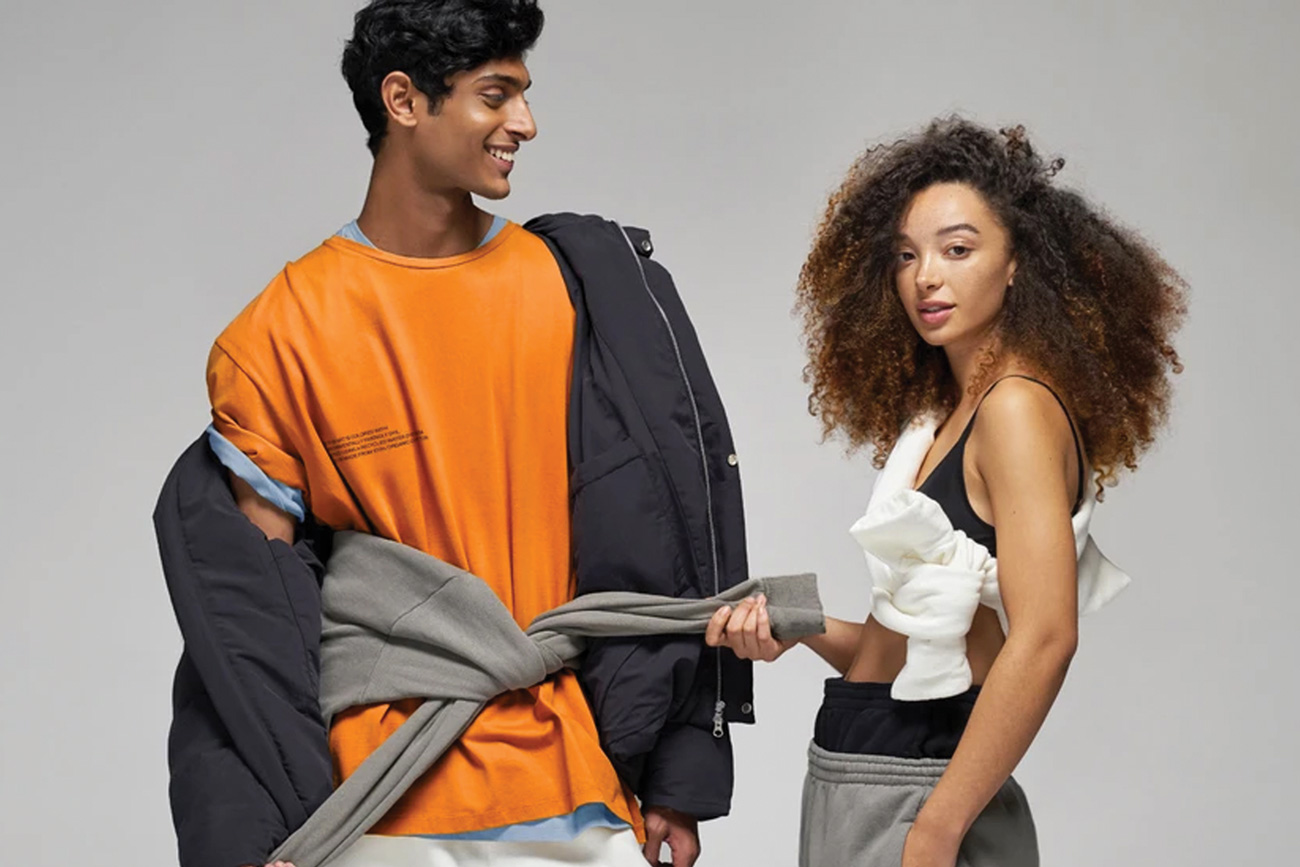
Performance Plus
Building on Established Tech with New, Nature-Inspired Innovations.
Performance Plus
Building on Established Tech with New, Nature-Inspired Innovations.
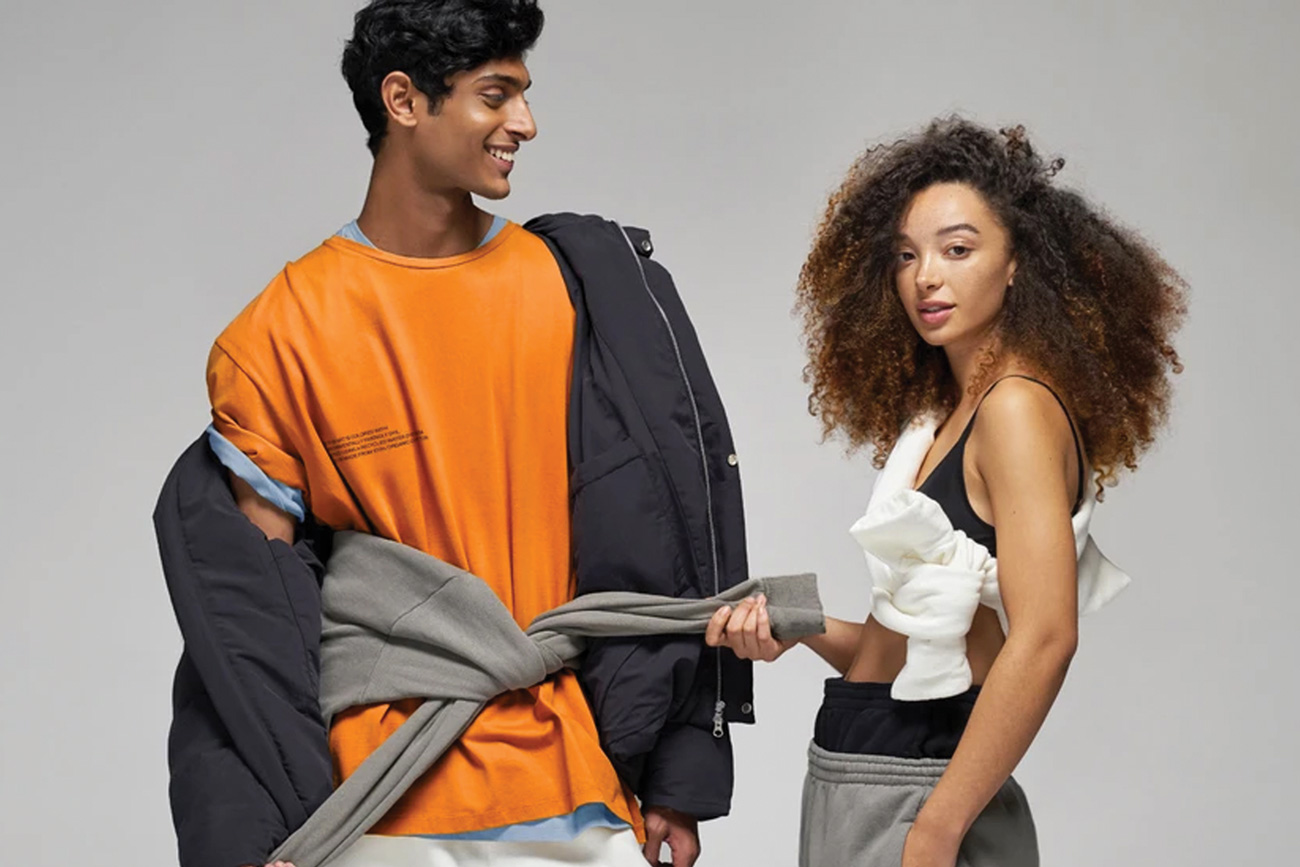
While brands and consumers alike appreciate functional fabrics — offering performance benefits such as odor control, moisture management, and weather protection — many are starting to question exactly what kind of mad science goes into them.
According to McKinsey & Company’s report The State of Fashion 2020, “45% of apparel companies surveyed by McKinsey are looking to integrate more innovative bio-based materials, and over 67% of sourcing executives state that the use of innovative sustainable materials will be important for their company.”
As a result, textile innovators are starting to create performance fabrics that replace traditional chemistry with bio-based or bio-mimetic technologies.
Nature-based Odor Control
Life Natural, an odor-control technology for textiles and polymers from Thailand’s Life Material Technologies Limited, is based on peppermint oil.
According to Lisa Owen, the company’s North American business representative, peppermint oil has long been used as a natural substance to inhibit the growth of odor-causing bacteria. “It’s a sustainable chemistry that’s a great alternative to metal-based antimicrobials and odor-capture technologies,” she explains.
“Everything old — of natural origin — is new again, but better.” — Lisa Owen, Life Material Technologies Ltd.
Life Natural is applied to textiles during manufacturing, is durable through multiple washings, and is cost-competitive with current silver, silane-quat or zinc antimicrobials.
Sourced from sustainable plants, the peppermint extract used as the active ingredient is also used in oral hygiene products (toothpaste, mouthwash, etc.) Applied to textiles, footwear, and fitness equipment, it has no smell or sensory impact. Most importantly, it passes relevant tests for efficacy and safety.
Life Natural has already been adopted by Columbia Sportswear and ethical clothing brand Pangaia, as well as by UK retailers Marks & Spencer and John Lewis.
“Everything old — of natural origin — is new again, but better,” quips Owen.
Act Like a Tree
The nature-based principle of capillary action inspires TurboDry, a non-chemical, patent-pending textile technology that relies on physics to draw moisture one way, to the outside of the garment. TurboDry is the creation of Dr. Jason (Jun-Yan) Hu, CTO of Atlanta-based NexTex Innovations.
Chad Lawrence, NexTex CEO, explains that while the innovative knit constructions utilize two or more yarns or “threads,” unlike old denier-gradient technologies the technology doesn’t rely on differing denier-per-filament ratios.
“Denier-gradient fabrics have construction limitations, and weren’t always soft next to the skin,” says Lawrence.
Dr. Hu’s process leverages the physics of contact angles and capillary action in a range of knitted fabrics typically using commercially available filament yarns, spun fibers, and various fiber blends.
"While spandex makes fabrics difficult to recycle, we are able to use other stretch polymers so that we can engineer what the brands need and desire.” — Chad Lawrence, NexTex
Lawrence is particularly excited about the sustainable aspects of TurboDry fabrics, which can be made with recycled polymers, and easily recycled if constructed of a single polymer type. The reduction of chemicals used during manufacturing also helps lower the Higg Materials Sustainability Index score.
TurboDry technology is physical and will not wash out; in many cases the moisture transport actually improves after washing, based on AATCC 195 testing.
The company has also developed TurboDry elastomeric fabrics, according to Lawrence. “While spandex makes fabrics difficult to recycle, we are able to use other stretch polymers so that we can engineer what the brands need and desire,” he says.
The company currently offers some 22 TurboDry fabrics and is in the process of developing additional constructions.
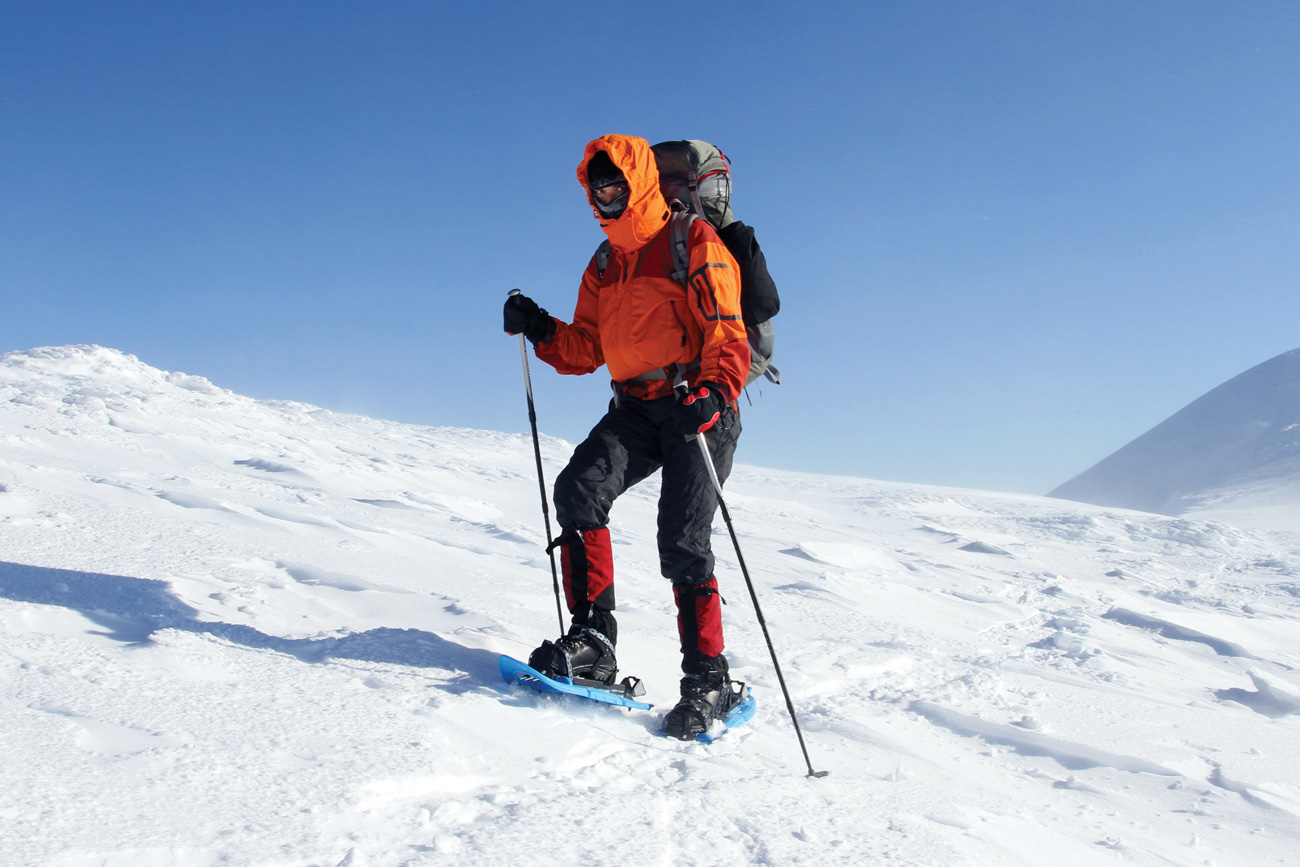
Personalized Climate
Few technologies are more critical to comfort in the outdoors than waterproof, breathable outerwear. With sustainability now top-of-mind, outdoor companies continue to search for the optimal combination of water and wind repellency, breathability and moisture flow, and durability.
AIRADIGM, a new waterproof, breathable membrane system created using microventing plasma technology, is being called “a paradigm shift” in personal comfort. “Adventure is personal,” says Greg Vas Nunes, CEO of Trinity Tech Group (TTG), the Missouri-based maker of membranes for footwear, protective and military apparel.
“Most waterproof, breathable products give up something. Airadigm gives up nothing.” — Greg Vas Nunes, Trinity Tech Group (TTG)
The microventing mechanism keeps wind and water out while allowing body heat and moisture to escape, promoting what the company is calling an “I-Climate,” or personalized body comfort zone.
TTG’s proprietary, made-in-America technology begins with an ePTFE layer that is laminated to a substrate as required. The magic happens in the vacuum chamber, where a very small amount of waterproofing chemical is vaporized into a gaseous state, creating a charge that permanently bonds the monomer to the multi-layered fabric.
The process encapsulates every fiber without blocking the fabric’s pores unlike traditional DWR finishes that only treat the fabric surface.
The pulse plasma treatment replaces the equivalent of two 55-gallon drums of chemical bath, according to Vas Nunes. No gasses are released into the atmosphere, and no polyurethanes or PFOA are involved.
The treatment can be applied to both knits and wovens, and the resulting fabrics are not only waterproof but oil and stain resistant as well. The fabrics are soft and pliable, appropriate for active apparel, footwear, gloves, packs, tenting, etc., and can be customized through various constructions and layering configurations.
“We are building on an older technology (ePTFE), but the twist is that we’ve taken away the negatives,” says Vas Nunes. “Most waterproof, breathable products give up something. Airadigm gives up nothing.”
Textile innovation requires a lot of science and capital investment, Vas Nunes points out; but it needn’t rely on harmful chemicals.