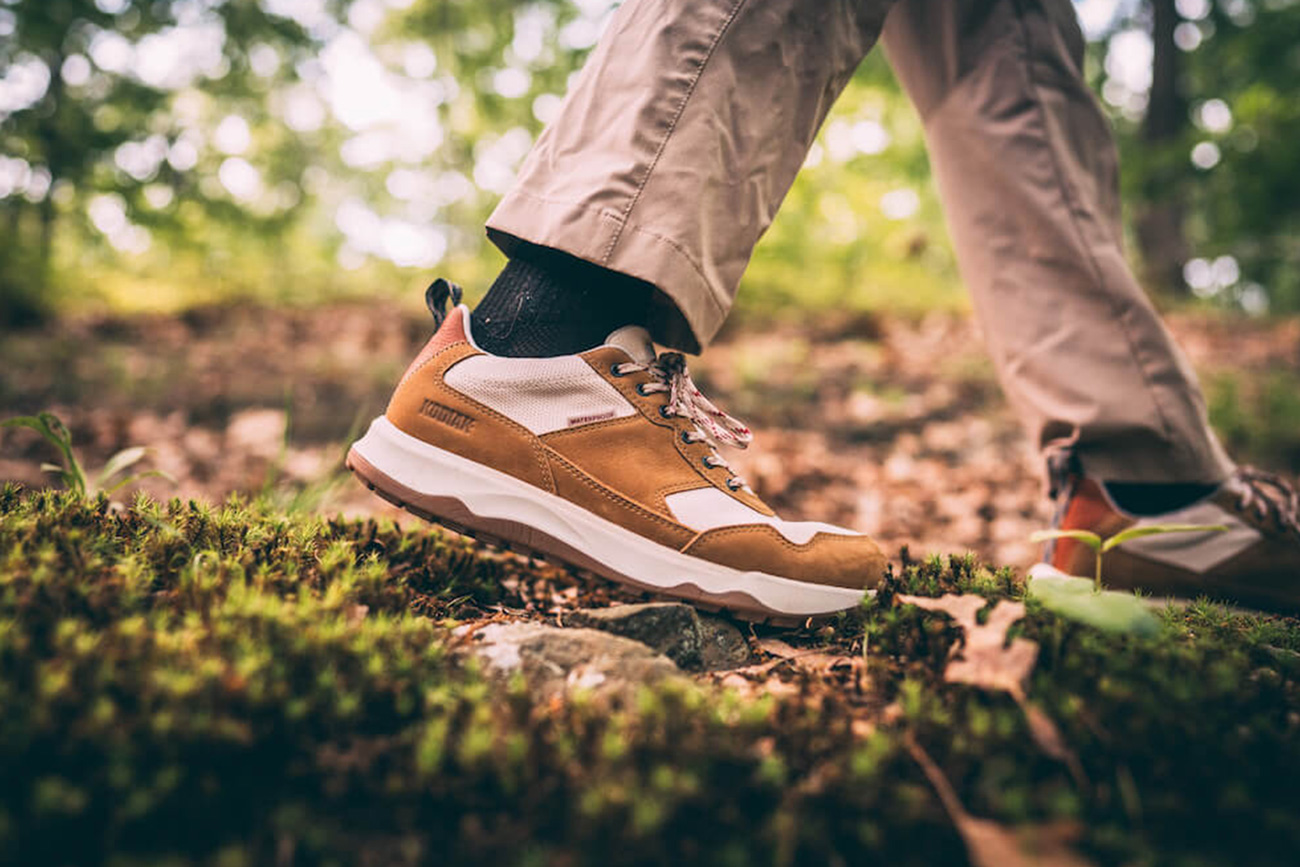
Kodiak Launches “Built for What Matters” Sustainability Initiative
Kodiak Launches “Built for What Matters” Sustainability Initiative
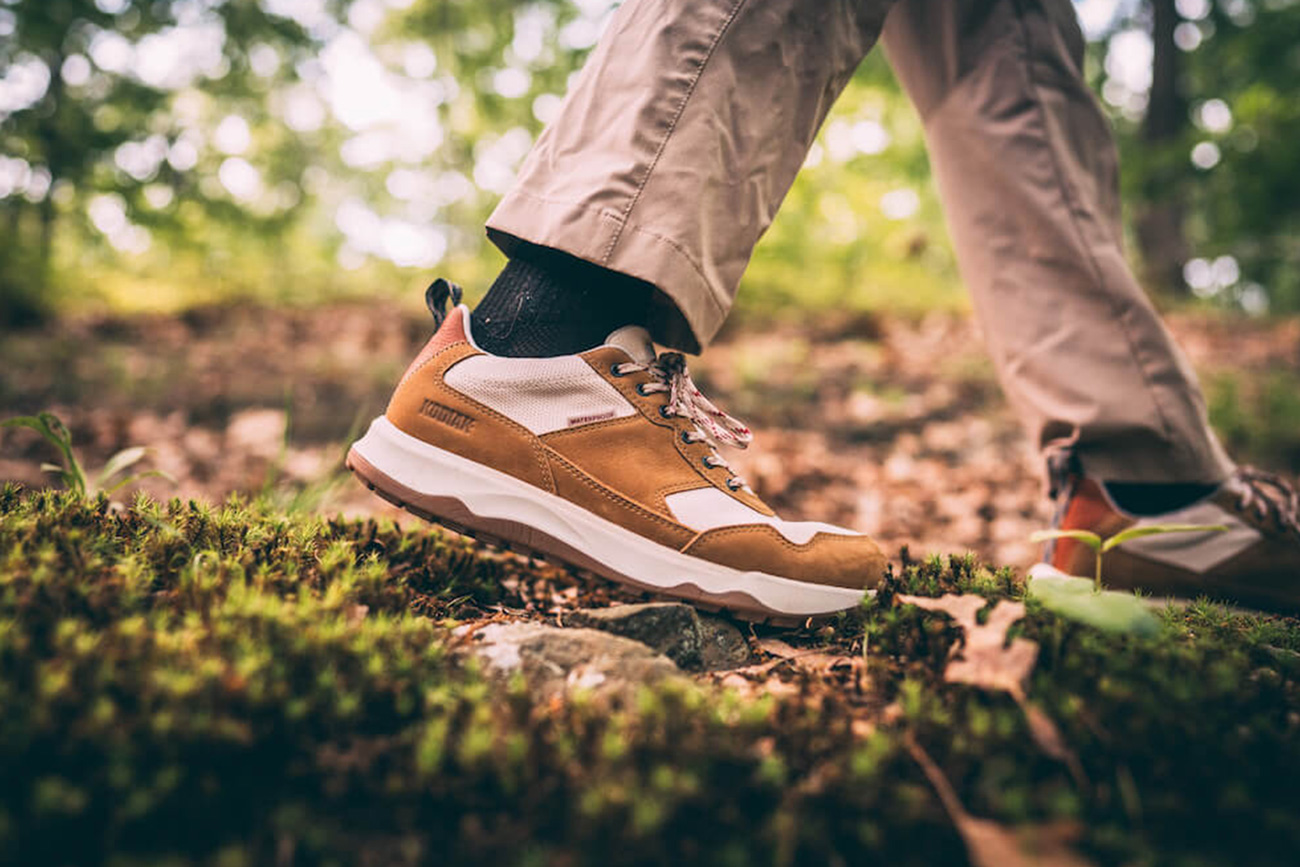
The 110-year-old Canadian boot brand Kodiak is taking steps to reduce its environmental footprint and improve sustainability through a new multi-year, multi-faceted initiative called Built for What Matters. The initiative kicks off with a focus on design and manufacturing, incorporating fewer, more sustainable materials and implementing manufacturing processes that are less impactful to the environment.
“The workwear category as a whole has a lot of work to do to make products that are less impactful to the planet,” said Karen McSorley, Kodiak Senior Brand Manager. “This initiative takes a holistic look at our design and manufacturing processes to identify opportunities to improve. It’s pretty simple really, we build footwear for exploring the planet and we need to do our part to help protect it.”
Kodiak has partnered with many of its suppliers to incorporate less harmful manufacturing practices and more environmentally-considered materials into its Fall 2021 product line. Kodiak will be the first footwear brand to use PrimaLoft P.U.R.E. insulation, made with 100% post-consumer recycled PET plastic using a process that generates 48% less carbon than the traditional insulation manufacturing process.
Additionally, Kodiak’s Fall 21 offerings include leathers sourced from ISA TanTec, tanneries that are rated gold for environmental responsibility by the Leather Working Group. And Kodiak has partnered with Evoco to create the Comfortzone Eco footbed featuring a foam made with 70% plantbased biomass.
As part of its sustainability initiative, Kodiak says it is committed to: Work with partners that offer traceable recycled, organic and renewable materials; Source leather from tanneries rated Silver, Gold or Platinum by the Leather Working Group; Replace oil-based materials with plant-based alternatives; Build for longevity and durability by integrating replaceable and repairable parts; Strive for zero waste in owned and partner manufacturing facilities by considering recycling factory surplus and/or using post-consumer waste; Limit the number of materials and trims used; and thoughtfully assess each material choice that gives equal weight to environmental impact and intended end-use.