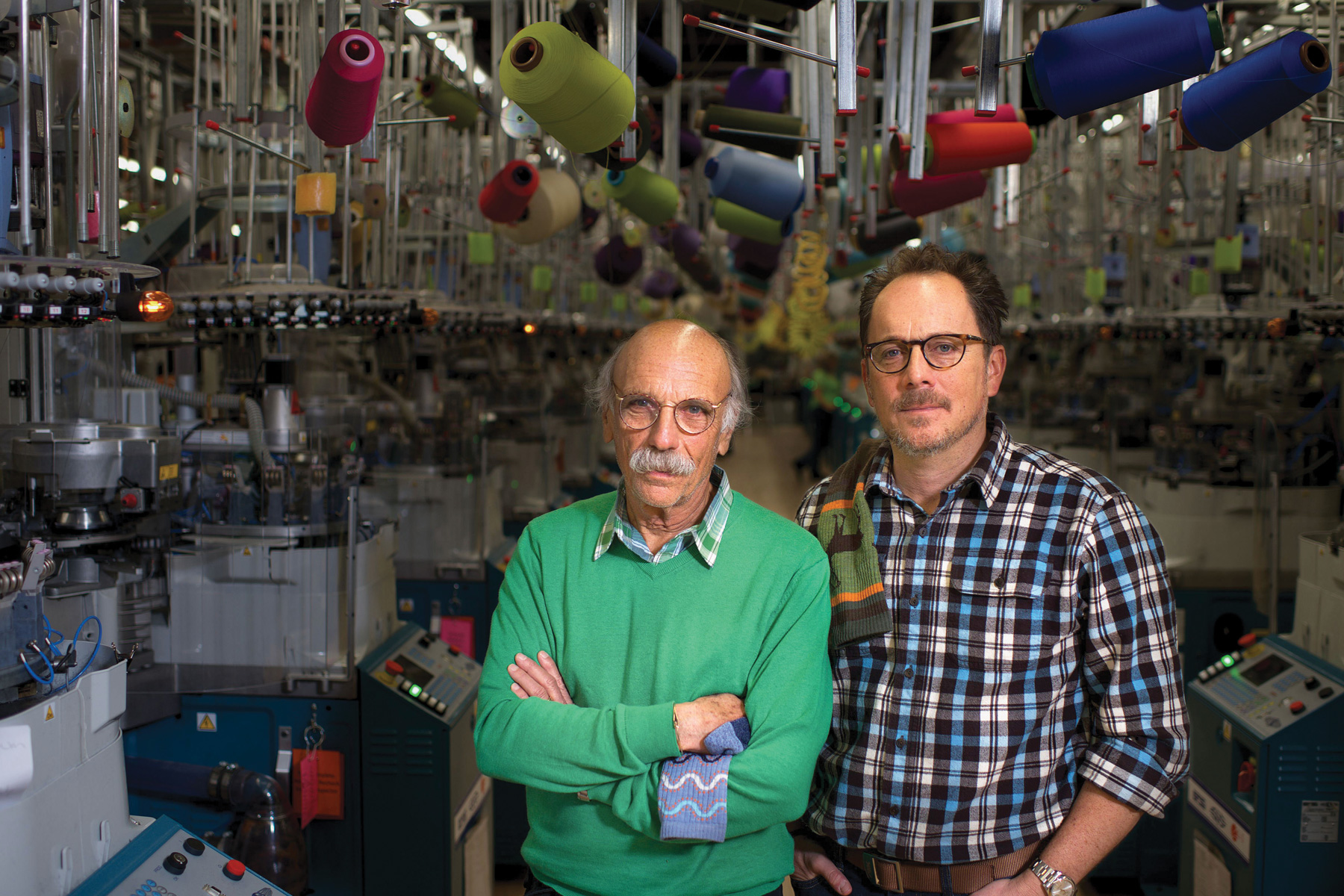
News of factory openings and facility expansion, along with reports of ambitious growth plans and commercialization of leading edge, home grown product is gradually becoming the norm in the United States. With entrepreneurial spirit, textile businesses are revitalizing regions with investment, employment, and strategic direction.
For example, new ventures in North Carolina put a progressive spin on textile heritage.
Dan St. Louis described the growth he’s seen first hand as executive director of the Manufacturing Solutions Center (MSC) in a December interview with The Weekly RoundUp, a podcast dedicated to all things business in North Carolina. “There’s been extraordinary growth in start-ups since 2010, and when you look at the data 70 percent of these people are under 40 years old,” said St. Louis, adding, “this is opening lots of doors for small manufacturers, which we have clusters of here, that are willing to do small runs that are higher profit.”
Located on the campus of Catawba Community Collage, in Conover, NC, the MSC focuses on helping commercialize product, with prototyping, applied R&D, testing and equipment onsite. St. Louis says he has seen “a lot of crazy ideas” from aerospace to sporting goods come through MSC doors that proved viable. CBD infused compression sleeves are one example.
“There’s been extraordinary growth in start-ups since 2010, and when you look at the data 70 percent of these people are under 40 years old.”
— Dan St. Louis, Executive Director, Manufacturing Solutions Center
For the past three years, North Carolina-based Founder’s Hemp and biomaterials company Nufabrx have been testing and developing a compression sleeve garment, called Hemp Squeeze, using Founder’s Hemp CBD Oil. The hemp extract is infused into the fibers of the Nufabrx yarn, a patented technology that delivers 3-dimensional, 360 degrees of active relief to the elbow and knee. “We’re taking a brand new industry — hemp, and taking an old industry — textile and we’re using new technology to help rejuvenate textiles in North Carolina,” said Bob Crumley, founder and CEO of Founder’s Hemp. “I never dreamed, when we first started this three years ago, that our Hemp Squeeze product would be made in Asheboro.”
Jordan Schindler, founder of Nufabrx moved his headquarters in 2016 from Seattle to the Manufacturing Solutions Center (MSC). “To move my vision forward, I needed a home base that understood the textile industry,” said Schindler. “Health Wear is the next generation of clothing, with CBD and other actives built directly into the garment itself.”
Advancing Performance
AKAS Tex, a PA-based textile manufacturing and design firm, has introduced a one-way wicking fabric designed to keep athletes cool, dry, and fresh, even in the most humid conditions. ProCool Stretch-FIT Dri-QWick Sports Jersey is a double-facing fabric with hydrophilic fibers next to the skin to wick moisture away, and hydrophobic fibers on the other side to keep moisture from seeping back into the fabric. It also uses Lycra for a four-way stretch and recovery.
“We’re taking a brand new industry — hemp, and taking an old industry —textile and we’re using new technology to help rejuvenate textiles in North Carolina.”
— Bob Crumley, Founder, Founder’s Hemp
“The hydrophilic side has a special diamond mesh which increases the surface area for wicking,” explained Sid Sharma, AKAS president. “It’s similar to a crest and valley — the raised diamond gathers the moisture and pulls it into the valley. We also use a special binding yarn between the layers which ties them together, but doesn’t allow the hydrophilic and hydrophobic fibers to mix.” It is manufactured without harmful chemicals or finishes in highly controlled settings.
AKAS sources raw materials in the USA and partners exclusively with American mills for production. In addition to creating fabrics for customers, AKAS has its own line of high-performance textiles including some of the top brands for absorbency (ZORB), food safety (ProCare), and organics (ProEco). ProCool is the latest addition to the firm’s branded offering.
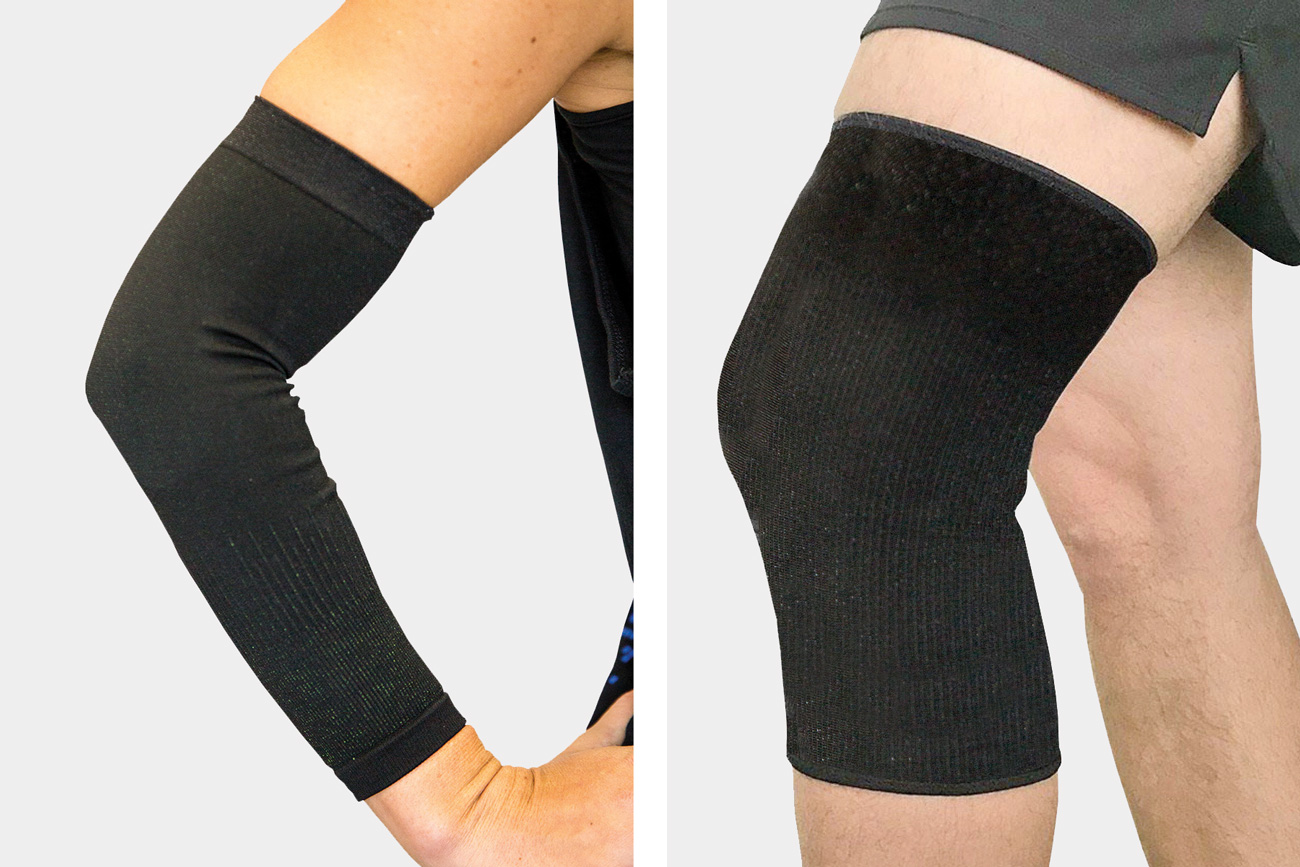
The family-owned enterprise, established in 2007, has grown by double digits every year, according to Sharma and will be expanding its facility space two-fold in 2020. Strategic decision-making, technical proficiency, and lean corporate structure has fueled company success.
In addition to designing and making fabric, the company has weeded out overseas businesses and concentrated on forming solid partnerships with established branded ingredient firms like Dow (Silvadur), DuPont (Teflon), Invista (CoolMax), and Lycra.
AKAS recently announced a licensing agreement with Cotton Incorporated to manufacture and market the TransDry fabrics.
“We work with the best American knitters and laminators and have good partners,” said AKAS CEO Arch Sharma.
Factory Investment
Sock maker Darn Tough Vermont, based in Northfield, VT, is adding a new 50,000-square-foot manufacturing facility to its production next year, and expects to have 100 people working at the new Waterbury, VT site in 2021. The leased space is part of an ambitious five-year growth plan for Cabot Hosiery Mill, Darn Tough’s parent company. In an interview with the local press, CEO Ric Cabot said the company expects to sell 8 million pairs of socks in 2020.
Renovations will start in February to create an additional 17,000 square feet of office space in the facility with manufacturing starting in Waterbury later in 2020. The company’s headquarters and existing sock factory will stay in Northfield. Darn Tough recently spent $2.5 million updating the 100-year-old Nantanna Building to increase the company’s space for manufacturing and internet fulfillment in Northfield.
“We’re doing this to fund our growth, but it’s also for the long term,” Cabot was quoted as saying. “It’s for the prosperity and job security of the people who have been with us all these years.”
“We work with the best American knitters and laminators and have good partners.”
— Arch Sharma, CEO, AKAS Tex
Georgia is also experiencing progress on the production front. Following two decades of decline, the opening of American Knits returns apparel manufacturing to the town of Swainsboro. The new business bolsters the domestic supply chain with regionally-located textile suppliers Buhler Quality Yarns, Jefferson, Ga., Gastonia, N.C.-based Parkdale, and Carolina Cotton Works (CCW), Gaffney, S.C. Premium knit tops using 100 percent U.S. grown ring-spun cotton will be produced, including T-shirts for a supplier to the U.S. military.
American Knits execs make the point that their company represents a new story in terms of domestically produced textiles. “The old story was 20-plus years ago, when many of the plants in the U.S. closed. Over the last eight years, I’ve discovered that there is a demand for U.S.-manufactured goods. And younger folks kind of care about where it’s made, the type of fabric that’s used and the sustainability part of it. We felt like if we could find the right place, then the demand was there,” said managing director Steve Hawkins, at a recent media event. Managing partner Dr. David Talton elaborated, “We want everybody to know that we’re more than just another plant — we’re making a new story here around how we treat people and how we treat our customers, and our employees will reflect to our customers how we treat them.”