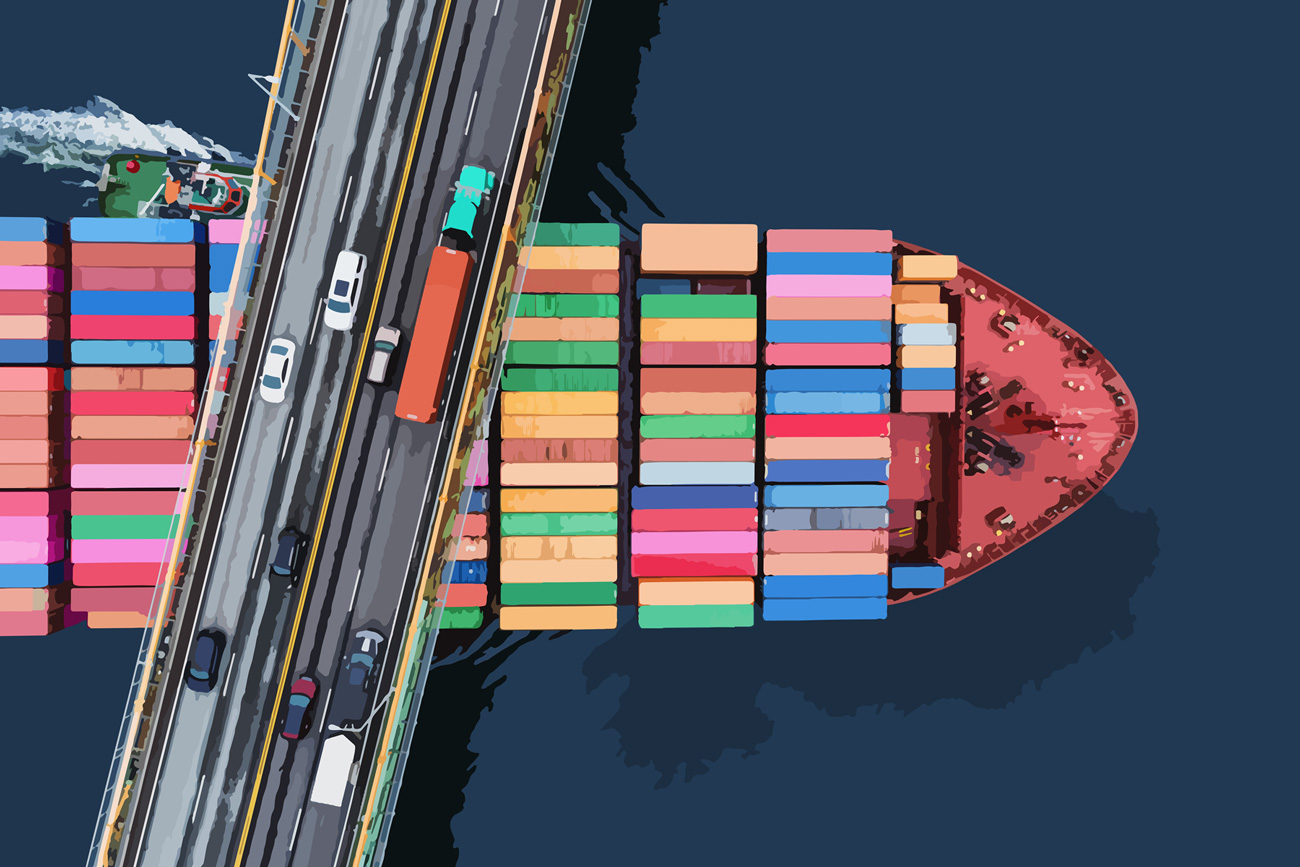
Broken Chain
The team sports market continues to grapple with a fractured supply chain.
Broken Chain
The team sports market continues to grapple with a fractured supply chain.
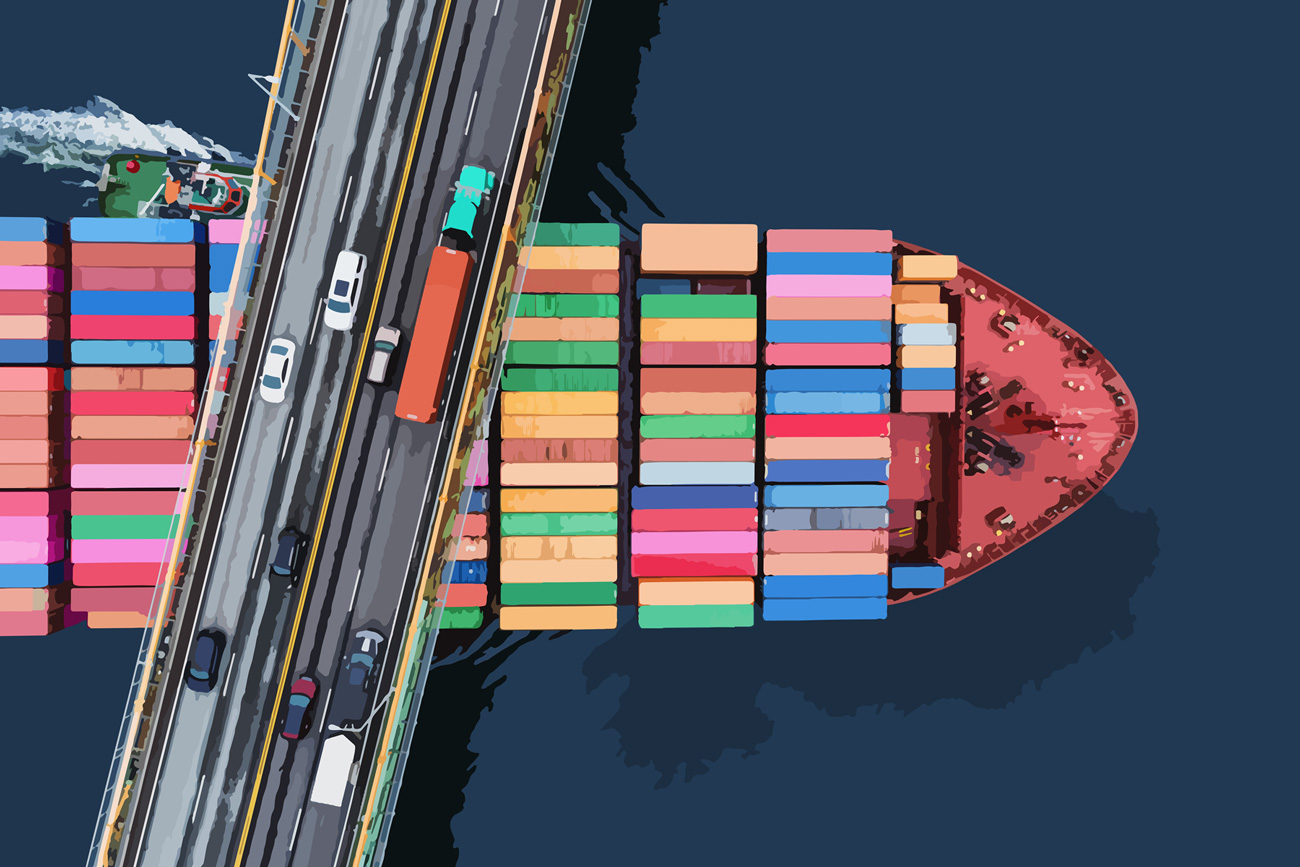
A slow boat to China used to conjure images of the longest trip imaginable, but these days the idiom can be reversed, referring to extensive delays of container ships that are traveling from Asia to U.S. ports, arriving only to sit at anchor sometimes for weeks waiting to be unloaded.
It is a problem with a severe impact on the team sports industry — from raw material sources to manufacturers, from team dealers to their customers. And no one has an easy answer to a challenge that is going to exist well into 2022.
In fact, Insider.com recently reported that U.S. ports moved more than 950,000 containers in August — yet as of early October nearly 500,000 were waiting to be unloaded. The largest cargo ships today can haul 24,000 containers — equal to a freight train 44 miles long. Marine Traffic, a ship tracking website, counted more than 50 container ships outside Long Beach and Los Angeles on October 13 — those two ports handle the bulk of cargo coming from China. On the Eastern coastline, there have also been queues of ships outside Savannah Port in Georgia.
You can do the math.
Although port congestion is far from the only factor contributing to supply chain woes, it’s one of the most visible. The story is familiar to most by now:
• Basically, pandemic lockdowns caused goods to get stuck in some places and overloaded in others.
• Once things opened up there was a surge in demand.
• This was all exacerbated by labor shortages and extreme weather events (such as extensive flooding in China that caused blackouts and factory shutdowns).
• Port congestion plus a lack of warehouse workers and truck drivers are adding to the logistical nightmare.
The bottom line: snarled global supply lines of everything, including sporting goods.
More Headaches on the Way
On the supply side the headaches continue to multiply. For example, a recent surge in COVID-19 cases in Southeast Asia – notably Vietnam and Malaysia, a key production hub for athletic shoes and apparel – has throttled ports and locked down plantations and processers, sparking extended disruptions of raw materials.
Many experts believe the pain will continue well into the second half of 2022 and perhaps into 2023. As Bloomberg.com recently stated, “The system underpinning globalization – production on one side of the planet, connected to consumers on the other by trucks, ships, planes, cranes and forklifts – is too rigid to absorb today’s rolling tremors from COVID-19, or to recover quickly from the jolts to consumer demand or the labor force.”
According to Wall Street research firm BTIG, Nike produced an estimated 350 million pairs of sneakers in Vietnam in 2020 and as many as 160 million pairs may not be made this year because of the shutdowns. In fact, products that normally take about three months to produce in parts of Asia are now taking 12 weeks longer due to backlogs. A few months earlier, COVID-19 outbreaks made India a trouble spot.
Looking ahead, industry experts believe the picture will grow bleaker as the holidays near.
A shortage of raw materials and rising energy costs are impeding already overstressed production capabilities and schedules and longer transit times and soaring transportation costs are testing everyone’s patience, finances and ingenuity.
For example, two years ago, a 40-foot container cost less than $2000 to transport goods from Asia to the U.S. Today, the service fetches as much as $25,000 if an importer pays a premium for on-time delivery, which is a luxury.
So, how does all of this impact the team market?
Manufacturers Struggle To Adjust To Disruption
“The supply chain disruption has affected everyone,” says Zachary Meller, EVP and chief strategy officer at Champion Sports. “During the pandemic, we saw a huge e-commerce boost for fitness products as school, team and institutional sales fell off. When schools reopened, we received a flood of orders so we had to place a lot of reactive orders — about 10 times the amount of orders we typically used to place.”
Throughout the supply chain crisis, “Our prime focus has been to obtain product or stock by any means necessary to service our customer base,” explains Meller. “We hope this reliability will have a long-term halo effect — having product in our warehouse that’s available to our customers in a time of need where product isn’t readily procurable will lead to the strengthening of existing and new relationships in the future.”
On top of everything else going on, Meller is concerned about China’s power grid.
“Different provinces have different power supply limitations, and power to factories has dwindled to three to four days a week – five days max – and the cost of power in China has increased significantly. This also impacts the supply chain,” he notes.
“We’re now looking at more significant price increases going forward,” he adds, pointing out that last year there were shortages of steel, rubber and wood and now plastic, PVC and related materials are in shorter supply and are more expensive, and this is all connected to rising oil prices.
“It’s just a matter of time before everything is affected.”
The result has been volatile product pricing, limited production space and extended production lead times. “The issue also impacts development and R&D for new product, meaning that we have to be focused on securing production space for existing products in our line,” Meller says. “We’re not actively looking at product expansion the way we normally do.”
Meller views the whole situation as being like a flywheel in which everything spins into everything else and there is no fast or easy fix.
“Everything is interconnected and that compounds the problems. I’m not very optimistic in any timeline that targets 12 to 18 months [for a return to normal operations]. That’s very unrealistic,” he says.
In fact, Champion Sports manufactures in nine countries and is seeing a reduced workforce in Europe, but not as bad as in China.
He adds, “We’ll have record demand going into Q4 and then in February we’ll have Chinese New Year, which will back up production lines and manufacturing even more. Couple these issues with Americans buying and consuming at all-time highs in many segments and it’s obvious that supply simply cannot meet demand.”
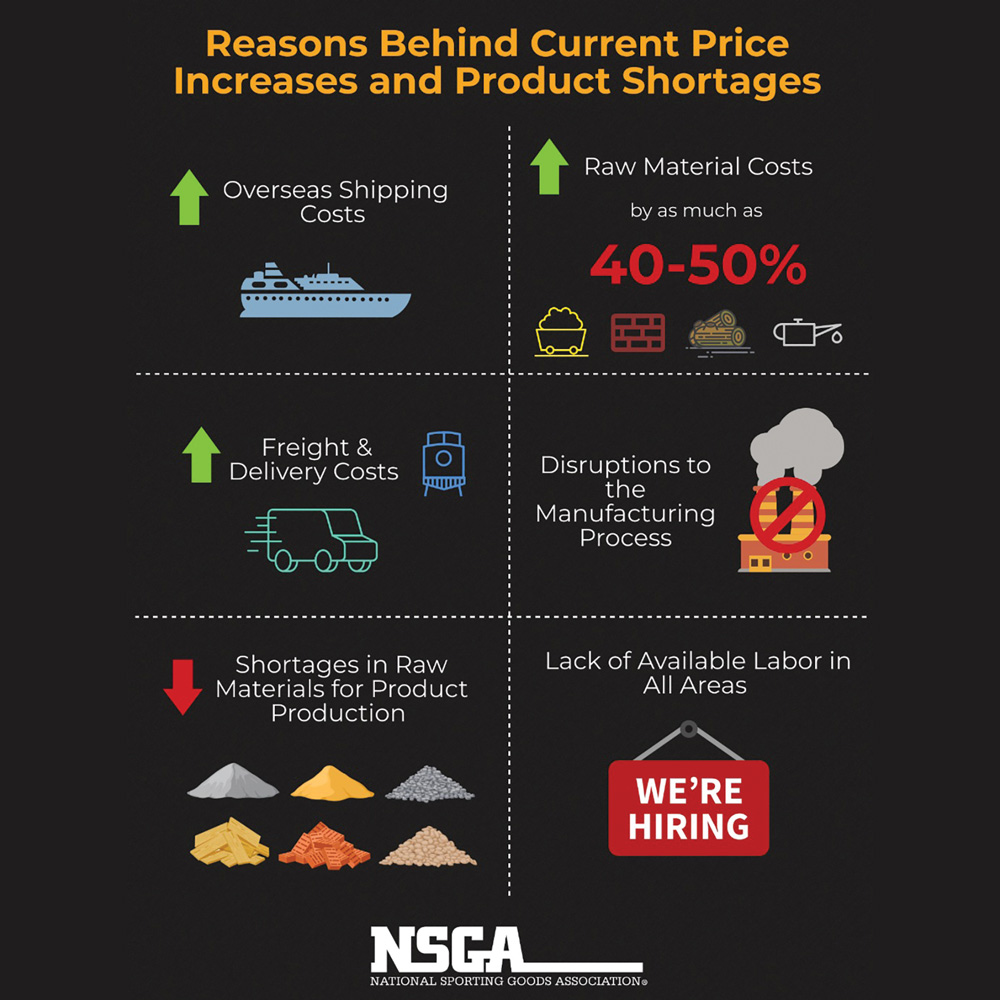
Associations Step In To Help
Sporting goods industry associations are keenly aware of the supply chain issues and are working to provide as much information and assistance to their members as possible, while also reaching out to the federal government to push for solutions.
“The big picture is that the industry is facing a situation that’s hard to overstate and it’s unprecedented in its complexity. The issues we face are deep, broad, long-lasting and far-reaching,” says Tom Cove, president and CEO of the Sports and Fitness Industry Association (SFIA). “Every piece of the supply chain is impacted and we’ve already hit all the levers we can to alleviate the situation. Because each delay is magnified along the line, it will take a while to get through it all.”
Over the years, explains Cove, the sporting goods industry has gotten so good at linking the supply chain that it’s become very lean. Now that’s turned into a disadvantage. “Going forward, it’s obvious that our industry and sports delivery systems have to evolve and respond to consumer demand,” he says. “There may be some lost sales in the near term, but we need to maintain participation surges despite the supply chain issues. There’s a strong, sustained consumer demand for sporting goods products and that’s likely to continue.”
Cove points out that SFIA is actively leveraging its assets and has redoubled its efforts in trying to get tariff relief for sporting goods products.
“We’d like there to be an exclusion or exemption process that will allow our companies to make the case of why they should face lower tariffs,” he says. “We’re working hard to get those programs reinstated through Congress. This will help reduce costs to consumers and supply chains.”
SFIA has also given its board of directors a clear directive to pursue every opportunity to mitigate problems. In regard to Vietnam, “We sent letters to the U.S. President and [the leadership in] Vietnam to make more COVID-19 vaccines available in order to get the country up and running again. This will help Vietnam as well as the sporting goods industry,” Cove says. Too, the organization has endorsed the Ocean Shipping Reform Act of 2021.
Looking ahead, Cove foresees that through Holiday 2021 there will be an “every which way you can” approach, and Q1 of 2022 will be tough. But by Q2, the supply chain crunch should start to ease up.
Two years ago, a 40-foot container cost less than $2000 to transport goods from Asia to the U.S. Today, the service fetches as much as $25,000.
“The next six months will be extremely challenging, but I have faith that American innovation will succeed,” he comments. “Over time there will be more stability throughout the supply chain and we’ll see improvement in fits and starts.”
Like Cove, National Spoting Goods Association (NSGA) president and CEO Matt Carlson is well aware that supply chain issues are impacting the ability of retailers and team dealers to procure a wide range of products. To help improve the situation, the NSGA Management Conference & Team Dealer Summit in September helped facilitate discussions between retailers, dealers and manufacturers, and the organization plans to host further discussions at the Conference next May in Scottsdale, AZ. Along those same lines, NSGA held its virtual “The Sporting Goods Rebound” in May, which is still available on demand at nsga.org/events/the-sporting-goods-rebound.
“NSGA has been providing as much information as possible on the situation regarding supply chain issues and product availability problems and we’re regularly sharing updated information,” says Carlson. “NSGA distributed social media messaging to the public that explained the reasoning for product delays, shortages and price increases related to supply chain problems and NSGA was one of the coalition co-signors of a letter to Congress expressing support for the Ocean Shipping Reform Act of 2021.”
Dealers React to the Reality
On the front lines in team sports, for dealers the supply chain crisis has proven to be a huge challenge among many other COVID-inspired challenges.
“I can see the container ships from my window,” exclaims Aaron Karsh, director of operations for Harbor City, CA-based California Pro Sports. “It’s a challenge — stuff that’s never been out of stock before is now unavailable. Most of the time, customers are understanding, but their impatience is growing.”
To help alleviate aggravation, “We’re trying to look at stock live as we’re taking an order to avoid problems,” says Karsh. “When meeting with coaches and athletic directors, we often have to substitute brands, items and price points.”
But this is impossible to do with online orders, he points out, which ends up doubling or tripling the workload for an already overtaxed staff.
Regarding uniform printing and production, Karsh notes that inventory issues and product availability are pushing things back. “Do we fulfill part of an order and then do the remainder when the missing pieces come in, or do we hold the entire order until it’s complete? Incomplete or late orders are now commonplace,” he says.
Karsh is optimistic that by Spring/Summer 2022 the situation will begin to improve, but this ultimately depends on the workforce and manufacturers’ ability to produce the needed items.
“If manufacturers were unable to produce or sell items from previous seasons, will they have the needed cash flow to produce enough inventory going forward?” he wonders. “The ripple effect is starting to grow. I wish that our legislature and elected officials would work together to find solutions rather than squabble with each other. This affects the majority of the country.”
At Hoosier Sporting Goods in Columbus, IN, owner Michael Bodart reminisces about the good old days when vendors had warehouses full of product, there were no shipping delays and orders would arrive in one day.
“Now we have to mix and match styles and we’ve pushed our turnaround time to two weeks or so,” he says, pointing out that its hoodie supply won’t last much past November, trophy parts are in sporadic supply and heat film for printing is hard to come by.
“We can’t turn orders around as fast as we want to and we’ve switched some of our priority to digital transfers, especially for smaller orders,” he explains.
When it comes to shipping costs, says Bodart, “We try to make sure we don’t order from a vendor that offers free freight unless we meet the minimum freight requirements, otherwise we could end up paying for multiple shipments that originate from different warehouses.”
He sighs, “I just wish they’d unload the boats quicker.”
On the East Coast, Betsy Frey, owner of Holyoke Sporting Goods in Holyoke, MA, admits that the supply chain predicament has had a big impact on her business.
“It’s been terrible. We couldn’t get soccer cleats, football pants or football cleats. You don’t know day to day what you can get,” she says.
While shipping costs have gone up a little, she says the main problem is delays: “We’re having a terrible time with missed shipments and there are more mistakes and mis-shipments in orders. Companies are short-handed and they’re trying to get product out as quickly as they can.”
As a result, Frey has found that her customers are becoming used to getting what’s available instead of what they really want.
“We’ve had to be creative to get around problems,” she explains. “You have to find what’s in stock and if something isn’t available we try to substitute items that are better to keep customers happy. It’s easier to substitute a higher-quality product for what was originally ordered.
“We may not make as much money on the order, but we can fill it and be done with it rather than stretching things out for two months,” Frey adds.
“The days of getting things overnight are gone. Once we make it through the Christmas rush, maybe things will settle down a little, perhaps by February 2022. Everyone just has to have patience.”