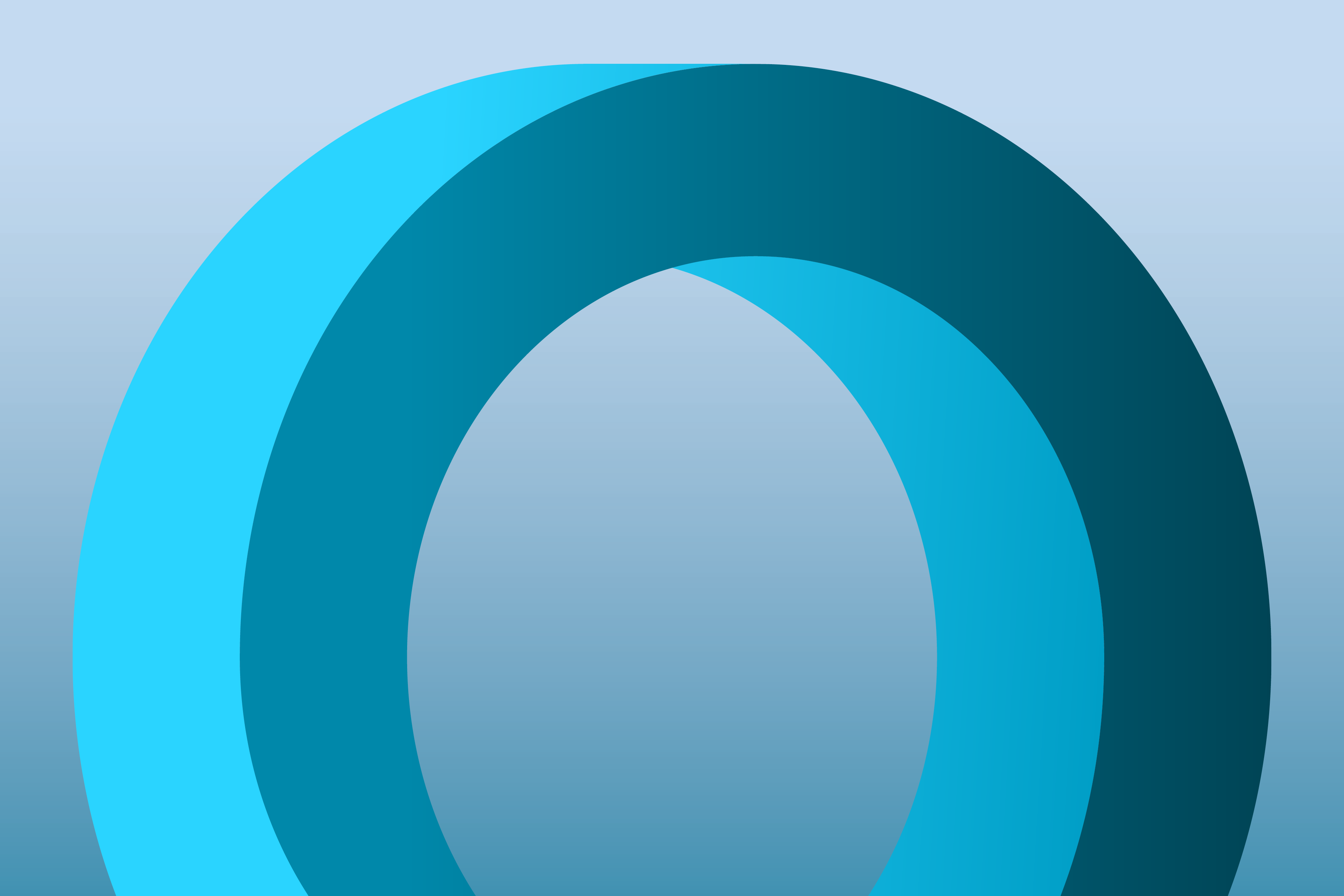
Chasing Circularity
The Race to Achieve & Advance Closed Loop Systems.
Chasing Circularity
The Race to Achieve & Advance Closed Loop Systems.
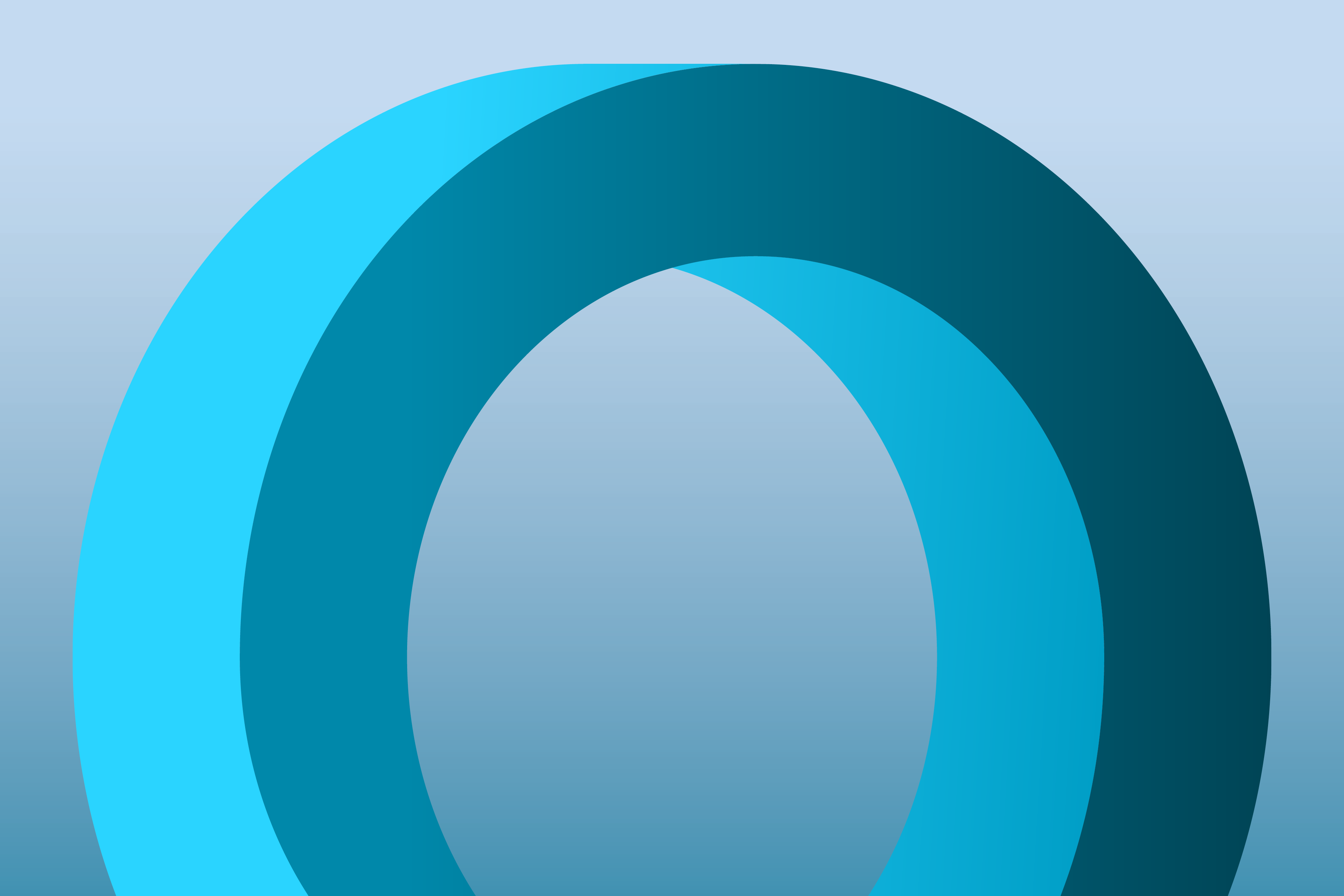
In this season’s swirl of sustainability developments, companies are taking impactful action to accelerate change. A collective push to reduce, recycle and repurpose using innovative textiles and technologies complements a determined outlook among company execs that going forward together is the path to decarbonization. It's clear that when it comes to creating a new model built on circular production and consumption, the textile industry means business.
“If you want to drive transformative change, then you have to shift the goal of the system," stated Sally Uren, chief executive of Forum for the Future, who spoke recently in conversation with Dr. Andrew Dent, executive director of the Material Connexion. Uren highlighted her belief that a regenerative ecosystem is possible, but stressed that it requires “systems thinking.”
According to Uren, if the textile business is serious about delivering advancements of environmental standards, for example, a re-focusing of the current system is needed that includes recognition and collaborating with other systems to create holistic change. “It’s important to remember that everything is connected — energy, agriculture, health, etc. — which makes designing for change more complex,” said Uren, noting that things are easier when there is clarity of goals. “As it is now, textile companies can do things, but you’ll hit a limit to scale unless other systems are in sync.”
Uren advocates that companies get “hyper-collaborative” and harmonize an approach to standards. By doing this the industry will continue its progress from the “starter phase” of collecting scientific data, to its current “accelerator phase," and transition to a “stabilization phase” of legislation and societal acceptance to bring new tech to scale and have price parity with established technology.
If all this sounds daunting, Uren offers this advice, “If you can’t change the system, you can dance with the system.”
Innovation & Initiatives
A recent study revealed that each of us might be consuming a credit card’s worth of small plastic particles every week! While plastic and other waste is the main culprit in this alarming statistic, microfiber fragmentation certainly contributes to the problem — a problem the textile community is committed to tackling.
Polartec Shed Less Fleece is a good example. Shed Less is a process that combines yarn construction, knitting, chemistry, and manufacturing to reduce home laundry fiber fragment shedding significantly. The first fabric to receive this new technology is the iconic Polartec 200 Series Fleece; the Polartec Series 200 with Shed Less is 100 percent recycled polyester.
The Shed Less process works by engineering the lofted fibers that give fleece its soft hand the ability to resist breaking and rubbing off during home laundering. Polartec used the AATCC (American Association of Textile Chemists and Colorists) TM212-2021 test method for fiber fragment release during home laundering. The test was conducted with large sample sizes to account for variability. The testing concluded that Shed Less Fleece reduced fiber fragment shedding by an average of 85 percent compared to the baseline fabric.
“In 2016 we began looking into how we might test for fiber loss because there wasn’t a lot of research on the issue,” said Aimee LaValley, Polartec textile development, dye and chemistry manager. “This led to new products like Polartec Power Air, new manufacturing processes, as well as our participation in the TextileMission workgroup to study the issue on an interdisciplinary basis.”
Polartec’s Karen Beattie, explained, “Polartec Shed Less technology and Polartec Power Air share the same EcoEngineering motivation at Polartec — to provide textiles that help to reduce microfiber shedding in home laundering. Power Air is an entirely new fabric construction that encapsulates insulating fibers to protect them from breaking off and shedding, while Shed Less technology offers an upgrade to our most popular product, which is Polartec 200 Series fleece.”
Cordura Advanced Fabrics is pushing ahead with circularity by innovating and expanding its solution dyed offering and launching fiber technologies. Both the company’s TrueLock fabric platform and the new re/cor RN66 recycled nylon are finding success.
Cordura, in partnership with HLC Industries, recently debuted a new nylon 6,6 Navy Blue Solution Dyed (SDN) TrueLock Fabric that targets the military, tactical and law enforcement market providing high-quality lot-to-lot color consistency plus long-lasting color durability. “The new Navy Blue TrueLock Fabric is a next-gen solution dyed nylon 6.6 fiber technology that is loaded with performance properties and sustainability attributes,” stated Cordura’s Cindy McNaull, explaining that compared to conventional level acid piece dyeing to SDN, the Cordura process uses less H2O, energy and fewer greenhouse gasses. The Navy is an important addition to the range, which now numbers nine different colors. Said McNaull, “The European market has a growing interest in solution dye for workwear. We are expanding in a stretch version, reinforcements and a new colorway. It’s not just about saving water.”
Following the re/cor launch in 2022, Cordura is now broadening its range, by offering more variety within the portfolio — from 210 to 420 denier, air-jet texture and ballistic weave in different plys – to enhance customer differentiation.
“It’s not a one-size-fits-all situation with customers,” noted McNaull. “Some are just getting started with solution dye goals while otters are far along in recycling.” Early adopters have had rapid success. Black Ember expanded their small line with new retail doors in Japan, and Mystery Ranch advanced its sustainability goals using re/cor in a 2022 collection.
Sustainability meets multifunctionality in Schoeller’s new recycled textile collection RE-SOURCE. “By giving new life to previously used materials, we create ecological and social added value,” stated Antonio Gatti Balsarri, chief commercial officer. The RE-SOURCE range is designed and developed for urban environments, as workwear, or on the mountain, with fabrications equipped with schoeller-ecorepelBIO and schoeller-c_change membrane technologies to provide breathability, thermal regulation, and wind and water repellence in concert with comfort features. All textile innovations in the collection are made from bio-based, post and pre-consumer materials such as recycled polyester and spandex, and bluesign approved.
Two textile innovations in the collection have been lined with natural Nativa merino wool on the interior, which offers maximum wearing comfort and is produced under the highest eco standards. The entire production process of Nativa merino wool is 100 percent transparent and traceable for consumers using blockchain technology.
“For RE-SOURCE, we used the special Q-cycle process,” explained Schoeller Technologies AG, COO, Hans Kohn. “The resilient and durable Q-cycle polyamide is obtained by pyrolysis of used tires, thereby saving CO2 emissions compared to the combustion process.”
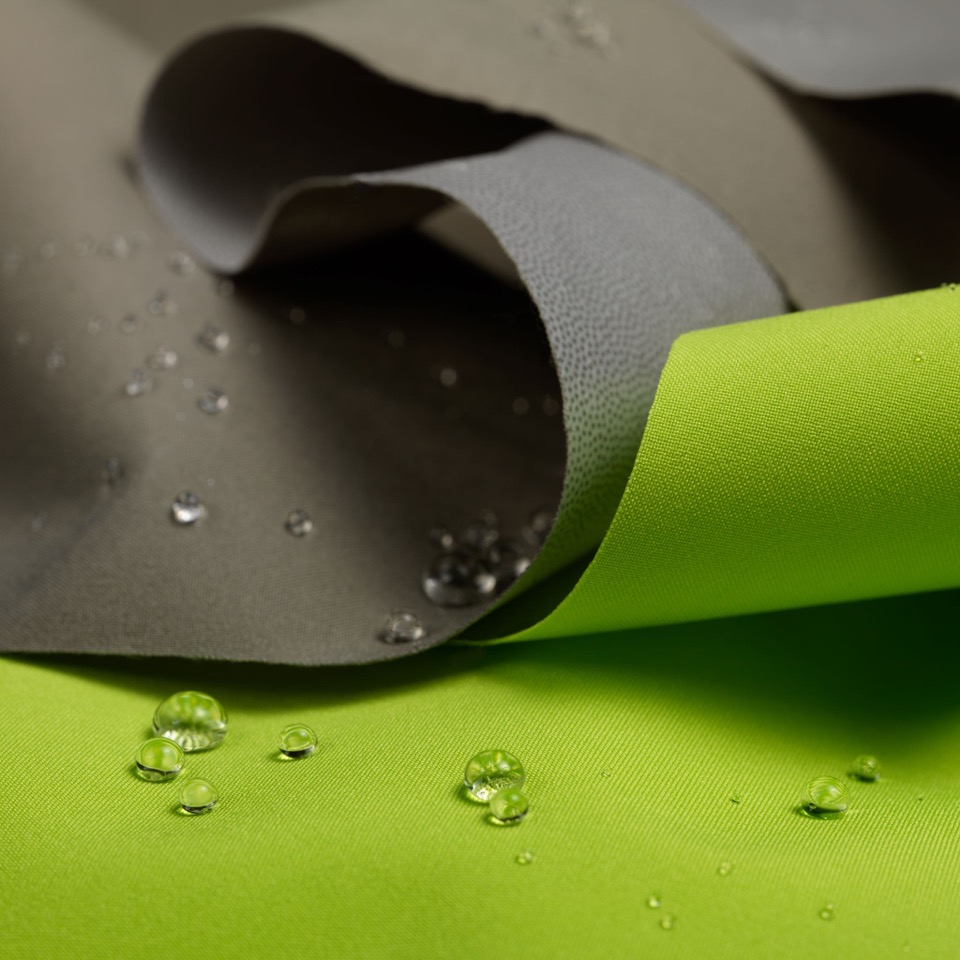
Goal Setting & Hitting Targets
Milliken reached a milestone in its path to net zero recently with its science-based net-zero targets having been approved by the U.N.-backed Science Based Targets initiative (SBTi).* Halsey Cook, president and CEO of Milliken & Company, stated, “Climate change is placing pressure on communities, on companies and on our planet. The time to take meaningful action is now.”
SBTi calculates that companies committed to cutting emissions in line with climate science now represent $38T – one third – of the global economy. Milliken is one of the first 50 companies globally to achieve approved science-based net-zero targets and joins a group of more than 1,300 companies who have made net-zero commitments using the 2021 SBTi Corporate Net-Zero Standard. Milliken is the first company to be approved in its home state of South Carolina.
“Not all net-zero is the same, which is why Milliken commits to reaching real net-zero greenhouse gas emissions across the value chain by 2050 from a 2018 base year,” said Kasel Knight, general counsel and head of sustainability at Milliken. Cook adds, “Our targets empower our team of more than 8,000 to reduce risk, minimize impacts, work efficiently, control costs and identify new ways to deliver products.”
Chemours’ circularity strategy also believes strongly in a collective pursuit of sustainability with focus on the UN's Sustainable Development Goals (SDG). The Executive Summary published in Chemours’ latest CSR, highlights this theme. For example, the firm’s 2030 goals align most closely with three SDGS that prioritize clean water and sanitation; responsible consumption and production; and climate action.
Sean Uhl, sustainability technology director, stated, “In 2021 we established our goal of reducing Scope 1 and Scope 2 absolute GHG emissions by 60 percent by 2030, positioning us to reach net zero operations by 2050. Building on this commitment we are pursuing an official science-based target through the SBTi to reduce our Scope 3 emissions, strengthening our already ambitious climate goals.”
Steven De Backer, EMEA technical marketing manager, remarked, “In 2021, Chemours joined a three-year recycling research project, Remove2Reclaim, in collaboration with industry, academia and government experts to develop a more sustainable process for recovery TiO2 and polymers from plastic end-use products.”
Ambitious Collaboration
Earlier this year at Lineapelle, the international leather fair held in Milan, Lenzing and National Fiber Welding, Inc., (NWF) showcased a new sustainable alternative for leather applications that features Tencel fibers as another backer option for NFW’s plant-based technology, Mirum.
Mirum is a categorically unique material class, according to NWF. Free from plastic, Mirum is made from natural rubber, plant and mineral pigments, plant-based oils and waxes, and an all-natural fabric backing. Instead of relying on PU binders, a characteristic of most leather alternatives, Mirum uses natural rubber and plant oils for binding.
A variety of natural ingredients like biobased charcoal, clay, cork powder, rice hulls, coconut fibers, recycled denim or seaweed are used to develop color or add visual interest. Products made with Mirum can be recycled into new Mirum or ground up and returned to the earth, when no longer in use, while Tencel fibers are compostable and biodegradable, enabling complete circularity of finished products.
“At NFW, we believe that plant matter is the only material that can scale to replace plastic. By adding fabrics made of Tencel to MIRUM, we can enhance material transparency and traceability, while guaranteeing comfort and great hand feel on the skin,” said Oihana Elizalde, VP and general manager of Mirum at NFW. Allbirds’ Fall ’22 Plant Pacer, features Mirum in the upper and lined with Tencel.
At material science company Pangaia, collaboration and innovation go hand in hand. The Renu jacket, Pangaia’s first denim product made entirely from cotton textile waste, was created in collaboration with Evrnu’s NuCycl. Dr. Amanda Parkes, chief innovation officer at Pangaia, believes the partnership demonstrates the “extraordinary potential for superior quality from recycling technologies.”
With NuCycl, pre-and post-consumer textile waste is broken down and transformed into a high-performance fiber for premium textile products. The technology uses repolymerization to convert the original fiber molecules into new renewable fibers. Products made with NuCycl can be disassembled to the molecular level and regenerated multiple times into new clothing . The fiber doesn’t need to be blended with virgin fiber, thus significantly less resource-intensive while also easing recyclability.
Evrnu co-founded/ CEO Stacy Flynn shares what many in the textile world believe to be an industry priority in 2023: “Our mission is to help brands create clothing out of recycled materials that are not only of the highest quality but can also continue to be recycled.”
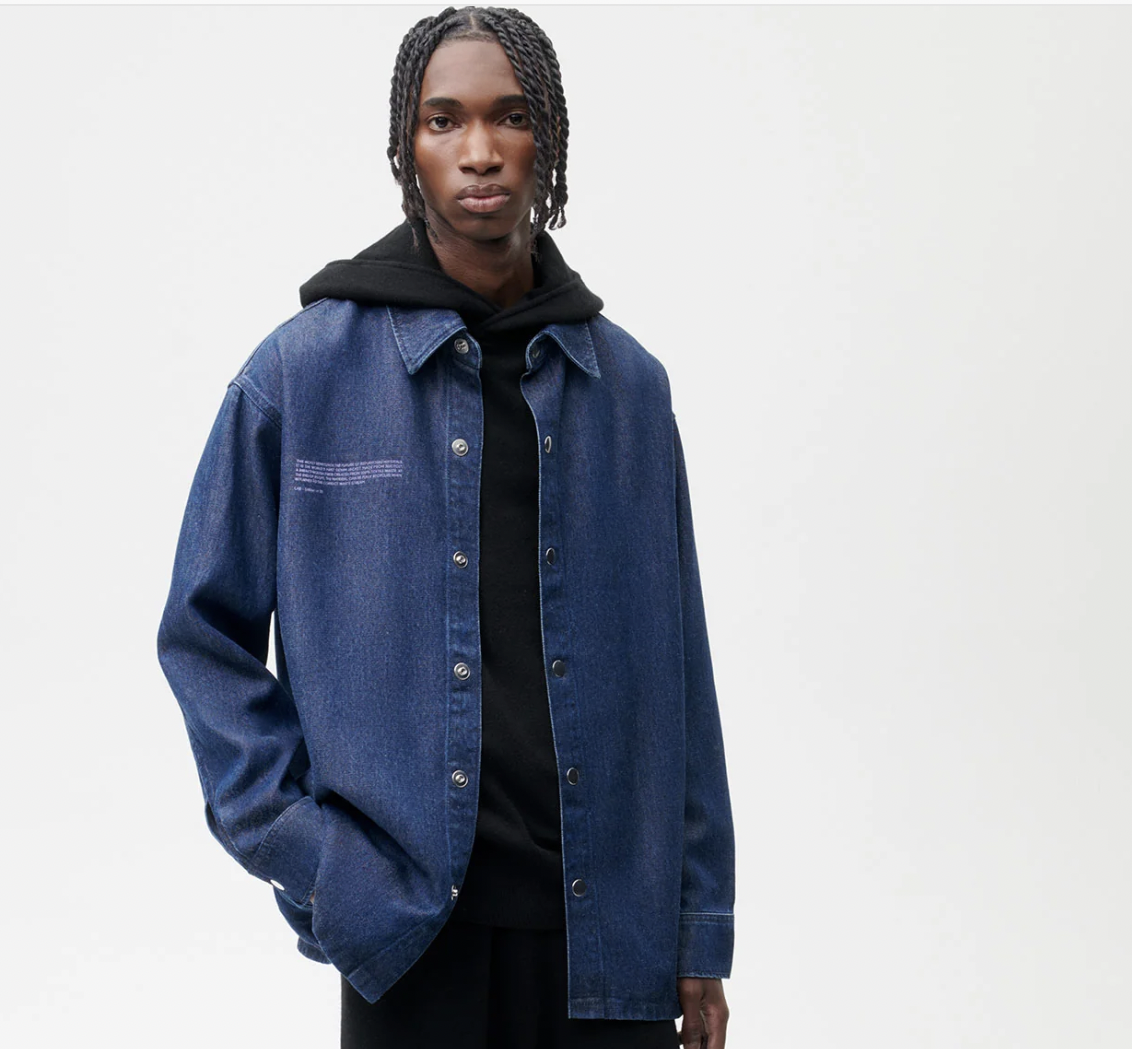
5 Top Trends
The Future of Materials
Nia Silva, director, Materials @ Fashion Snoops shares leading innovations and industry shifts that will influence the product development of materials and surfaces for the next 3-5 years.
1. Ethical Foundations: The basis for everything, and vital for sustainable design. “To pave an ethical way forward, suppliers sow seeds to a responsible future.”
Emerging: Fostering regenerative farming; example denim powerhouse Citizens of Humanity partners with Kiss the Ground non-profit to support and fund U.S. cotton farmers.
2. Low Impact: Prioritizing cyclical products and sustainable material engineering. Government plays a role in carbon reduction — whether plastic, steel, cement, or textiles.
Emerging: Consumers will expect traceable tech and transparency, but will they pay for it?
Emerging: Carbon becomes a leading renewable resource and “captured carbon” will scale.
3. Bactory: Bio-designed will saturate the market as the biodesign system becomes robust and “lab-grown” provides a promising future. In 2020 start-ups in biotech raised $8B U.S. Alt leather, silk and synthetics.
Emerging: algae & seaweed i.e. sea-sourced materials offer performance and aesthetic benefits.
Emerging: bio-derived leather acceleration into new markets. Mushroom (mycelium-based) MycoWorks partners with Ligne Roset using its Reishi product in furnishings.
4. Consciously Renewed: Waste material becoming raw material of the future. Trash is now a “waste resource.”
Emerging: Repair of damaged goods with deadstock and offcut fabrics.
Emerging: Companies, such as Renewcell, create sophisticated and purposeful product from textile waste.
5. Streamlined Processes: The next frontier in manufacturing is streamlining processes to increase speed, efficiency and revenue while reducing waste. New modes of making include more mechanized processing, 3D printing, 4D weaving. Collapsing the supply chain will shift from multi-step make to “all-in-one” process.
Emerging: Karl Mayer & Shima Seiki effectively “de-couple” and streamline areas of the supply chain.
6. Expanded Wellbeing: Sensory-friendly materials will be the cornerstone of comfort and adaptive design.
Emerging: Natural empowered performance fabrications using hyper-cooling using jade; hyper-anti odor using chitin (crab shells); soft Supima cotton; creora regen (recycled) spandex. Peppermint oil, Seacell; fruit leathers and veggie wax finishes with lower impacts are all trending.