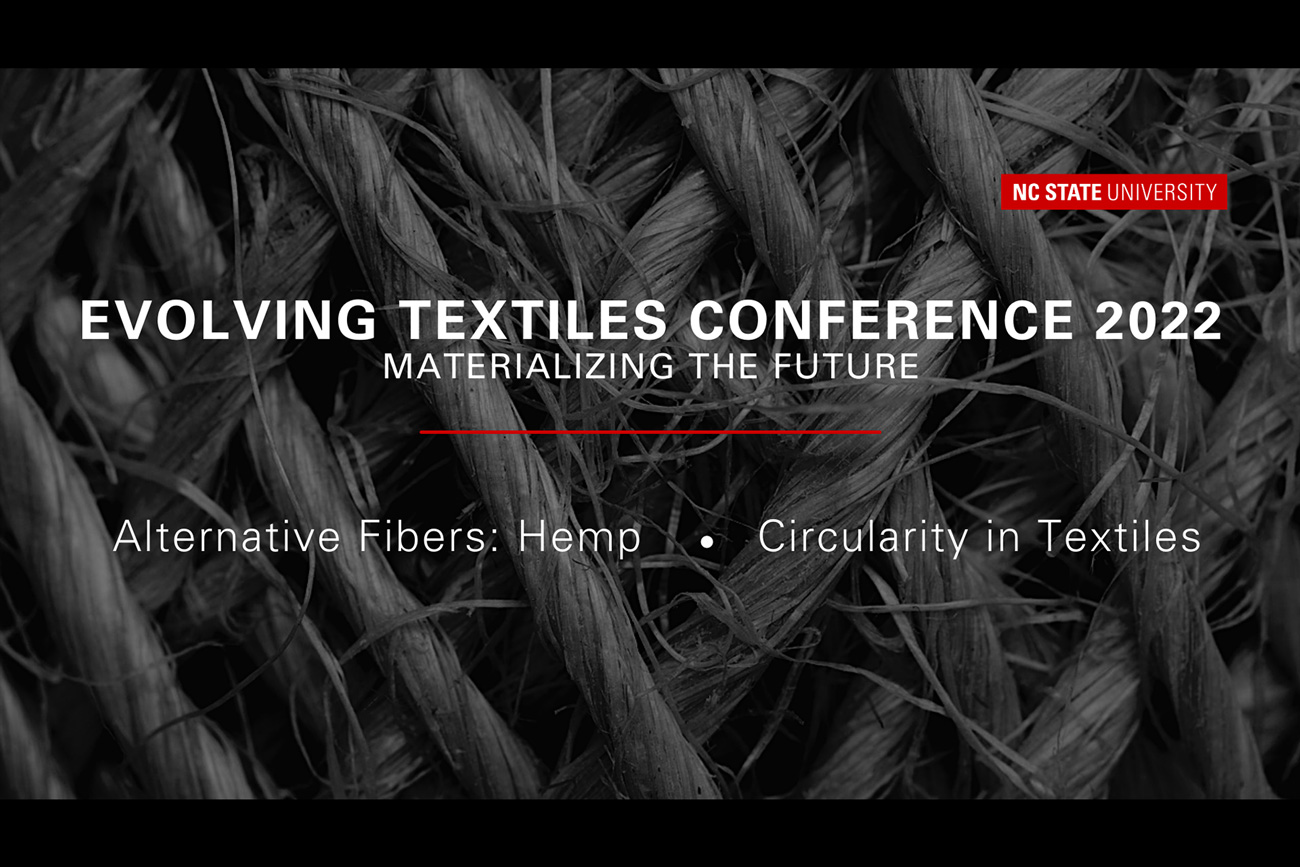
An All-Encompassing Sustainability Event
An All-Encompassing Sustainability Event
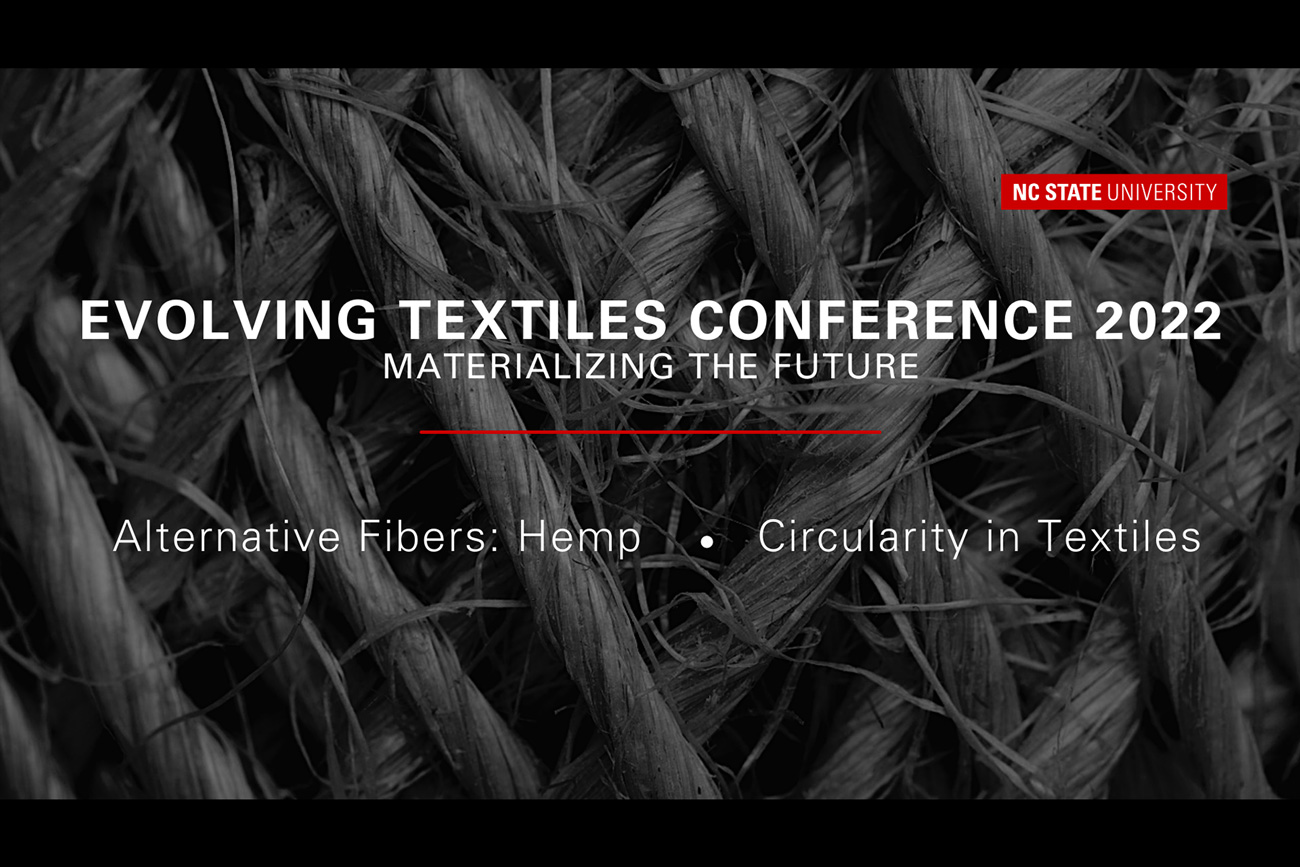
Two of the hottest topics in textiles were center stage last week when experts from industry and academia gathered to discuss circularity and alternative fibers during an event hosted by The Wilson College of Textiles at North Carolina State University (NCSU).
Hemp is experiencing growth (literally) and rapid development in the U.S., but particularly in the Southeast region where fiber use in textiles is the primary focus. Enthusiasm around the fiber’s potential made for lively conversation on Day 1 of the Evolving Textiles Conference. Progress in hemp is happening across NCSU – in the Wilson College of Textiles, the College of Natural Resources, and the College of Agriculture and Life Sciences.
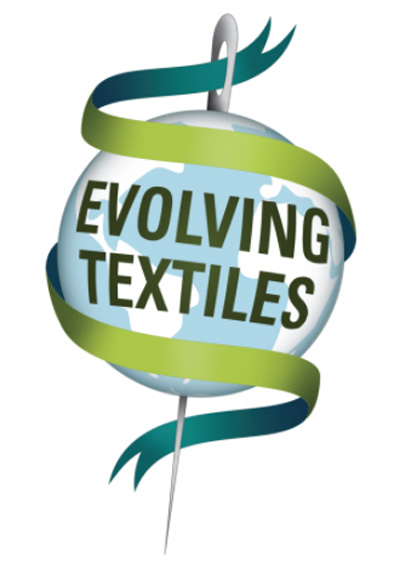
Day 2 of the Conference, presented virtually on March 16 and 17th, broadened its scope to a variety of aspects of circularity within the supply chain. LCAs, end-of- life solutions, resale, mending, recycling, circular design, materials selection, and digital tracking of clothing wear were all part of a jam-packed program schedule featuring more than 30 speakers in addition to Q&A sessions.

Gary Sikes of Bountiful Harvest shared a farmer’s perspective of growing hemp for textiles in North Carolina. He gave a fast, fact-filled update on the strides made, and set-backs experienced, during the past few years. Sikes explained current needs including: processing infrastructure and industry funding; better harvesting equipment; better understanding of seed genetics to grow seed in the Southeast and for the price of hemp to be competitive with commodity crops.
Guy Carpenter, founder of Bear Fiber, and a leader in the domestic hemp movement for decades, noted that spinning hemp remains problematic because of the non-uniformity of the fiber. “We’re not there yet in the U.S. in terms of consistency, but I’m confident we will get there,” said Carpenter, who characterized the past four years as “a hell of a ride” full of opportunities and challenges in short staple spinning of textile grade hemp fiber.
Like hemp, circularity is a market driver these days, yet scalability has proven elusive. Not so with Renewcell, a Swedish firm that has in a short time inked deals with H&M and Levi’s and is already building its second production plant. Renewcell’s Harald Cavalli-Borkman presented the keynote address and impressed attendees with the company’s Circulose product, a dissolving pulp made from 100 percent textile waste, such as worn out jeans and product scraps, that can be used to make staple fiber or filament viscose, lyocell, modal, acetate or other types of man-made cellulosic fiber.
“We add a crucial extra link in the value chain,” stated Borkman. “We need to scale sustainable solutions to make a difference and grow quicker to meet expected demand with processes that work with industrial scale machines.”