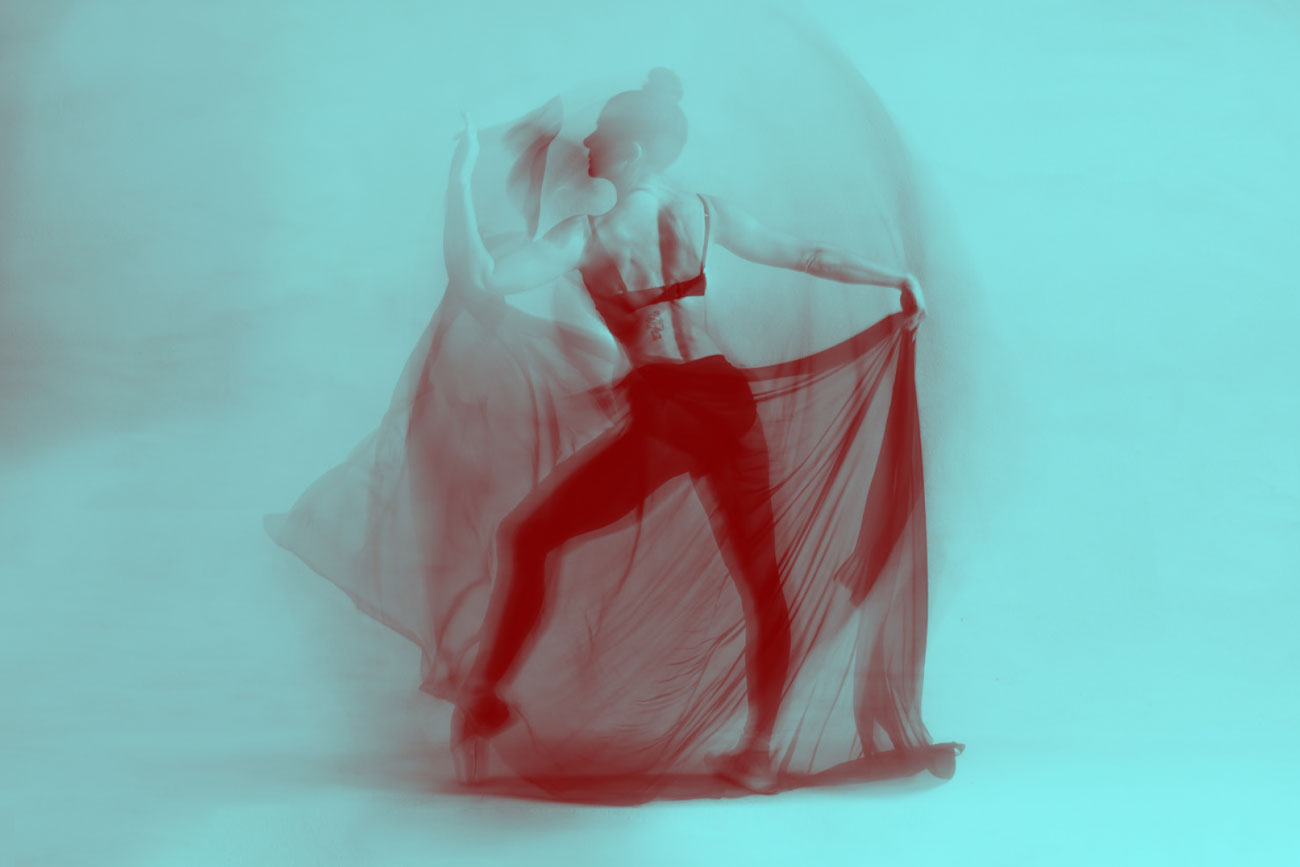
Dancing with a Small Batch Factory
What to expect from a small scale sewing resource.
Dancing with a Small Batch Factory
What to expect from a small scale sewing resource.
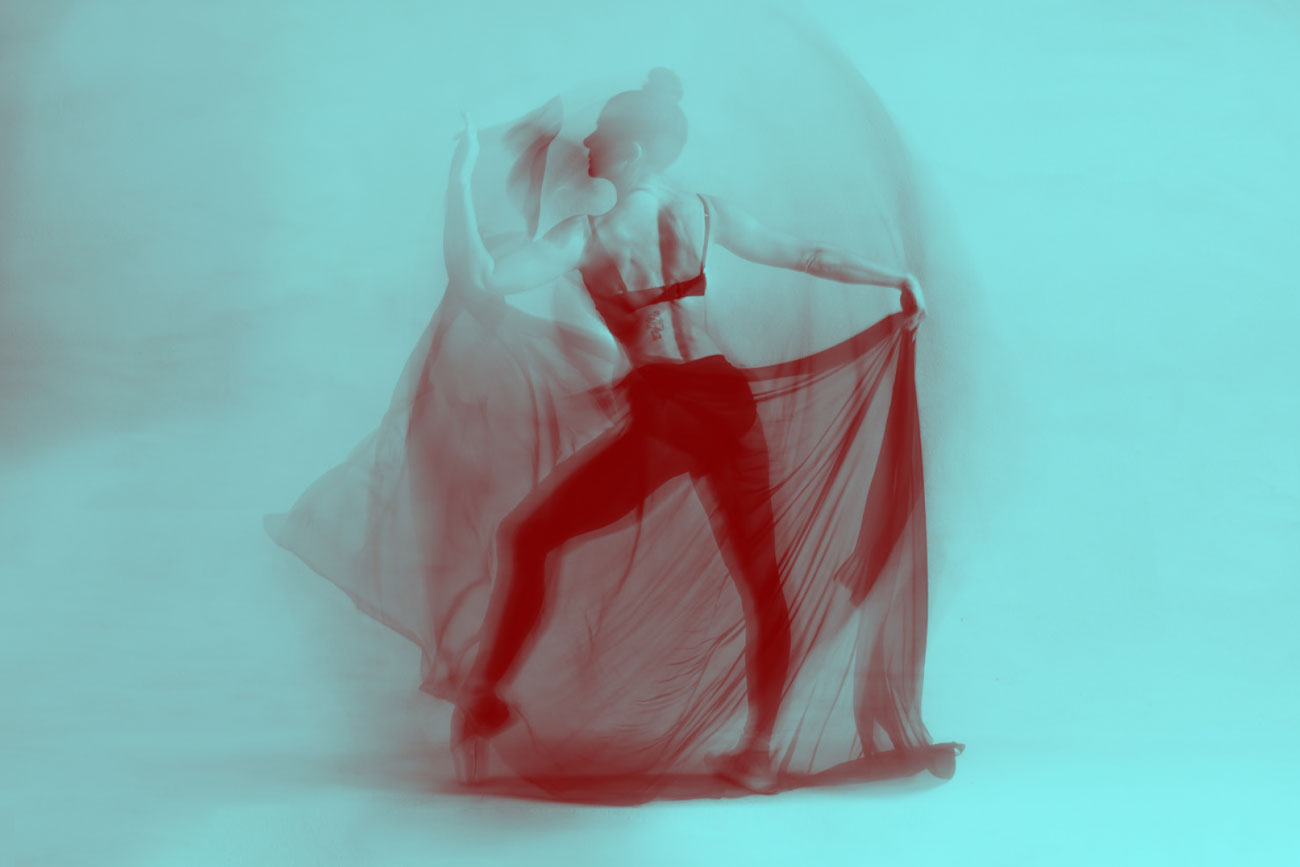
With the recent interest in reshoring amidst the never ending perturbations in the supply chain, both brands and retailers are turning to smaller local factories for a reliable source of sewn goods. This brings people with too little, or too much, manufacturing experience into contact with the world of the small batch sewer. The product tango is similar to what you’d expect from any big factory, but with some key differences. Here are a few things to keep in mind:
Design: Simply said, design must prioritize simplicity over complexity. The design of a product needs to be in harmony with the required manufacturing steps and techniques involved in its production. The designer must know how the product will be made.
Pattern making: The crux for any sewn goods is the creation of the pattern. The problem with patterns is they can be digital or analog or both, and this can lead to confusion with a small maker who still cuts by hand on a table. The efficient cutting of materials is of concern to both factory and customer. Be sure everyone understands how the pattern work translates into the cutting plan.
Development: The customer pays for development in dollars, the factory pays in brain power. The mental cost for a small factory to learn how to make a new gizmo is steep and it is reflected in the reluctance and anxiety around making “samples.” Many factories actually learn to make a product during the initial production run, figuring it out as they go along. In order to make a perfect pre-production sample, the factory needs all that knowledge in advance. It is a good idea to agree in advance about the expectations involved in sampling.
Production: This part of the process is similar across all sewn goods factories, with one caveat; in a small shop, the machines may not be set up to create the seams the product requires. In the big-time sewing world factories are specialized around the kind machines on hand and how those machines are optimized to sew various classes of fabrics and products. There are pant factories, tee shirt factories, backpack factories, upholstery factories, etc. Small batch sewers are often generalists, moving quickly from one project to another while using all kinds of fabrics. Keep an eye on the stitching as it can be a struggle to optimize thread - needle - feed in order to make perfect seams.
Finishing: There isn’t any. Small factories will keep things tidy, but they aren’t really into steaming, tagging and bagging. Quality control is minimal, so it is best to have a forthright discussion early on about production “seconds” and who pays for what when things go wrong.
Materials: By far the biggest hurdle for a small sewing factory is dealing with a wide range of materials. Small batch sewing is by definition CMT style production. CMT stands for cut, make and trim and it is where the customer sources and provides all the parts needed to make a product while the factory does the cutting and sewing. Inevitably problems crop up around inventory control, color, quantity, size, and the ability to easily cut and sew what the customer has purchased. It is important that the small batch maker and the customer are both comfortable with the plan for materials.
You know who makes the best small batch customers? Other small sewing factories. They get it, and are often proactive and collaborative in problem solving. When dealing with a small sewing facility try putting on your own small batch hat and think of what you can do to help make those perfect seams.
Disclaimer: Mr. Gray thinks small batch sewing means making tiny bags. A skill he has perfected. The publisher may not share his opinions but does have some of his bags.