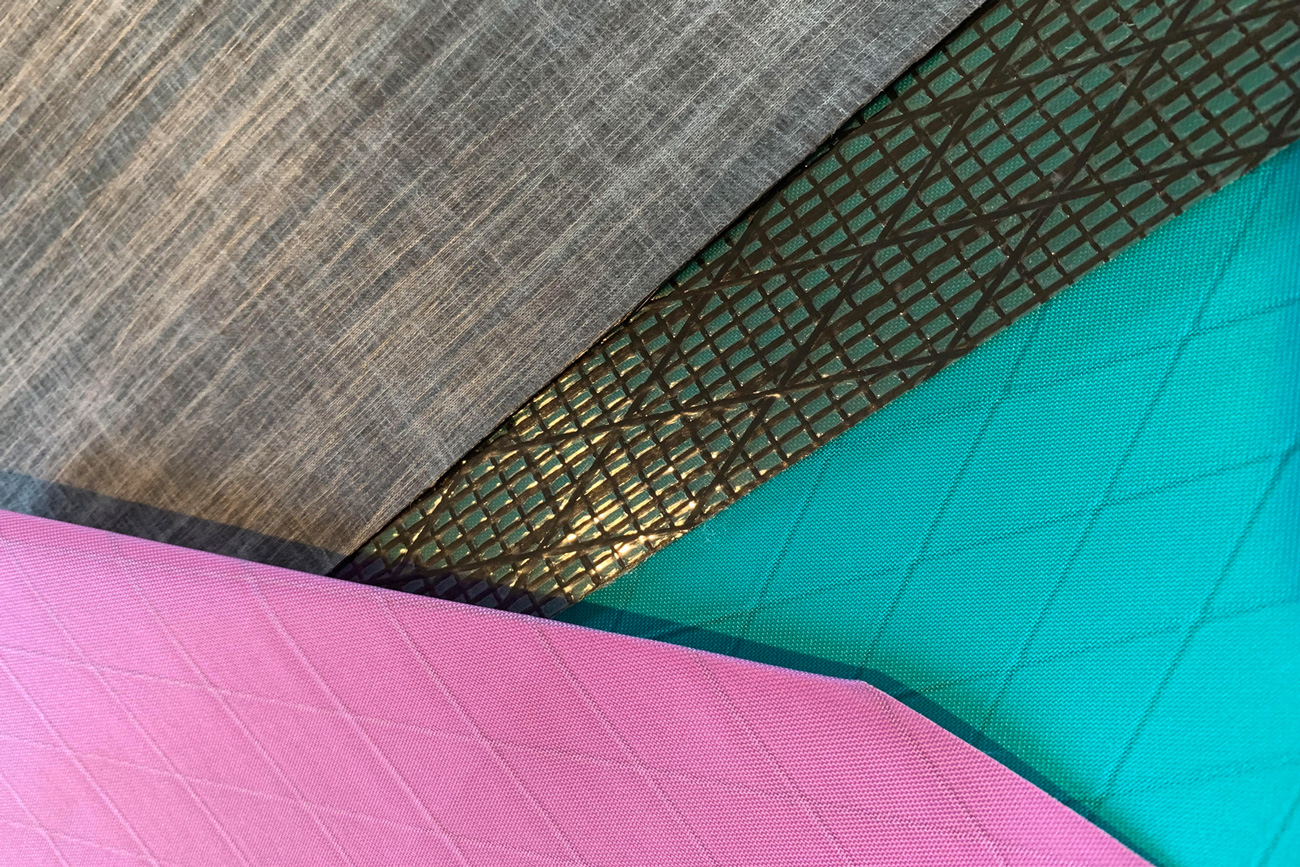
By Land or By Sea
From Sailcloth Tech Comes Fabric Purpose-Built for Venturing Out.
By Land or By Sea
From Sailcloth Tech Comes Fabric Purpose-Built for Venturing Out.
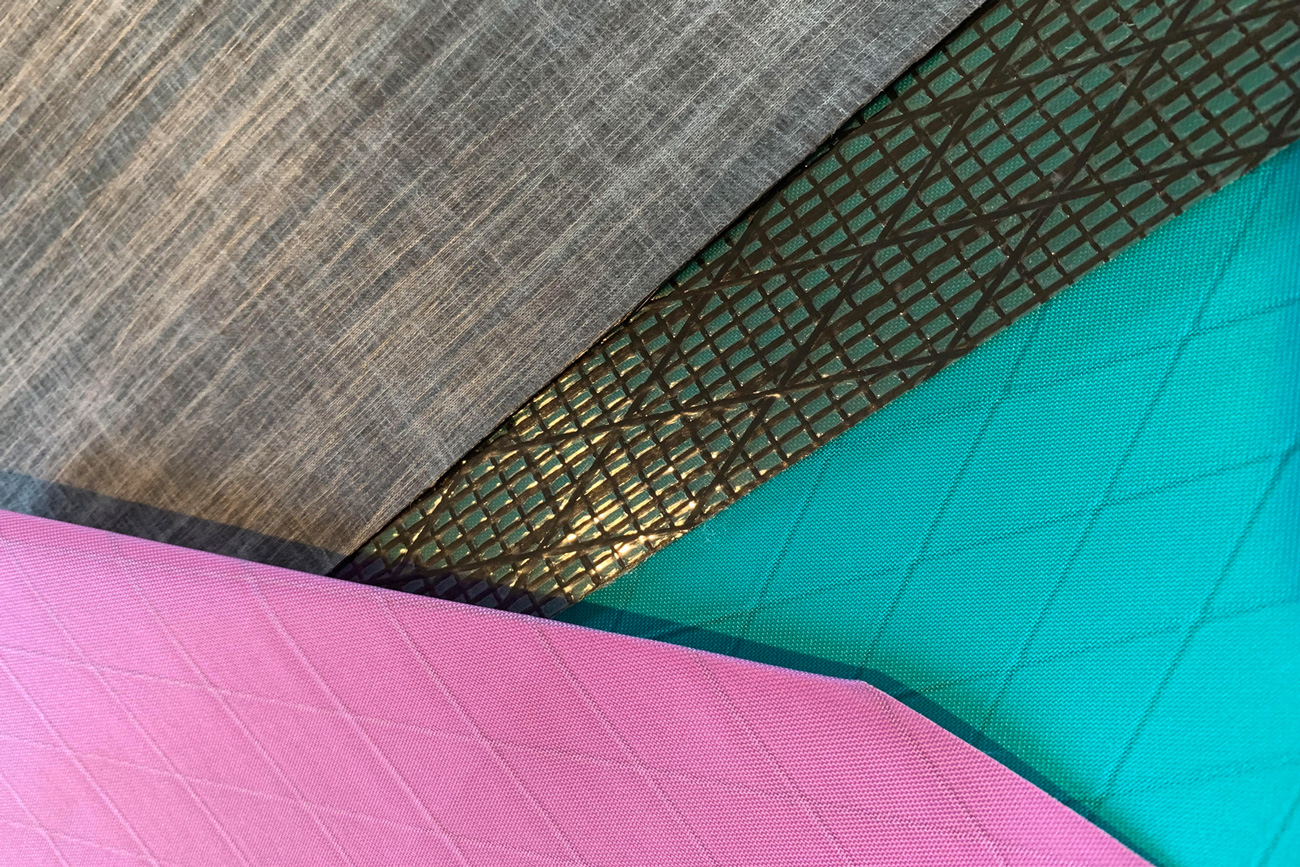
The founders of Dimension-Polyant may have salt in their veins from a heritage of sailcloth making, but these days execs at the Connecticut-based firm have their sights set on outdoor adventures of a different kind. The company’s technical fabrics, milled onsite, have been taking on momentum in recent years and are now a focus of its own.
The name Dimension-Polyant comes from the merger in 1991 of two companies; Polyant, an established German company known for its craftsmanship and expertise in sailcloth production and a then American start-up, Dimension Sailcloth, with a reputation for innovation.
The “cloth” is more like a sheet than traditional fabric. Super thin, yet dense, X-Pac material is lightweight and exceptionally durable. A proprietary weaving, laminating and finishing process results in a highly engineered woven with exceptional performance properties.
X-Pac is known for its dimensional stability, a trait not associated with conventional outdoor textiles, but regarded in sail making. Think of the “rigid wings” on boats used at the highest level of the sailing world, as example. “They have shape built into them to be highly efficient providing structure without weight,” explains Kenneth Madsen, president of the Putnam, CT business, adding, “Dimensional stability is the holy grail.”
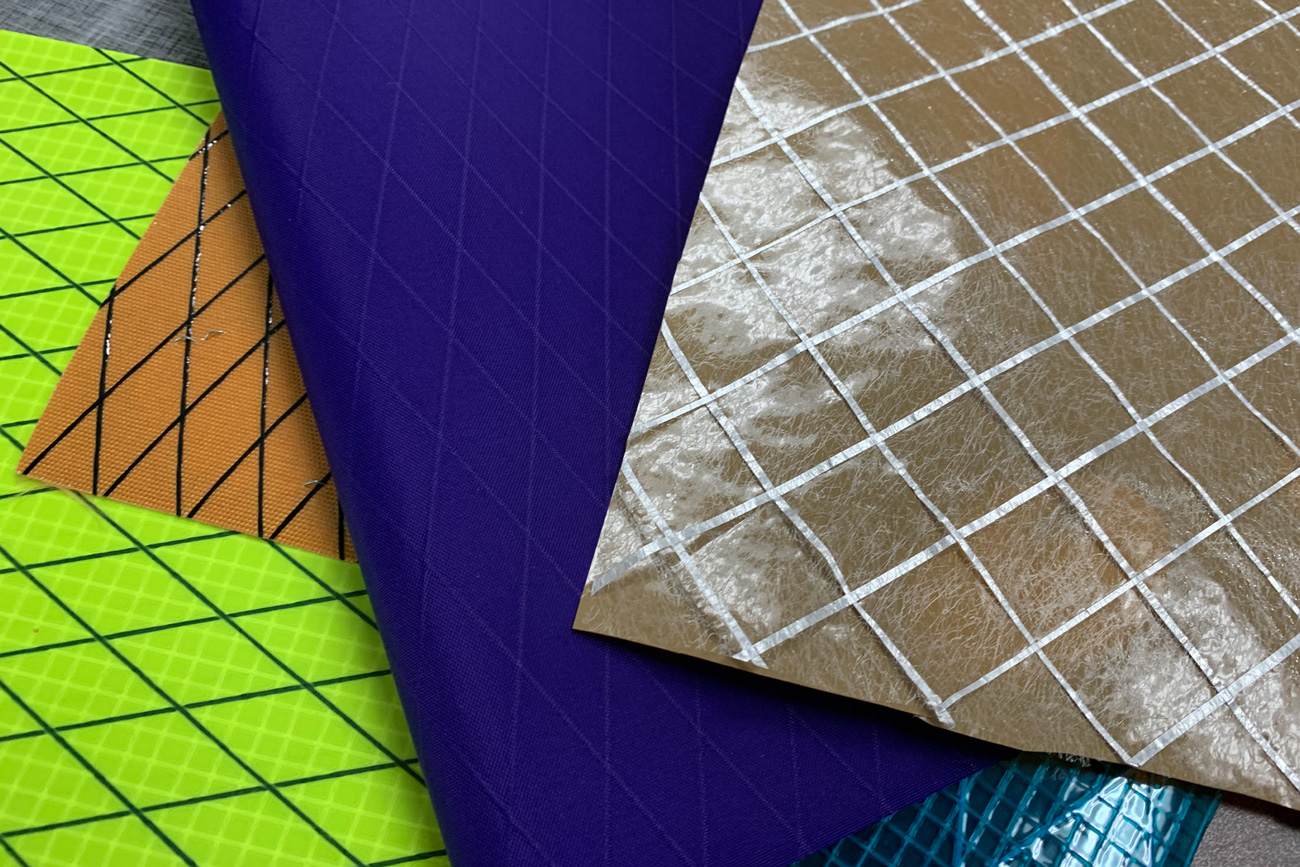
And not easily achieved. The multi-step process, the “special sauce” if you will, is what sets Dimension-Polyant’s X-Pac apart. A pack made out of sailcloth would be loud, stiff, lacking aesthetic and hard to sew. X-Pac handles like conventional pack material but has the DNA of sailcloth.
“We are not sacrificing the technical, nor changing the functionality found in our sailcloth, but finding application in a diverse range of markets,” states Madsen.
Mountain Hardwear and Topo Designs are brand partners in the outdoor pack space. On its website Topo offers this description: “The combination of X-Pac Ripstop Polyester, waterproof construction technology, and 210 denier nylon fabric face provides an ideal balance of weight and durability. Making for a great all around mountain companion, whether you are hiking, biking, climbing or skiing. The X-Ply (diamond pattern) provides additional strength across the bias, traditionally the weakest part of the pack.”
Dimension-Polyant did a capsule bag collection with Supreme that sold out. “I wouldn’t bring the Supreme duffel to top of Everest, but the material could do it,” comments Madsen. Rickshaw is another DP partner that takes X-Pac in a lifestyle direction. The San Francisco specialty bag maker, with a strong following in Japan, features Dimension- Polyant’s LiteSkin product in a travel pack. The sleek, modern pack stands out for its distinct urban aesthetic and its technical tear resist and waterproof qualities.
On the footwear front, DP collaborated with Flowfold to feature X-Pac in L.L.Bean’s iconic Bean boot.
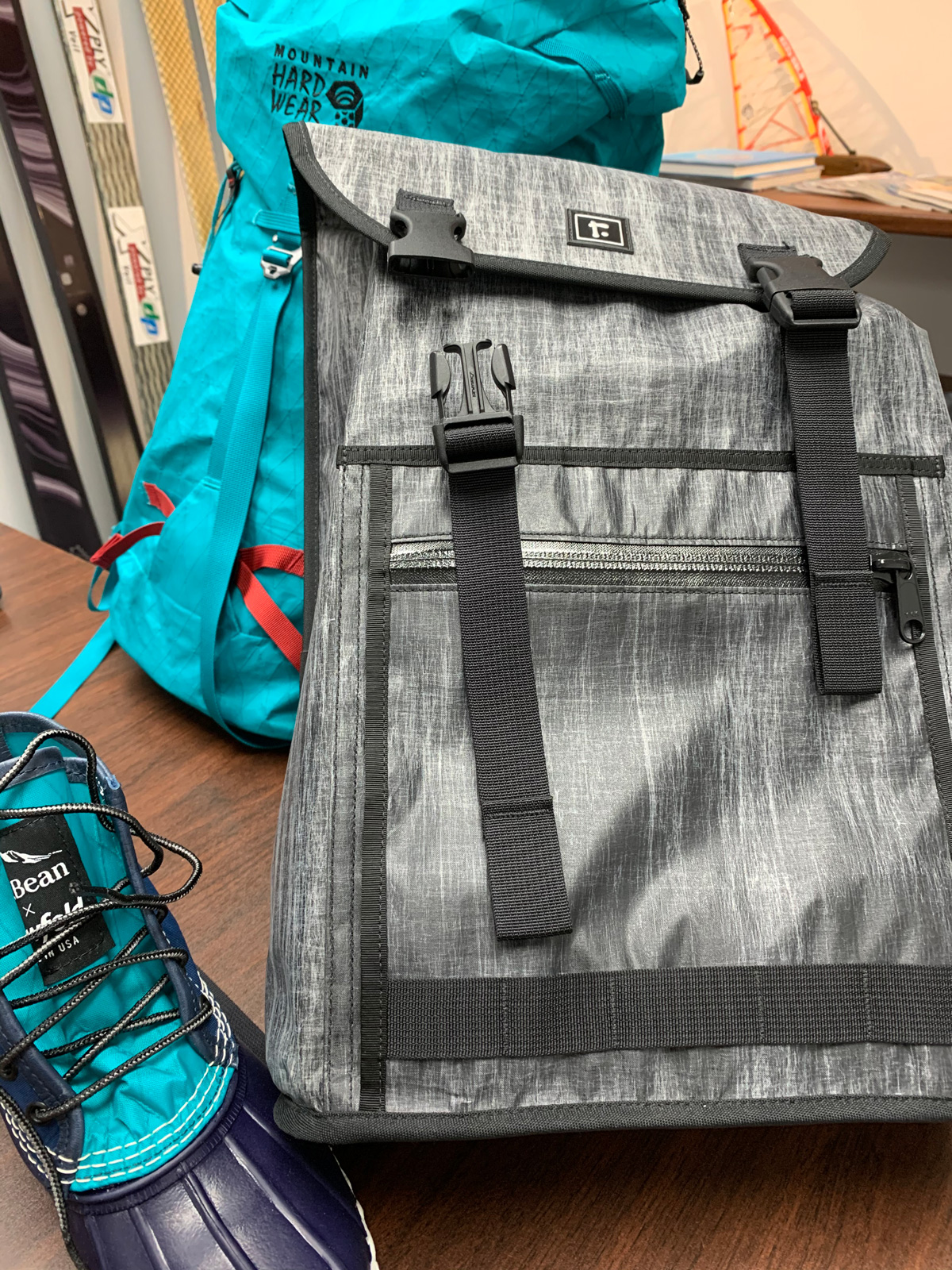
A recent development in the X-Pac family is X-Ply Veil, an ultra-light composite reinforcement for hardgoods like skis and surfboards. The company is also starting a tactical line with Kevlar reinforced with X-Ply for First Responders and military.
“These are all ways we can adapt the fiber content and configuration to meet the needs of end users,” says Dimension-Polyant’s head of technical fabric, Taylor North, who joined the team two years ago.
A Fully Booked Factory
Sailcloth innovation experienced a heady time in the 1980s and 90s when money poured into the sport pushing for new, better, sails for highest-level competition. “It was a steep innovation curve during those years; lamination allowed sailcloth to leapfrog into the high tech world,” explains North, who grew up on the water and has a career background in the sail industry.
Dimension-Polyant continues to invest in its manufacturing at the Putnam facility. A complete overhaul of one laminator was accomplished recently with a second laminator due for a similar upgrade in early 2020. Woven in Germany, the textile is and laminated and finished in CT.
With a small team of 40 employees and onsite manufacturing working three shifts, development is innovative and quick. “The factory is fully booked; this is our biggest year ever,” states North, who works with colleague Peter von Maffei, sales manager. Previously, Maffei spent nine years with The North Face in addition to experience selling department store lifestyle.
“People call us all the time and say they want sailcloth to make a bag. And we tell them, you probably don’t want sailcloth for a couple reasons, but try this: X-Pac,” explain the execs.