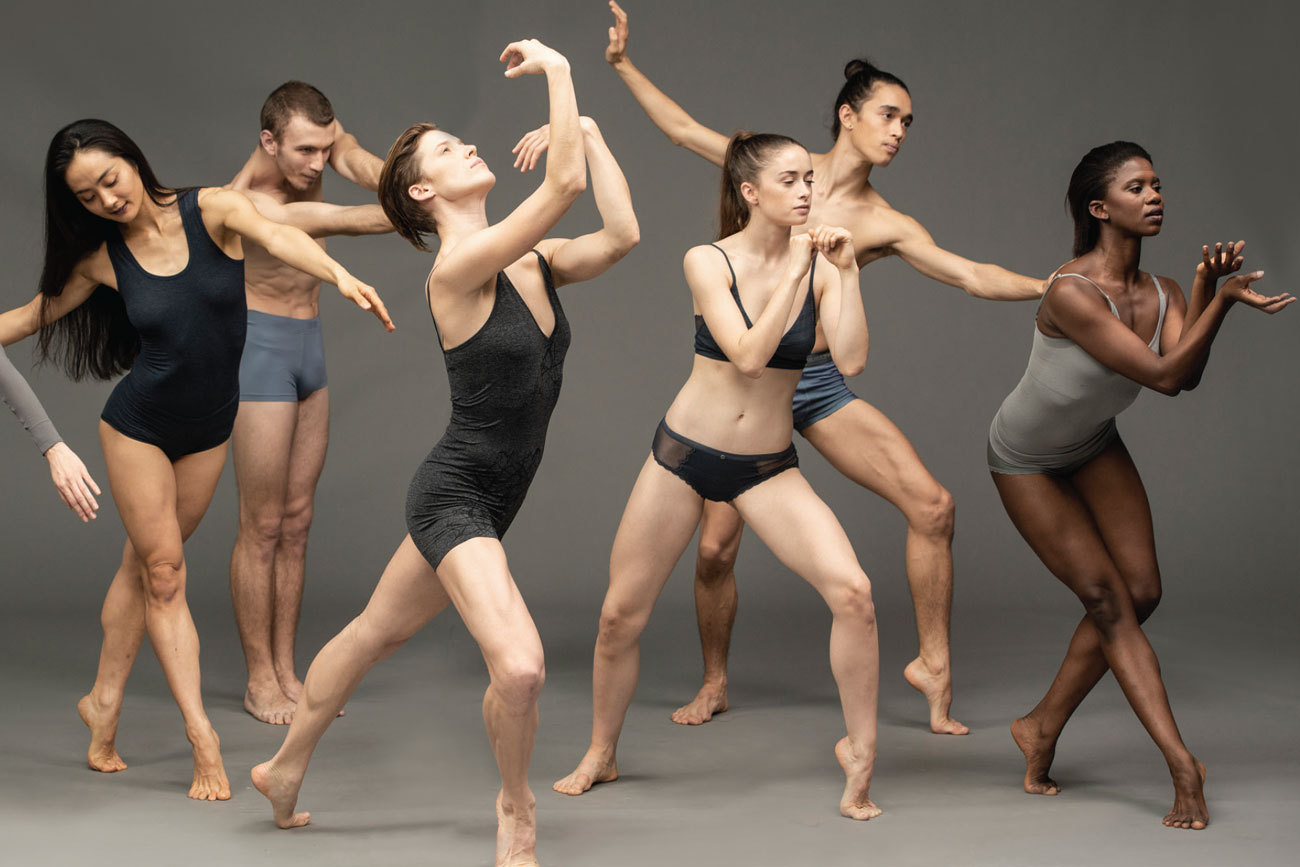
Dyeing for Change
New Advances Offer Improved Sustainability, Speed & Efficiency.
Dyeing for Change
New Advances Offer Improved Sustainability, Speed & Efficiency.
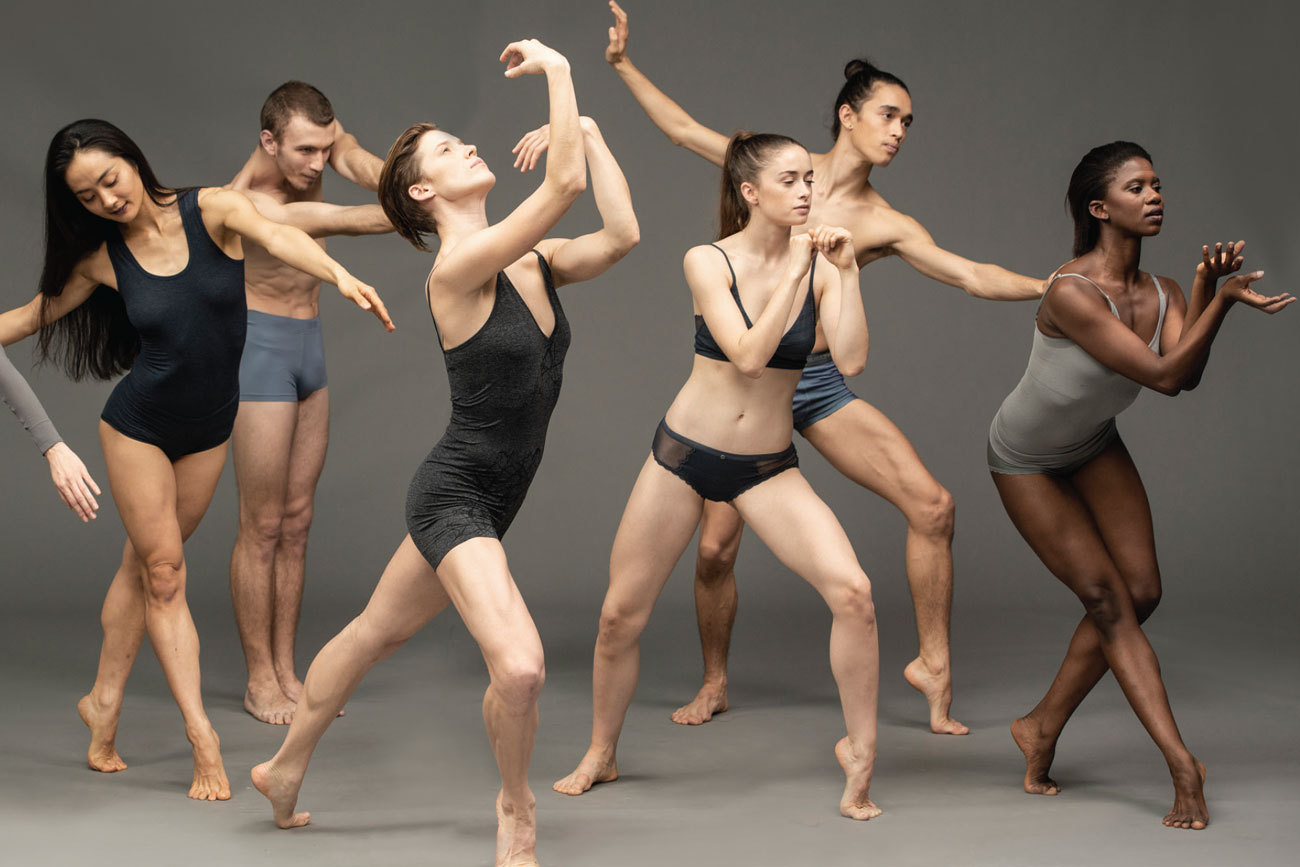
Dyeing and finishing — the wet processing stage of textile manufacturing — has historically been a dirty business. The Tier 2 stage of the textile supply chain (which includes pre-treatment, coloration, and finishing) makes up 52 percent of the industry’s GHG emissions, according to Fashion for Good’s January 2022 Textile Processing Guide.
The report identifies the wet processing stage of textile manufacturing as “often overlooked and a critical area for pivotal and positive change.”
By 2015 the textile industry was using more than 8,000 chemicals to make the 400 billion m2 of fabric sold annually around the world, says a report from Chemical & Engineering News. That processing results in 20 percent of global water pollution.
Fortunately, change is happening. New dye technologies such as bio-based and digital dyeing hold the potential to reduce water pollution, GHG emissions, and waste in the supply chain.
The chemical industry is also working hard to innovate and reformulate their products to reduce or eliminate toxicity while continuing to offer a full range of achievable, colorfast shades.
Dyeing Goes Digital
The digital transformation of the textile industry is empowering a shift from wet to dry dyeing. Based in Cambridge, England, Alchemie Technology Limited’s Endeavour digital process drives a high velocity dispersion of droplets into the fabric. Application of infrared radiation promotes chemical reactions and physical diffusion of the colorant to the fiber with three-dimensional homogeneity.
As a result, 100 percent of the colorant ends up in the fabric, creating high color fastness, and eliminating the post-dyeing wash cycle.
An Endeavour production line uses 95 percent less water and 85 percent less energy, allowing manufacturers to both improve sustainability and reduce dramatically increasing energy costs. In addition, the ability to do shorter, on-demand dye runs reduces excess inventory and waste.
“Textile wet processing is the largest contributor to carbon emissions in the supply chain, and brands are needed to push innovative new technologies into their supply chains. Our unique new process technologies for dyeing and finishing (via the Fashion For Good Dry Factory project) will enable brand partners such as H&M, adidas, Kering, PVH Corp., Arvind Limited, and Welspun Group to transform the environmental impact of their products,” says Simon Kew, Alchemie managing director.
“Fashion For Good’s Dry Factory project is a great example of how brands have started to support new technologies into market,” adds Kew. “However, we do still need more direct investment from brands to support their manufacturers to switch to sustainable technologies.”
Dyeing Goes In-house
Israeli-based Twine Solutions Limited is a waterless, digital system for custom dyeing of polyester thread and yarn, using specialized ink cartridges and requiring no pre- or post-treatment.
Twine’s proprietary algorithms automatically create a recipe specifically to the thread type, and initiate highly accurate ink mixing of Twine’s four basic ink colors. Once dyed, the yarn or thread passes through a treatment chamber and then into the drying unit, where the ink is fixed into the fibers.
“Textile wet processing is the largest contributor to carbon emissions in the supply chain, and brands are needed to push innovative new technologies into their supply chains.” – Simon Kew, Managing Director, Alchemie
Thread giant Coats is a strategic investor in the company, and the first Twine TS-1800 was trialed by Delta Galil in 2018. Twine and Henderson Sewing Machine Company Inc., recently announced a partnership for marketing, sales, and support of Twine’s dyeing system in North America.
The system is designed to be installed and used locally to provide in-house, on-demand dyeing of up to 1,800 meters of polyester thread or yarn per hour, with no MOQs. The technology eliminates wasteful over-production.
Frank Henderson, president of Henderson Sewing Machine Company, points out that Twine’s digital system is also great for whole garment knitting, and is “another step on the digital journey to transform our industry.”
“I think we will see a future that includes the realization of sustainable personalization and customization,” he says.
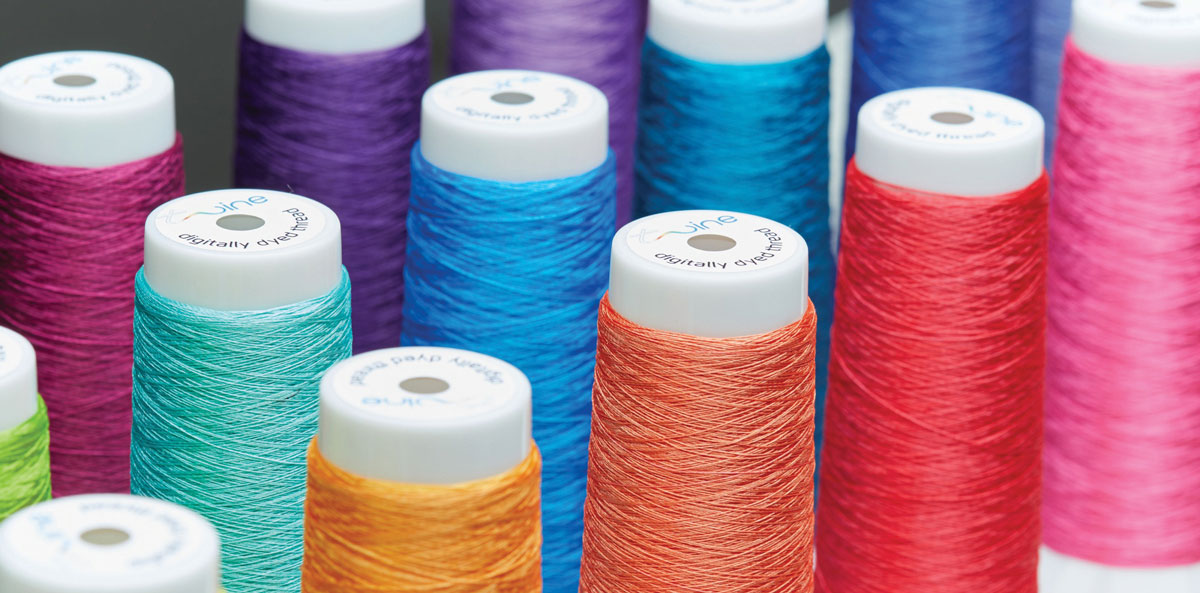
Biology, Not Chemistry
Inspired by the colors found in nature, biotech firm Colorifix Limited produces pigments in the lab by identifying and duplicating the DNA of a pigment-producing organism. Much like a sourdough starter, a small amount of the engineered bacteria is shipped to the customer’s manufacturing site, where it is grown via fermentation using renewable feedstocks.
The dye liquor can then be used in a standard dye machine to dye textiles of natural, synthetic, or blended fibers without the use of toxic chemicals, heavy metals, or organic solvents. The dyed textiles meet industry standards for color fastness.
Colorifix’ genetically modified organisms (GMOs) are Class 1 activities, considered by the European Commission to be of zero or negligible risk. In the final stage of dyeing, the dye bath is heated to 95˚C for five minutes, which inactivates all of the microbes.
The final wash step removes all biomass, resulting in a sterile, non-GM dyed product. Colorifix waste is compatible with existing waste treatment for the industry and poses no contamination problem.
Compared with the standard dyeing process for cotton, Colorifix’ technology reduces water consumption by 49 percent, electricity use by 35 percent, and CO2 emissions by 31percent. Based in Norwich, England, the company is currently serving a number of international textile mills.
“Our customer acquisition strategy is two-pronged: engaging directly with manufacturers of interest or engaging with brands who then connect us with their supply chain,” explains Alexandra Ting, outreach manager for the company.
“After product launches with H&M and Pangaia, we are currently working with several other leading retail, luxury and sportswear brands who align with our sustainability values,” she continues.
“There has been overwhelming interest in more sustainable and ethical products and practices from both brands and manufacturers (and the end citizen consumer), so the real challenge has been scaling up quickly enough to respond to the demand!”
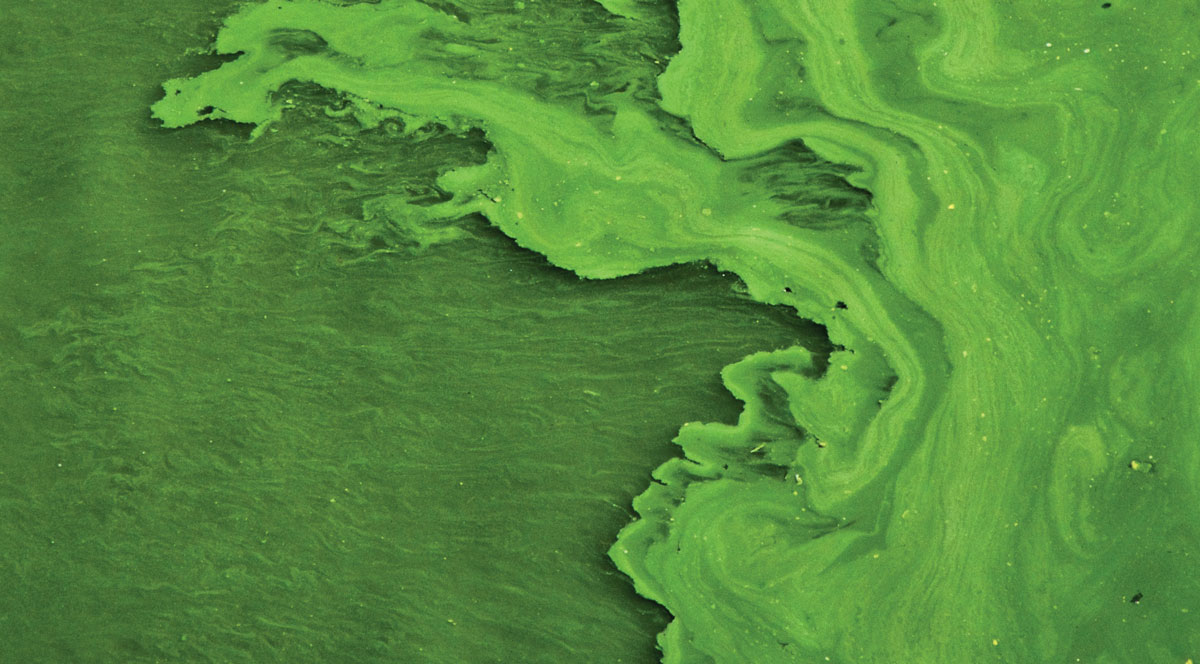
Dyeing Gets Efficient
A global leader in specialty dyes and chemicals, Archroma has taken a number of steps to promote more sustainable dyeing, including a range of metal-free acid dyes; sulfur dyeing technologies that replace toxic reduction agents with glucose; aniline-free indigo; and a Love Nature X Earthcolors range of colors synthesized from plant waste.
Steve Richardson of Archroma Brand Studio points out that there are misconceptions about natural dyes as they are not necessarily robust enough for functional commercial production, and color palettes are limited. They can require toxic mordants, or be sourced from food competitive crops.
“We see the need to educate brands on dyeing technology. They don’t have a baseline as they don’t know what is in their supply chain,” he believes.
The company’s One Way Impact Calculator is a process simulation and calculation tool designed to provide customers with an accurate estimate of the process costs, resource utilization, effluent discharge quality, and CO2 emissions of an existing production process vs. a newly evaluated system.
Archroma’s System Solutions engineers products to work together to save resources and reduce impacts for dyeing and finishing. For example, Fast Cycle is a particularly efficient Archroma system of disperse dyes that promotes rapid, right-first-time coloration of rPET fibers, using fewer resources and chemicals.
“We are dealing with what we have today to take customers forward to better use of resources and technologies,” says Richardson. “There is great promise in new technologies, but fashion industry interest is slow. We need big leaps as well as incremental changes for billions of units.”