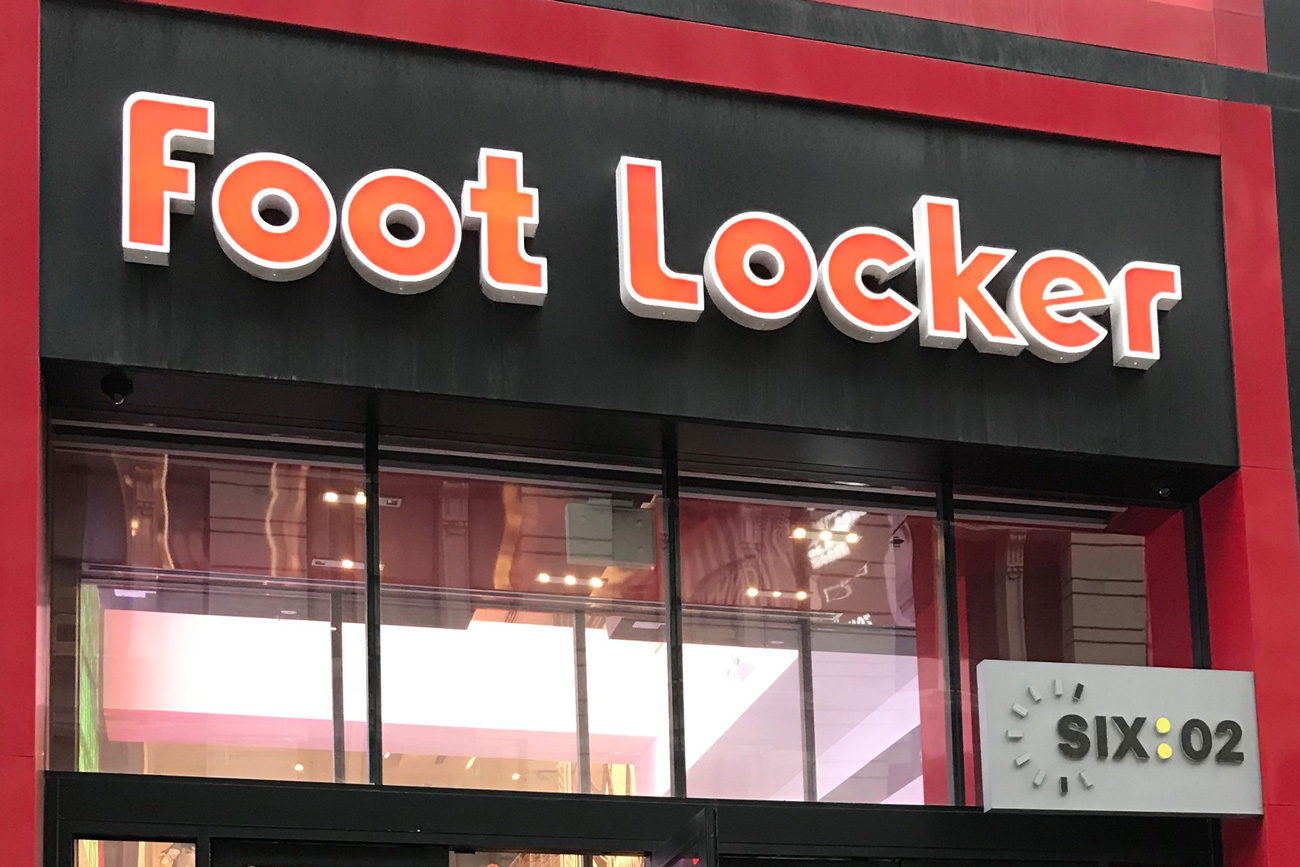
Foot Locker Spends on Supply Chain, Logistics But Could Face Pitfalls
Foot Locker Spends on Supply Chain, Logistics But Could Face Pitfalls
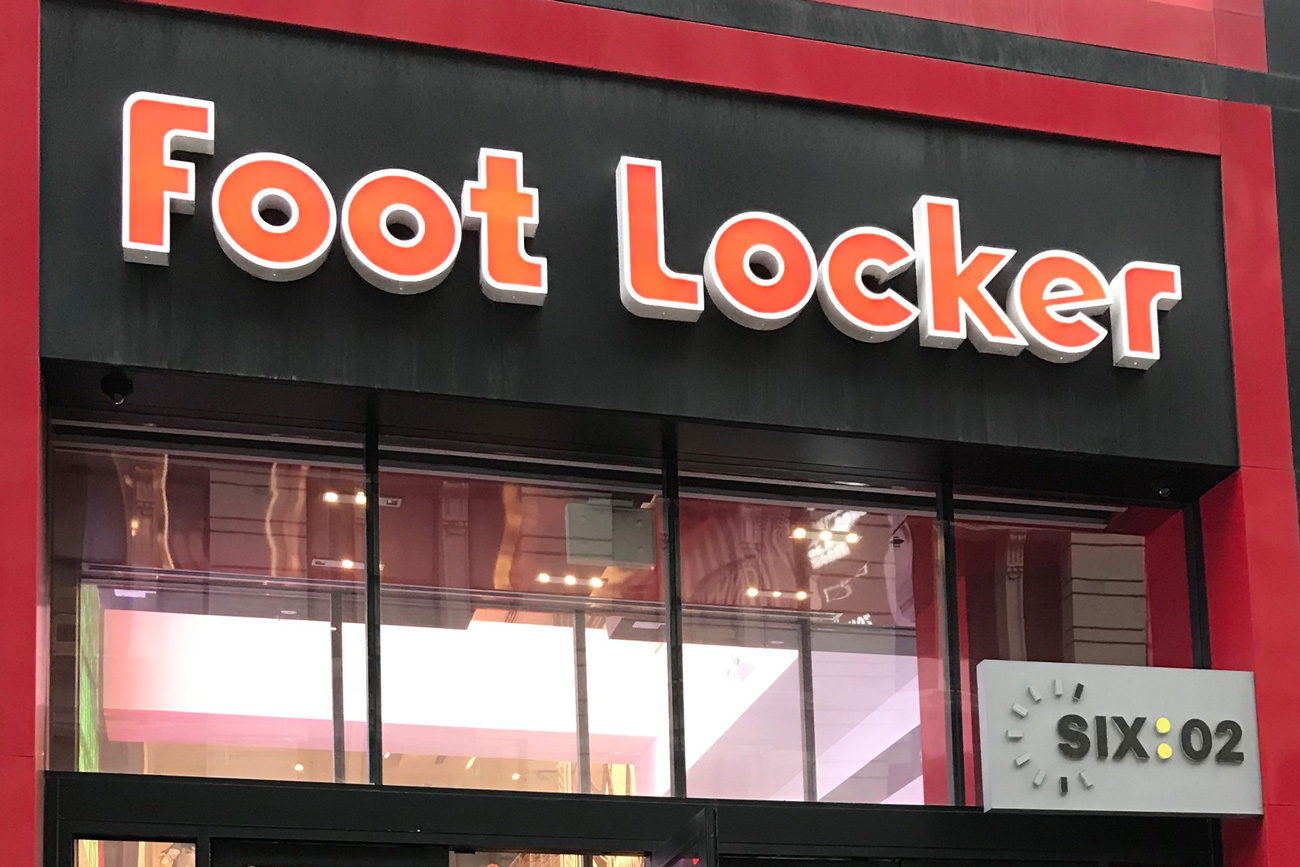
Wall Street circles are cautious about the retailer’s FY20 outlook calling for a low-single-digit comparable sales improvement and continued supply chain investments, citing possible product delivery delays this year fueled by the effects of the coronavirus crisis.
In reporting its first annual sales above the $8 billion mark in FY19 on a 2.2 percent comparable sales increase, FL senior management last week confirmed the completion of a retrofit to its Junction City, KS, facility that supplies stores and processes digital orders, and discussed plans to modernize a Camp Hill, PA, facility to a full-service distribution center to service the eastern U.S.
“The upgraded facility will enable us to fulfill customer orders more rapidly, replenish stores more often, improve the overall customer experience yielding freight and labor savings from an optimized shipping network,” President and CEO Dick Johnson told analysts.
The Foot Locker U.S. banner ended the fiscal year with 2 percent fewer locations at 867, but selling square footage was essentially flat at 2.4 million square feet. Besides testing a new “Core” store format in the U.S. in 2020, FL will open 20 additional “Power” stores in FY20 split between the U.S. and international markets, including one in the American Dream retail entertainment complex at the Meadowlands in New Jersey. Last year, six Power stores debuted.
Despite softer demand in seasonal categories, a compressed holiday season and a promotional environment that pushed period comps down 1.6 percent, Foot Locker said it was encouraged by fourth-quarter momentum in its basketball business from Nike, Jordan, Converse and Puma, and a fifth consecutive quarterly comp sales gain in women’s and kids footwear. The retailer intends to “have more energy around basketball” in the first quarter from both classic and signature styles, including from new category entrant New Balance.