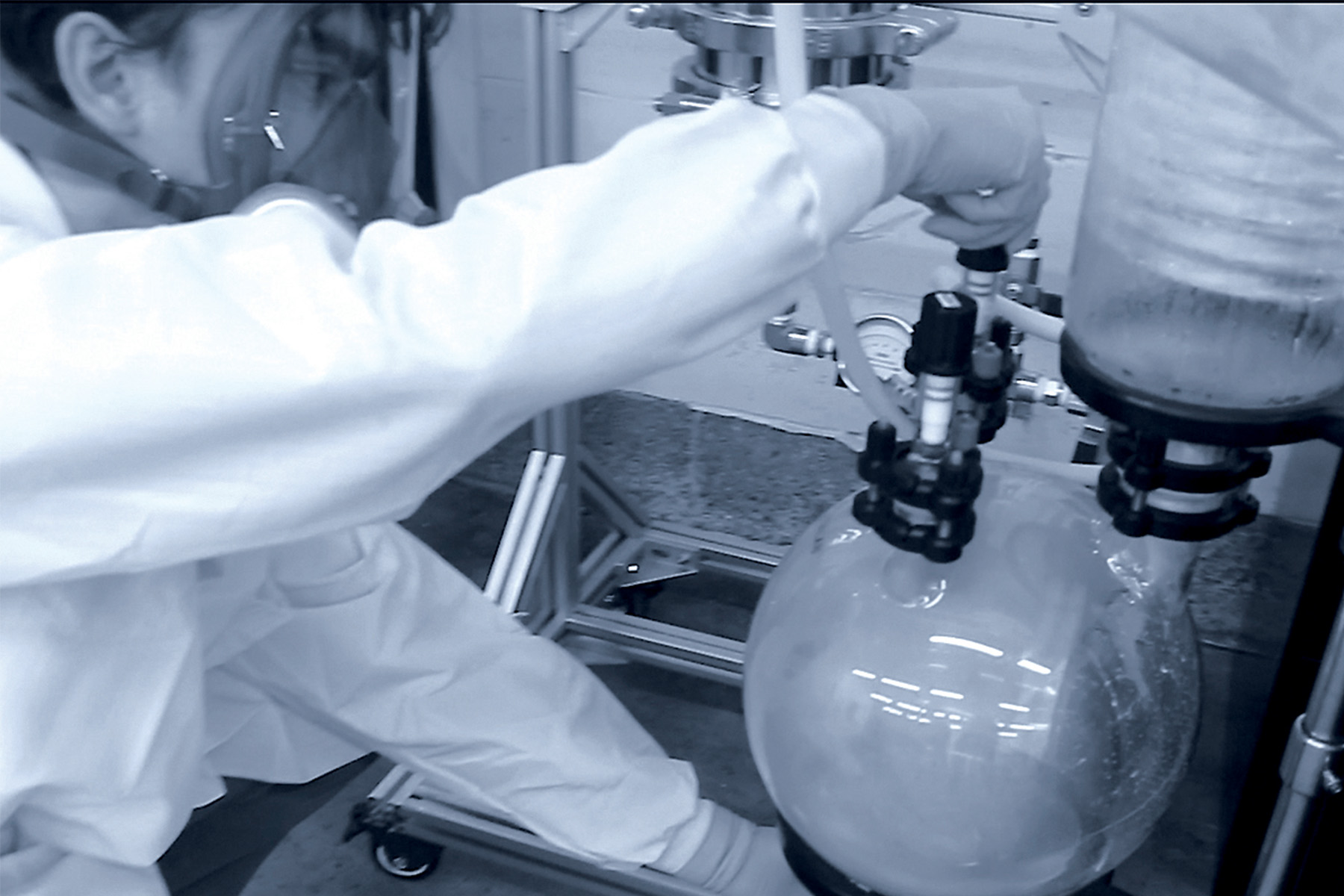
PFAS Problem
Performance Becomes an Issue.
PFAS Problem
Performance Becomes an Issue.
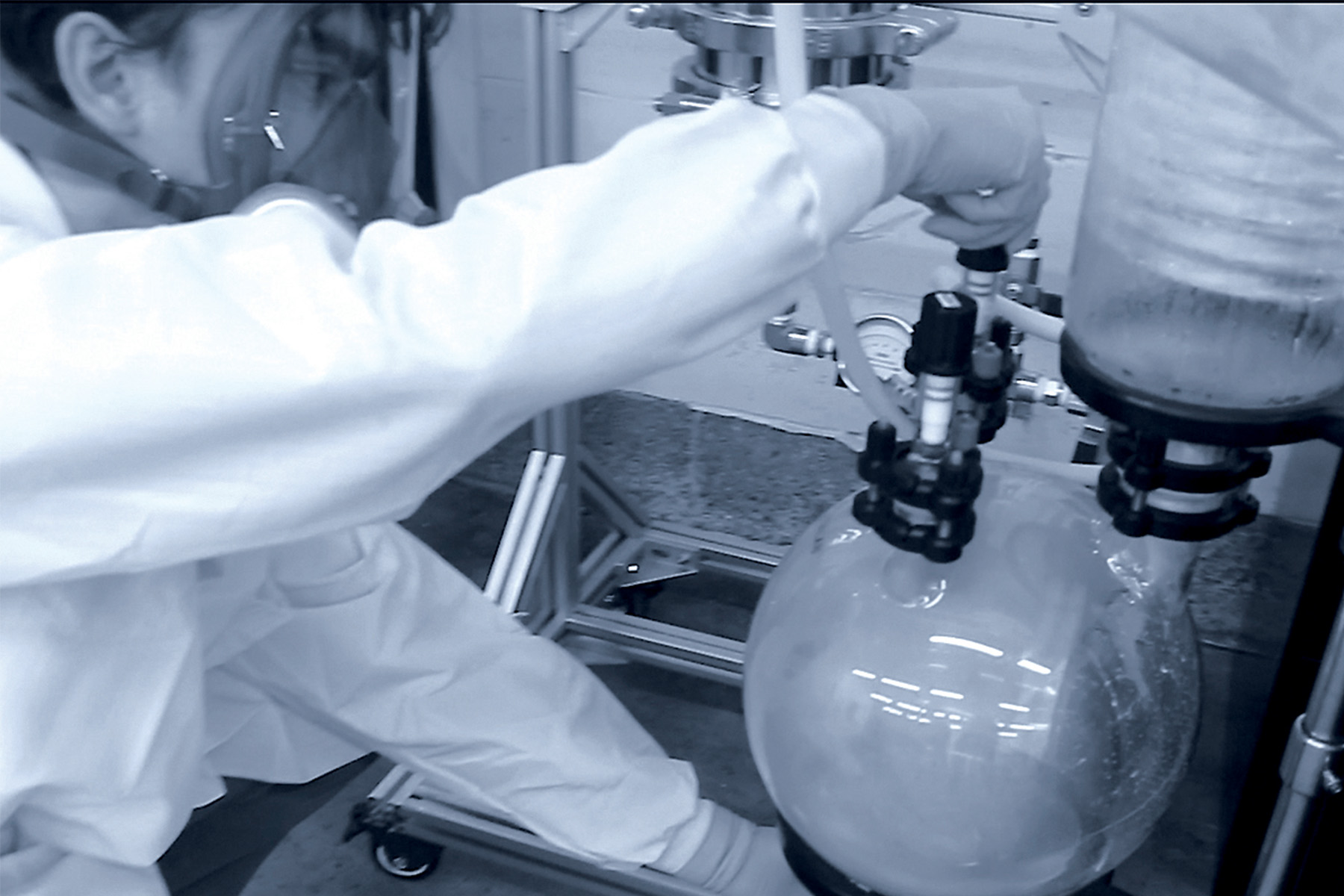
In January 2022, the Environmental Working Group (EWG) targeted the textile industry when it identified more than 1,500 textile mills that may be problem PFAS polluters in EWG’s analysis of 29,900 U.S. industrial sites.
PFAS is a family of synthetic chemicals called per- and polyfluoroalkyl substances used in manufacturing textiles with water and oil repellency, odor and stain resistance and antimicrobial properties. These “forever chemicals,” don’t naturally degrade, and are now found in the water, soil, air and human bodies around the world.
The focus on PFAS pollution and the textile industry is global. In 2021, the Natural Resources Defense Council (NRDC) published “Engaging the Textile Industry as a Key Sector in SAICM: A Review of PFAS as a Chemical Class in the Textile Sector.” The Strategic Approach to International Chemicals Management (SAICM) named the textile industry as one of its four priority sectors, reporting that “more than 8,000 chemical substances are potentially used in the textile industry” and that “a significant portion of PFAS in manufacturing waste streams are released into industrial wastewater treatment plants” that cannot adequately capture PFAS.
PFAS regulations abound, and more is expected. The Environmental Protection Agency (EPA) has said it will issue a final rule designating perfluorooctanoic (PFOA) and perfluorooctane sulfonate (PFOS), two of the most common PFAS compounds, as “Hazardous Substances” under the Comprehensive Environmental Response Compensation and Liability Act (CERCLA), a k a Superfund, this summer. The ruling would create “cradle-to-grave” requirements of PFOA and PFOS, authorizing the EPA to order investigations and remediation of sites impacted by the compounds and to recover costs incurred for remediation.
In October 2021, the EPA said it would initiate the process to add PFOA, PFOS, Perfluorobutane sulfonic acid (PFBS), and hexafluoropropylene oxide dimer acid (commonly known as GenX) as “Hazardous Constituents” under the Resource Conservation and Recovery Act (RCRA), which would lead to site investigations, remediation actions, and increased waste management recordkeeping and costs.
In the meantime, the EPA released a memorandum on April 28, 2022, stating that it would use the National Pollutant Discharge Elimination System (NPDES) program established by the Clean Water Act “to restrict PFAS discharges to water bodies.” The EPA issues all NPDES permits in Massachusetts, New Hampshire, New Mexico, the District of Columbia, U.S. territories (except the Virgin Islands), tribal lands, and some federal facilities. Other states could adopt the EPA’s guidance.
The EPA memo specifically names textile mills and leather tanning and finishing as industrial direct dischargers and outlines two primary requirements for NPDES permits. The first is quarterly monitoring for 40 PFAS compounds detectable by draft method 1633 and reporting the data in Discharge Monitoring Reports (DMRs). The second is implementing best management practices, “including product substitution, reduction, or elimination for discharges with PFAS.”
In addition to EPA’s actions, more than 50 bills to address PFAS were introduced in Congress between 2021 and 2022, according to policy consulting group Global Counsel. As of May 2022, 20 states had issued widely ranging PFAS standards or regulations for drinking water. More state and federal regulations are expected.
PFAS litigation is on the rise, and the payouts stemming from litigation are often significant. PFAS pollution is also leading to explosive growth in lawsuits. Bloomberg Law reports that more than 6,400 PFAS-related lawsuits were filed in federal courts between July 2005 and March 2022.
Michael Blumenthal, an attorney with McGlinchey Stafford, PLLC, told Bloomberg Law that if PFOA and PFOS are classified as hazardous waste, “there will be so much litigation.”
PFAS Management
PFAS management is developing but still falls short of what is needed. The majority of commercially available PFAS testing detects fewer than 100 PFAS compounds and the development of analytical testing methods has been playing catch-up with the continuously growing list of known PFAS compounds. There have been some calls for a class-based approach to PFAS management that focuses on the C-F bond. The EPA recently published a draft method for adsorbable organic fluorine (AOF) to analyze PFAS as a class. Yet AOF is noticeably less sensitive, does not provide compound-specific information, and is biased toward longer-chain compounds.
The most common methods used for filtering PFAS from wastewater are reverse osmosis, foam fractionation, ion resins, and granulated activated carbon. These methods have difficulty removing short-chain PFAS, especially in wastewater with high concentrations of other organic compounds and ions. Yet the U.S. National Toxicology Program found higher doses of short-chain PFAS have the same harmful health effects as their long-chain counterparts, C&EN reported.
PFAS-filled filters are sent to landfills or incinerated, which merely transfers the compounds to another environmental matrix. Incineration breaks long-chain PFAS into small-chain PFAS that are spread by ash and smoke. The U.S. Department of Defense recently banned incineration of PFAS materials. Some states, the EPA and other countries are poised to enact bans.
Besides the recontamination issue, both landfill and incineration disposal methods for PFAS are becoming too expensive, especially since the originator of the waste may still hold significant liability risk.
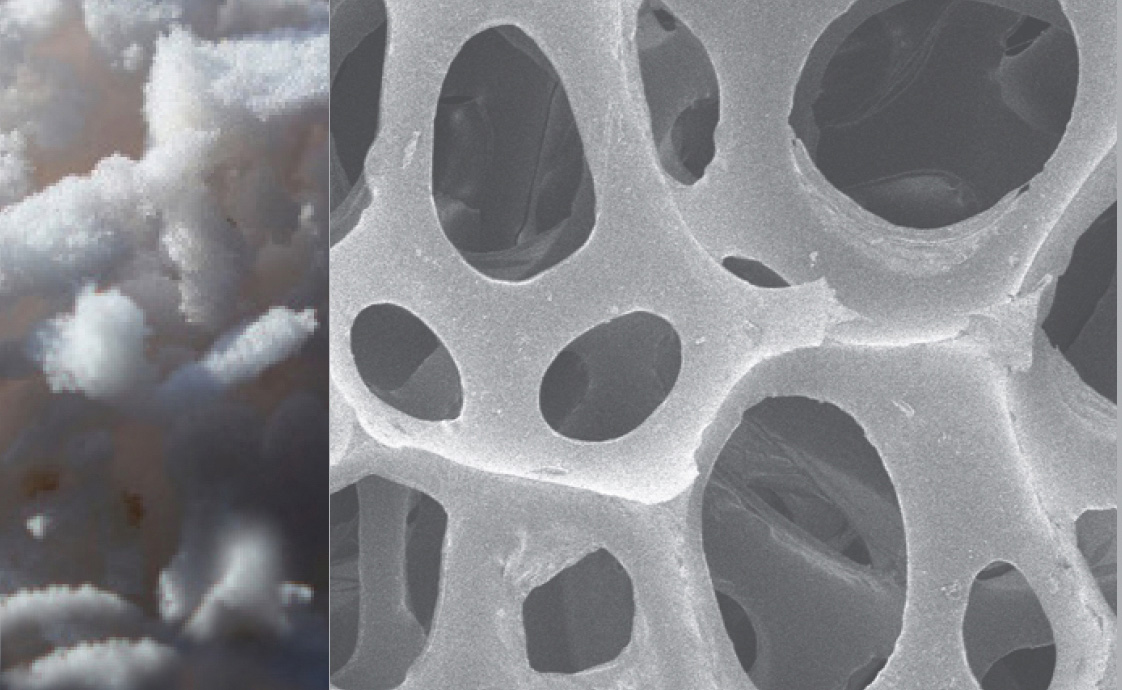
Solving the PFAS Problem
New technologies developed and incubated at the University of Minnesota and now being commercialized by Claros Technologies hold the promise of destroying PFAS, taking the “forever” out of “forever chemicals.” The innovative technologies detect and destroy PFAS in wastewater, leaving only clean, detoxified water and naturally occurring elements.
The first step is PFAS testing that uses both compound-specific methods as well as methods that address PFAS as a class, such as AOF and total organic fluorine (TOF). This type of in-depth analysis is necessary to design customized remediation strategies. This is nascent technology, and Claros Technologies is one of only three accredited labs in the United States that can detect short- and ultrashort-chain PFAS.
The second step is capture and concentration of all short- and long-chain PFAS. New proprietary chemistries and concentration methods developed at Claros are proving more efficient in enhancing the capture and concentrating of PFAS. They can be used alone or tailored to fit with existing capture systems such as ion resin and foam fractionation, making wide-scale adoption more feasible. Reducing millions of gallons of wastewater into a few gallons of PFAS concentrate makes destruction more manageable and affordable.
The final step is permanent destruction of PFAS. Defluorination is accomplished with Elemental Destruction, which uses a photochemical process to break the powerful C-F bond and stands alone in being effective in destructing long-chain, short-chain and ultra-short-chain compounds while operating at the highest energy and cost efficiencies available.
Dr. John Brockgreitens, Claros director of research and development, says, “Adopting a closed-loop system for chemical waste is a necessity. It protects public and environmental health, ensures regulatory compliance and mitigates legal liabilities for manufacturers and waste disposal companies.”
PFAS testing and remediation are critical for the textile and leather industries and the related apparel and footwear industries. Equally important is prevention. The question is whether there is a way to provide the performance properties that consumers have grown to expect, without PFAS.
Amy Phillips is a writer based in California.