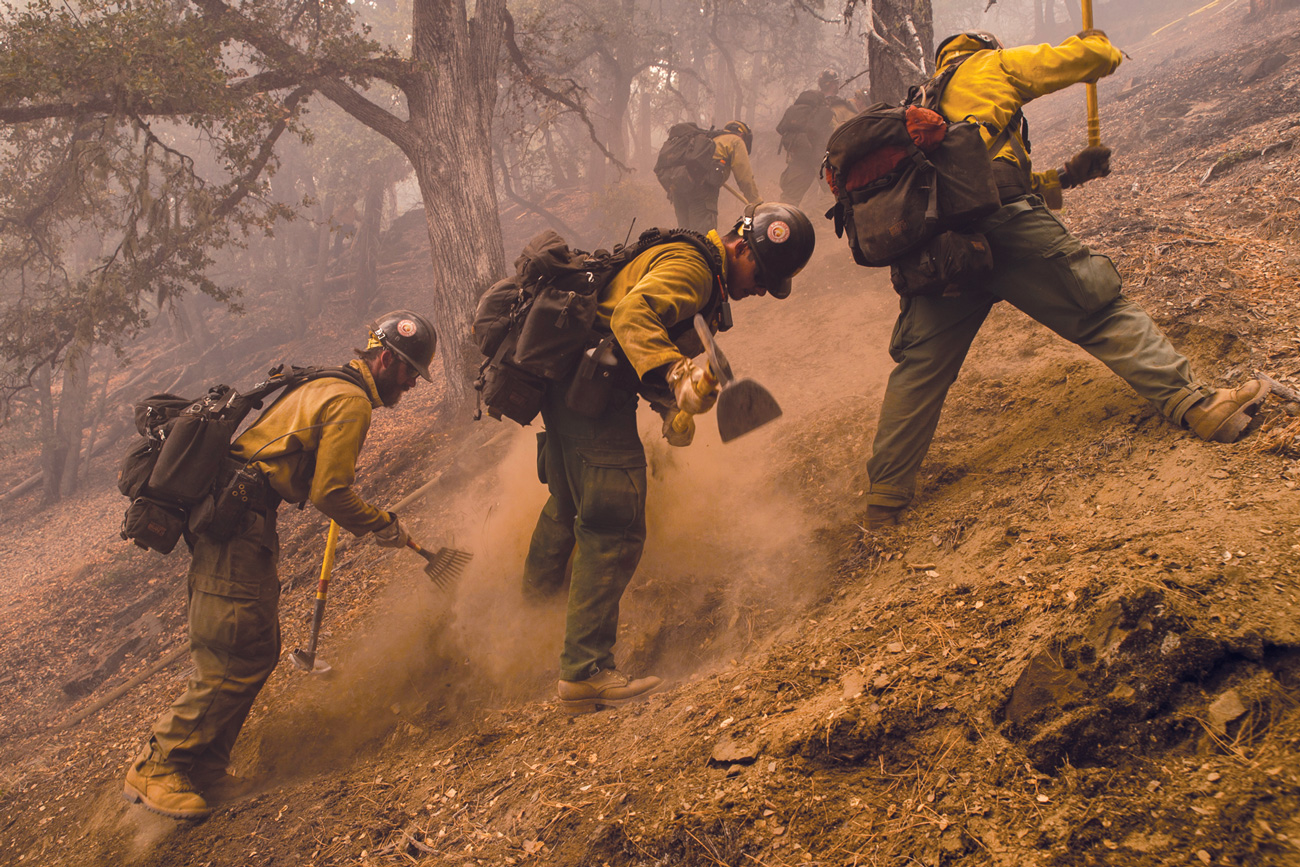
A Wildland Firefighter Weighs In
Raging Wildfires Fuel Need for a Different Kind of FR Protection
A Wildland Firefighter Weighs In
Raging Wildfires Fuel Need for a Different Kind of FR Protection
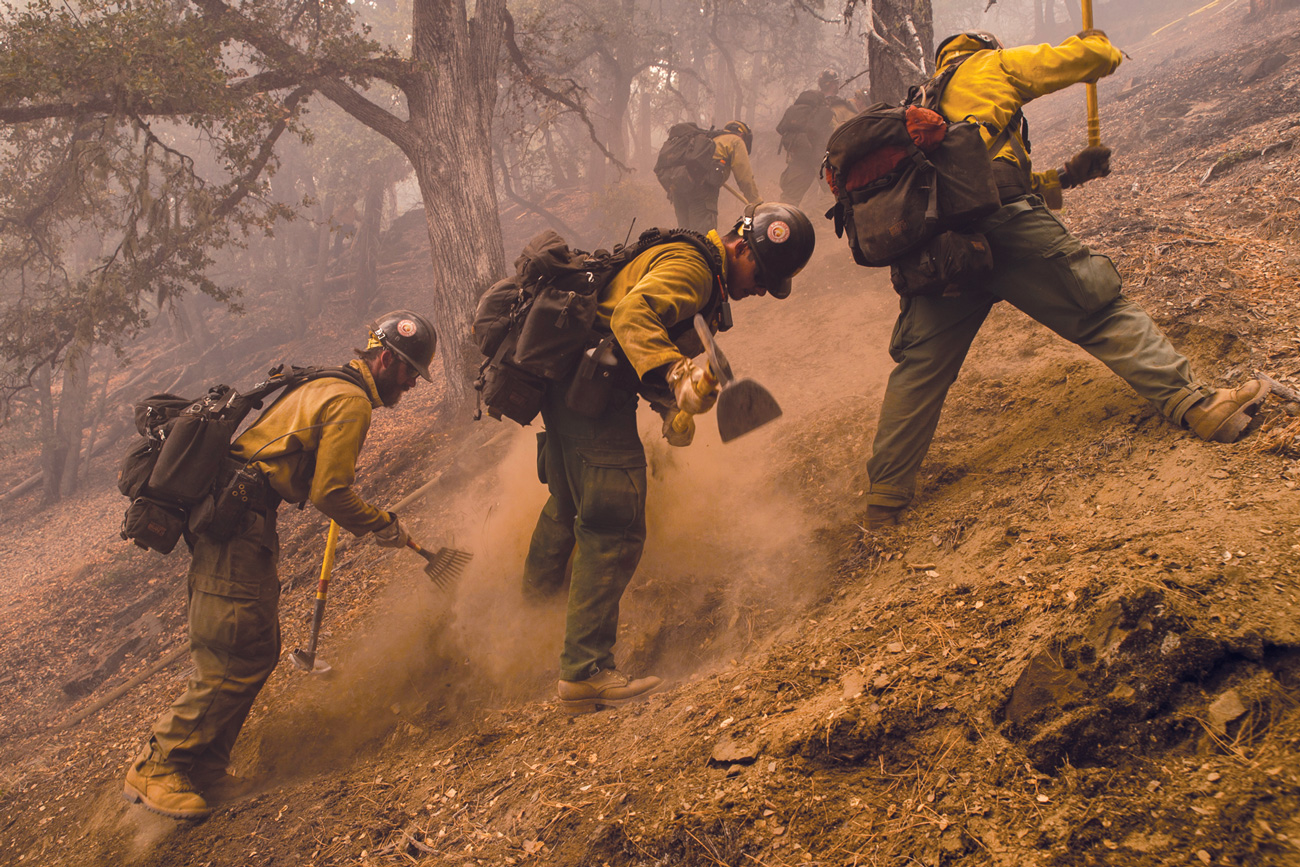
Wildland firefighters (WLFFs), or as they are called by the U.S. government, “forestry technicians,” are finding 2020 to be their most challenging year on record. Fueled by climate change, the hotter, drier conditions have resulted in a massively destructive fire season that seems unending.
Wildland firefighting is different from structural firefighting, although the principles of putting out a fire are the same: Eliminate the fuel, oxygen, or heat source. Working in hot weather, WLFFs dig ditches, fell trees, create backfires, and haul water in the wilderness, all while wearing 50-pound packs carrying their gear. Heat stress is an ever-present threat.
According to a 2017 report published by the National Wildfire Coordinating Group (NWCG), heart attacks are the major cause of fatalities among WLFFs. Clearly, they require a different kind of protection.
Balancing Protection & Comfort
The National Fire Protection Association (NFPA) standard 1977 was created in 1993 specifically to combat heat stress in wildland firefighting.
In addition to setting standards for flame and heat resistance, textiles for WLFFs are qualified for radiant protective performance (RPP) and evaporative heat transfer (total heat loss, or THL).
The traditional go-tos, Nomex, a meta-aramid, and Kevlar, a para-aramid, are inherently FR, with excellent strength and durability. While meeting the standards, the fabrics are stiff and harsh, and have low moisture absorption.
From the Boots on the Ground
Wildland firefighters work for a variety of federal agencies, state institutions, tribes, and private contractors. They’re paid as little as $13 an hour, and don’t get health care.
“Most of our gear is issued to us by the federal government,” says Nick Harper-Johnston, a forestry technician working for the National Park Service. “We wear Nomex both for long sleeve shirts, (affectionately referred to as yellows) and green pants.
Since all of our gear is constructed and issued via federal government contracts, there isn’t much change or innovation. The pants and shirts are not very comfortable.
We wear the same yellows, every day, in all conditions wet, dry, or cold. We wear the same couple pairs of clothes for 14 to 21 days straight! Typically warmer jackets aren’t necessary on fires. But we do camp all summer and fall and so we bring our own personal cold weather gear.”
High-tech, no-melt/no-drip base layers are not issued as part of their kit, says Harper-Johnston: “Some folks wear cotton undershirts, some folks spend money on expensive wool undershirts, and some folks don’t wear anything underneath their yellows.”
According to Harper-Johnston, the Nomex clothing offers incomplete protection when it inevitably becomes saturated with fuel from chainsaws or drip torches. “There’s been several documented burn injuries the last few years where the actual fabric appeared undamaged, while the fire consumed the fuel within the material,” he says.
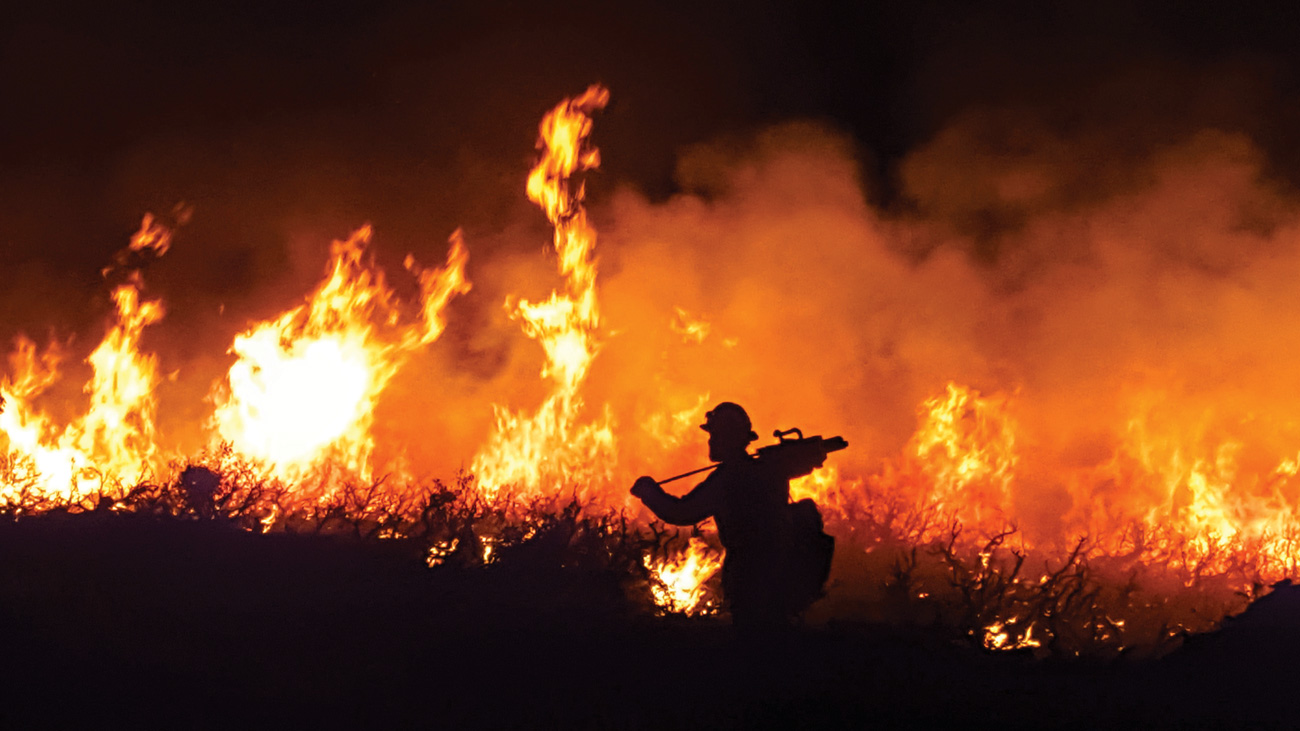
Textile Research Focuses on Improvements
In 2010 the Natick Soldier Center (NSC), along with the Department of Homeland Security (DHS), CalFire, the National Forestry Service, and a number of West Coast fire departments challenged the textile industry to develop FR textiles that would combine excellent protection with improved comfort and durability.
“It is about making textiles that balance radiant heat protection, durability and comfort in hot conditions. Finding that balance is the technical focus of our research at TPACC.” — Roger Barker, Burlington distinguished professor and Director of NC State Wilson College of Textiles’ Textile Protection & Comfort Center (T-PACC)
“It’s one thing to make FR textiles; but how do you also make them comfortable for wildland firefighter clothing?” asks Roger Barker, Burlington distinguished professor and Director of NC State Wilson College of Textiles’ Textile Protection & Comfort Center (T-PACC).
“WLFF gear is not designed to protect from full fire engulfment. WLFFs experience radiant heat at a distance from a fire front,” Dr. Barker points out. “It is about making textiles that balance radiant heat protection, durability and comfort in hot conditions. Finding that balance is the technical focus of our research at TPACC.”
Beyond aramid fibers, alternative FR technologies include modacrylics (better hand, lower cost), and char formers, phosphorous-based additives reacted with cotton or rayon fibers.
“While each technology can provide excellent protection from thermal hazards, leading textile manufacturers with access to multiple technologies can develop fabrics that incorporate more than one technology into a protective textile,” recommends Drew Child, program director for Milliken & Company, in The Science Behind Your FR Clothing for Occupational Health & Safety magazine.
“Utilizing combinations of multiple technologies also allows manufacturers to meet industry requirements while offering performance characteristics, such as durability, lightweight, breathability or mobility.”
Milliken’s ResQ range of FR fabrics exceed NFPA 1977 standards for RPP and THL. The range includes ResQ DH, a blend of Lenzing Lyocell, modacrylic, and aramid, with outstanding moisture wicking properties.
From Safety Components (a division of Elevate Textiles), Sigma Four-Star, a blend of meta-aramid, Lenzing FR, polyamide and para-aramid, was top-rated by DHS and NSC in one of the largest wildland wear trials ever conducted. The 2014 Wildland Firefighter Personal Protective Equipment (PPE) Selection Guide calls out Sigma’s superior rating for rating for RPP and THL.
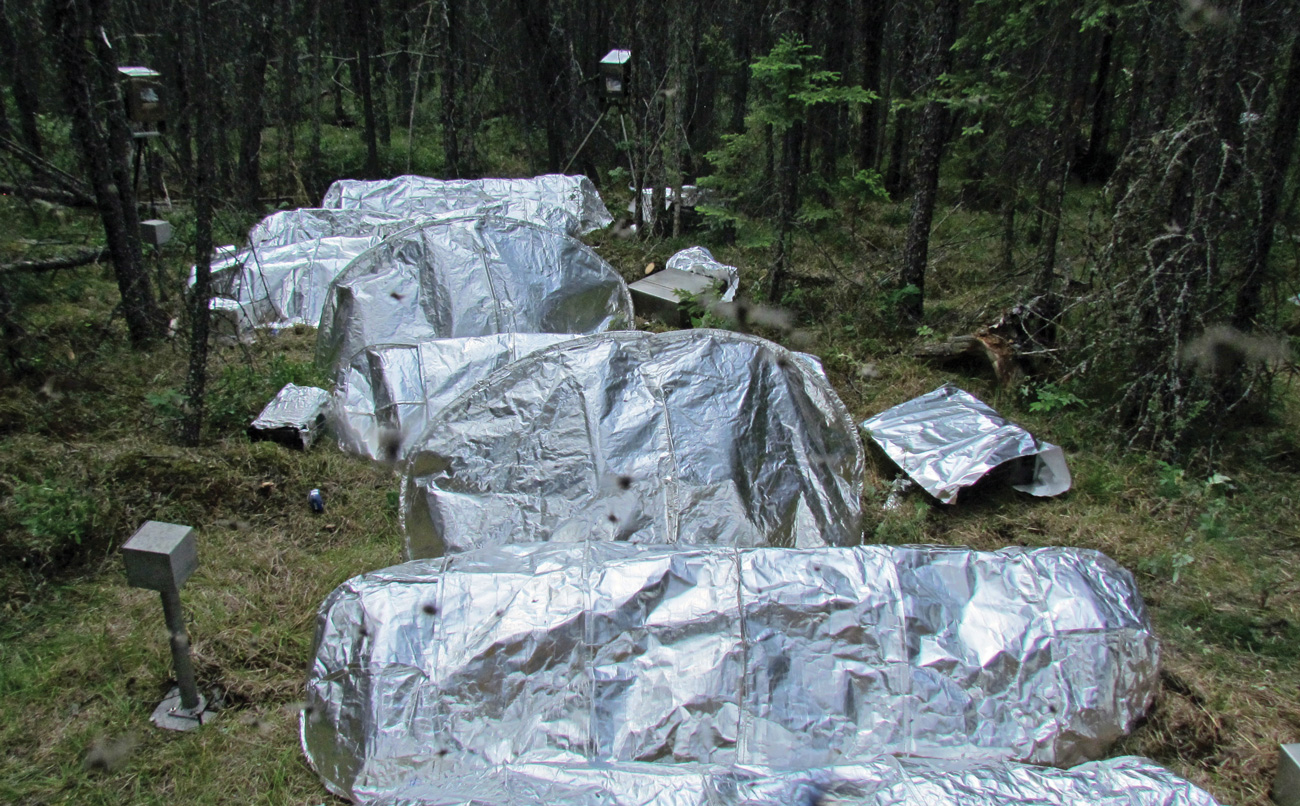
The Last Resort
A critical component of WLFFs’ kit is their fire shelter, which they employ when trapped by fire with no escape route. The “new generation” fire shelter (adopted in 2003) reflects radiant heat while trapping breathable air within.
Weighing 4.2 pounds, the fire shelter consists of an outer layer of aluminum foil bonded to a silica fabric, sewn to an inner layer of aluminum foil laminated to fiberglass. The air gap between the layers offers an additional layer of insulation.
When the temperature reaches 500˚ F, the glue begins to break down and the layers separate, allowing fire winds to tear off the outer layer of aluminum. In 2013, 19 WLFFs died in their fire shelters in the Yarnell Hill fire in Arizona.
“Since all of our gear is constructed and issued via federal government contracts, there isn’t much change or innovation. The pants and shirts are not very comfortable.” — Nick Harper-Johnston, forestry technician, National Park Service
In 2014 the USDA Forest Service initiated an exhaustive fire shelter review in coordination with the NWCG Fire Shelter Subcommittee. New materials and designs were submitted by 23 different entities, including NC State’s T-PACC.
T-PACC researchers developed advanced fire blocking textiles for wildland fire shelters. Their tests showed that prototype fire shelters made from these materials provided improved protection in wildfire burnovers in comparison to the current model.
However, after wear testing the prototypes, the NWCG subcommittee concluded in 2018 that the current fire shelter model, with slight modifications, continues to be the best option, given tradeoffs of weight, volume, durability, and material toxicity.
“Fire shelters do save a lot of lives, but there is a limit to what they are currently capable of,” explains Harper-Johnston. “Weight is a major limiting factor in construction of a better shelter. And we never, ever base our actions with the expectation of deploying shelters. They are last resort survival only.”
Innovation is a word not typically associated with FR fabrics worn by those in the wildland firefighting and tech rescue world, admits a Safety Components product sheet. While the trend is toward lighter weight fabrics, basic WLFF uniforms have changed little in the past 30 years.
Although technical textile companies are developing improved FR fabrics, most target the structural firefighting and industrial markets.
As the danger faced by WLFFs continues to increase, we need to step up efforts to protect them.