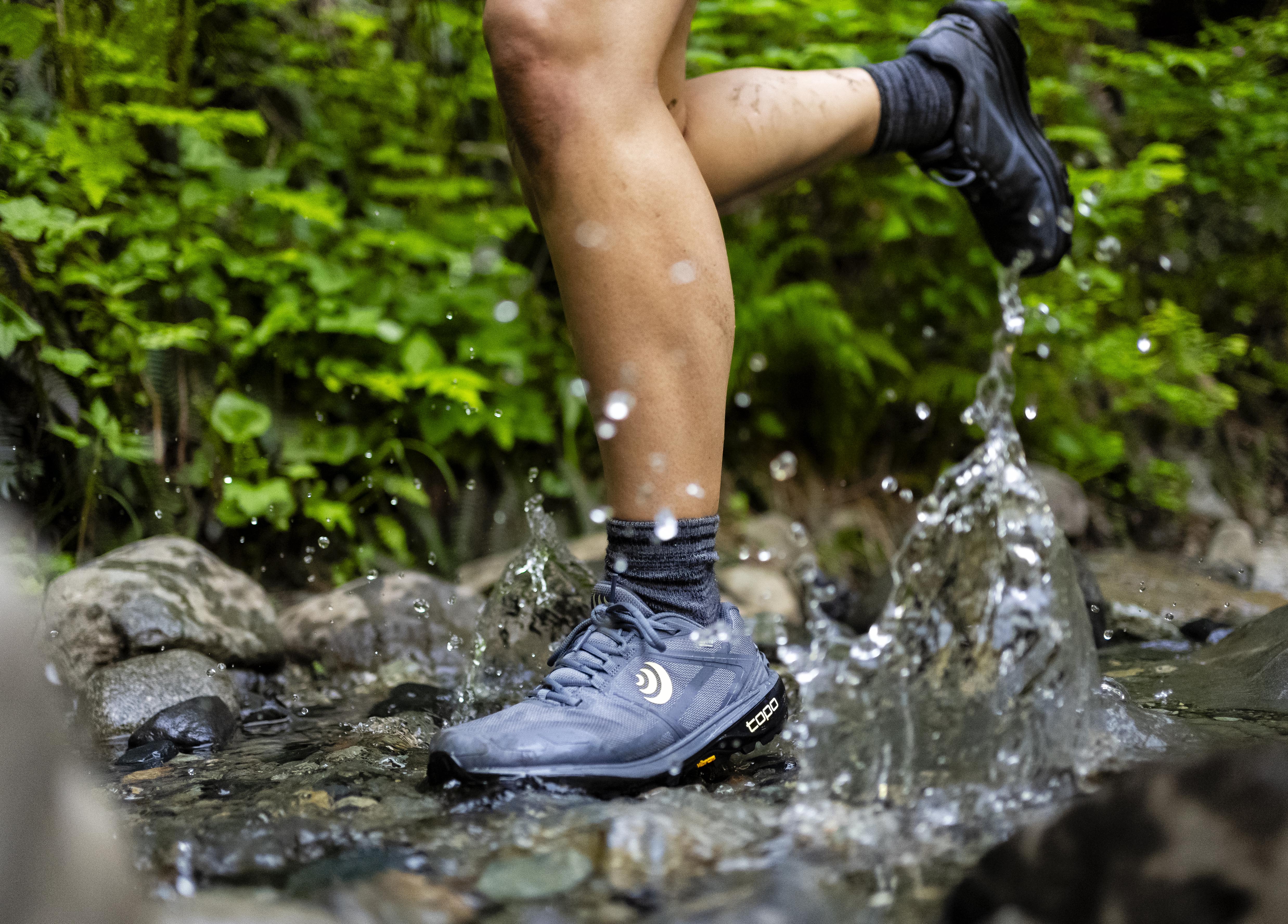
According to Accenture’s Accelerating Global Companies toward Net Zero by 2050 report, many companies are not on track to meet net zero goals by 2050 and need to accelerate. The report concludes that “reaching net zero will require urgent and profound transformations, as it is about embedding sustainability into everything organizations do, redefining their purpose, culture and business models.”
Companies have made strides in sustainable solutions in footwear for years, however, the race to mitigate PFAS in shoes (and softgoods) is one challenge that is heating up significantly as more laws regarding PFAS have gone into effect across the nation. Just last month California and New York passed legislation, effective January 1, 2025, restricting the use of PFAS in athletic footwear and other textiles. According to Safer States, a national alliance of environmental health organizations, at least 36 states are considering more than 450 bills on toxic chemical-related policies. Approximately a dozen states have already outlawed products with PFAS.
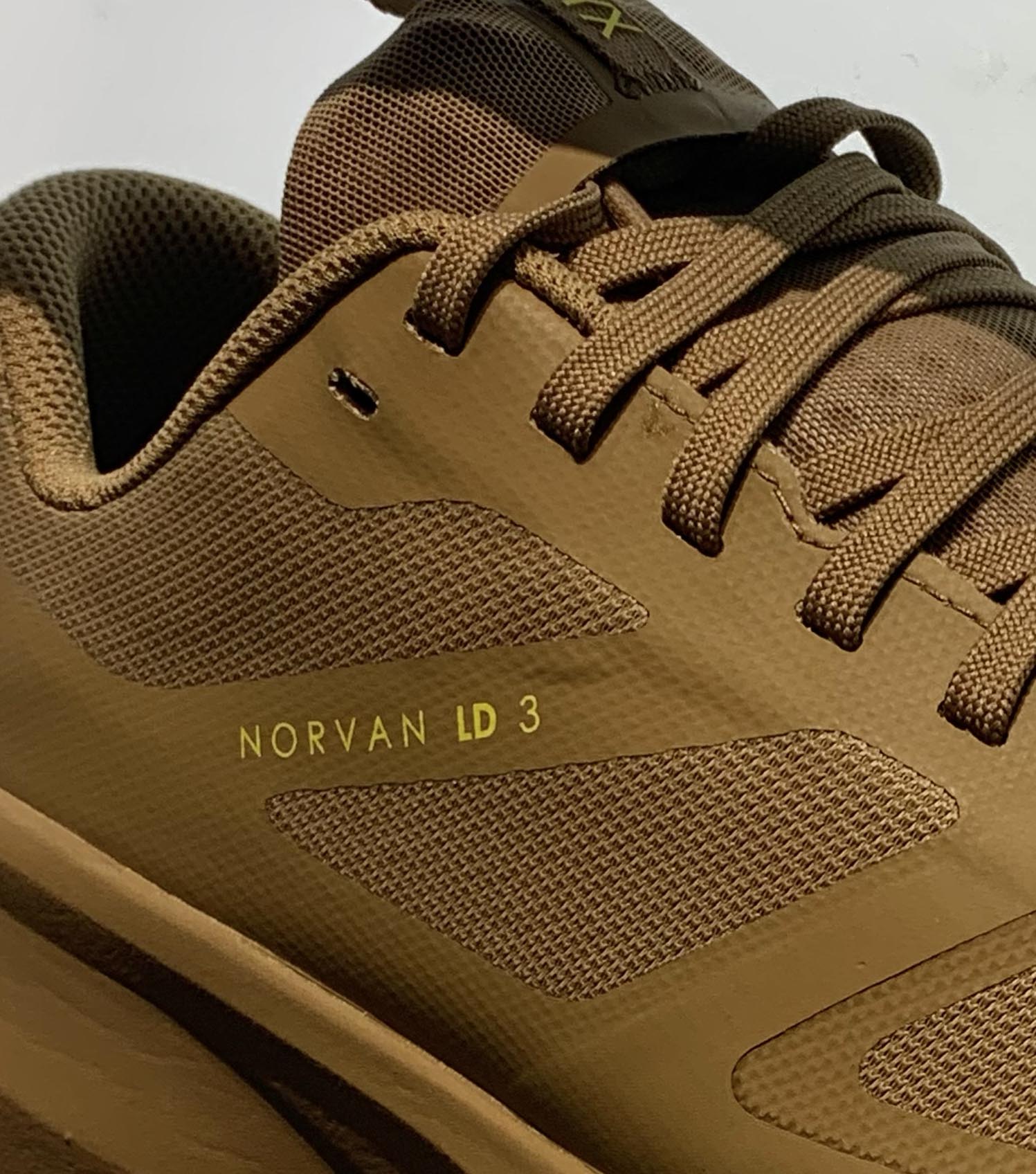
PFAS are a group of synthetic chemicals used in many consumer products. Toxicity and longevity go hand in hand with PFAS, commonly referred to as “forever chemicals” because they are difficult to break down in the environment. PFAS has long been key to waterproof performance in footwear, as well as fabric treatments and finishes for several decades.
“People have known for years that ‘forever chemicals’ are harmful for the environment and need to be addressed, and now legislation is pushing the timeline for that agenda,” states Mark Mathews, VP sales at Scarpa. He explains that Scarpa, a long-time brand partner with W.L. Gore, has been actively working for the last 18 months toward transitioning its current Gore-Tex application to a new Gore-Tex technology. Called ePE, the new expanded Polyethylene (ePE) membrane, free of PFAS chemicals, is light, thin yet strong and has a reduced carbon footprint. All Scarpa run, hike and trail footwear will feature Gore-Tex ePE in 2025.
“We were PFAS-free compliant as of January first,” explains Mathews.
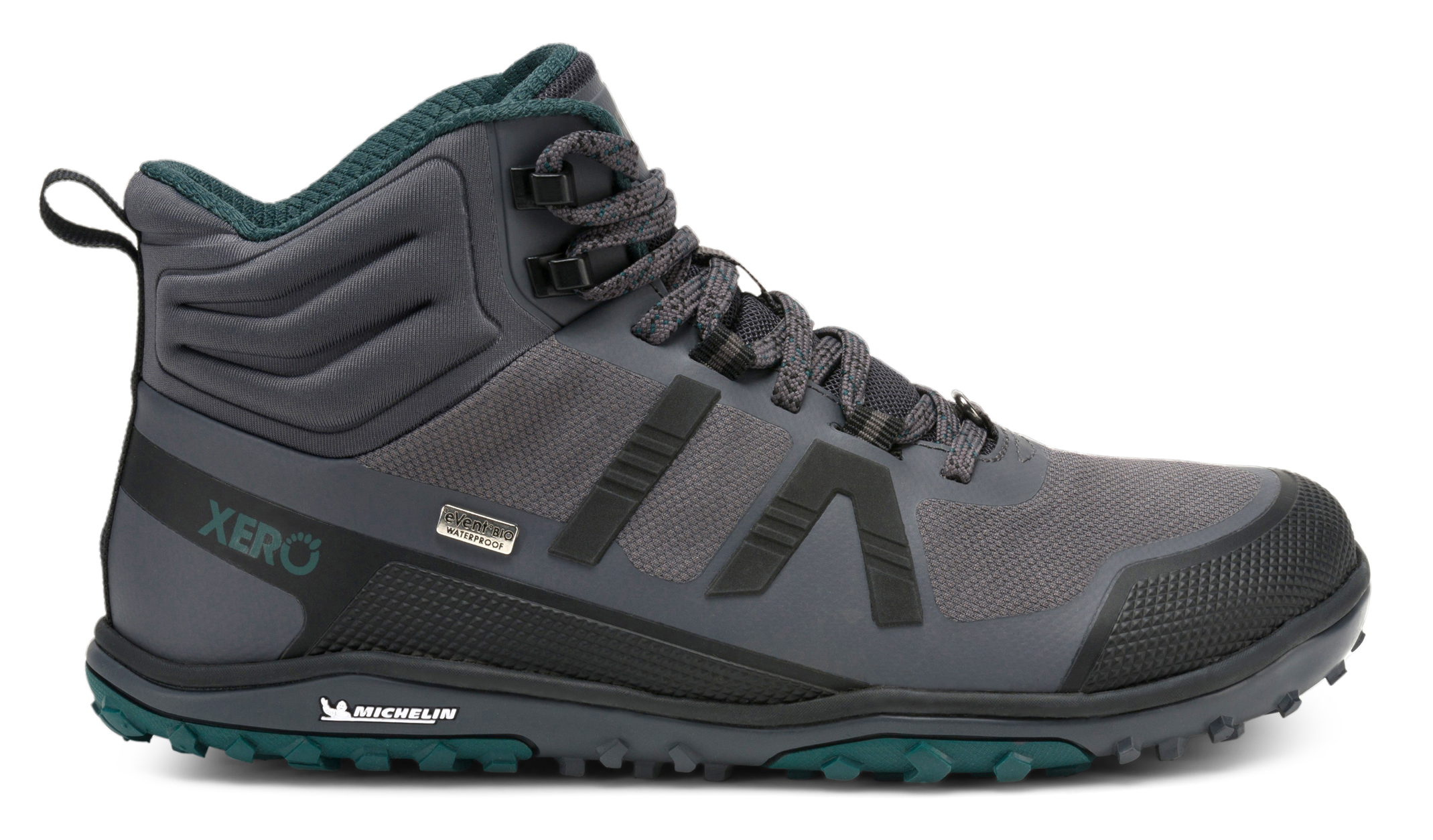
The current market forces in the marketplace have varying levels of influence but together contribute to ongoing shifts in footwear trends. Chad Kelly, eVent fabrics president, explains, “Regulations are a strong focus not only because you have to comply, but in footwear, waterproof performance is critical, and sustainability is increasingly important.” He adds that corporate initiatives and a desire to produce cleaner product is also top of the list. eVent fabrics portfolio includes eVent StormST, formerly eVentBIO, a plant-based membrane technology that uses sustainable materials to provide all-weather protection and performance.
Materials solution provider Polartec has eliminated PFAS in its DWR (durable water repellent) treatments across its line of performance fabrics. Polartec Power Shield Pro is a weather protection fabric that is made from renewable, non-GMO, plant-based nylon and a non-PFAS membrane. There is no loss of performance from a water repellency or durability standpoint, according to the company.
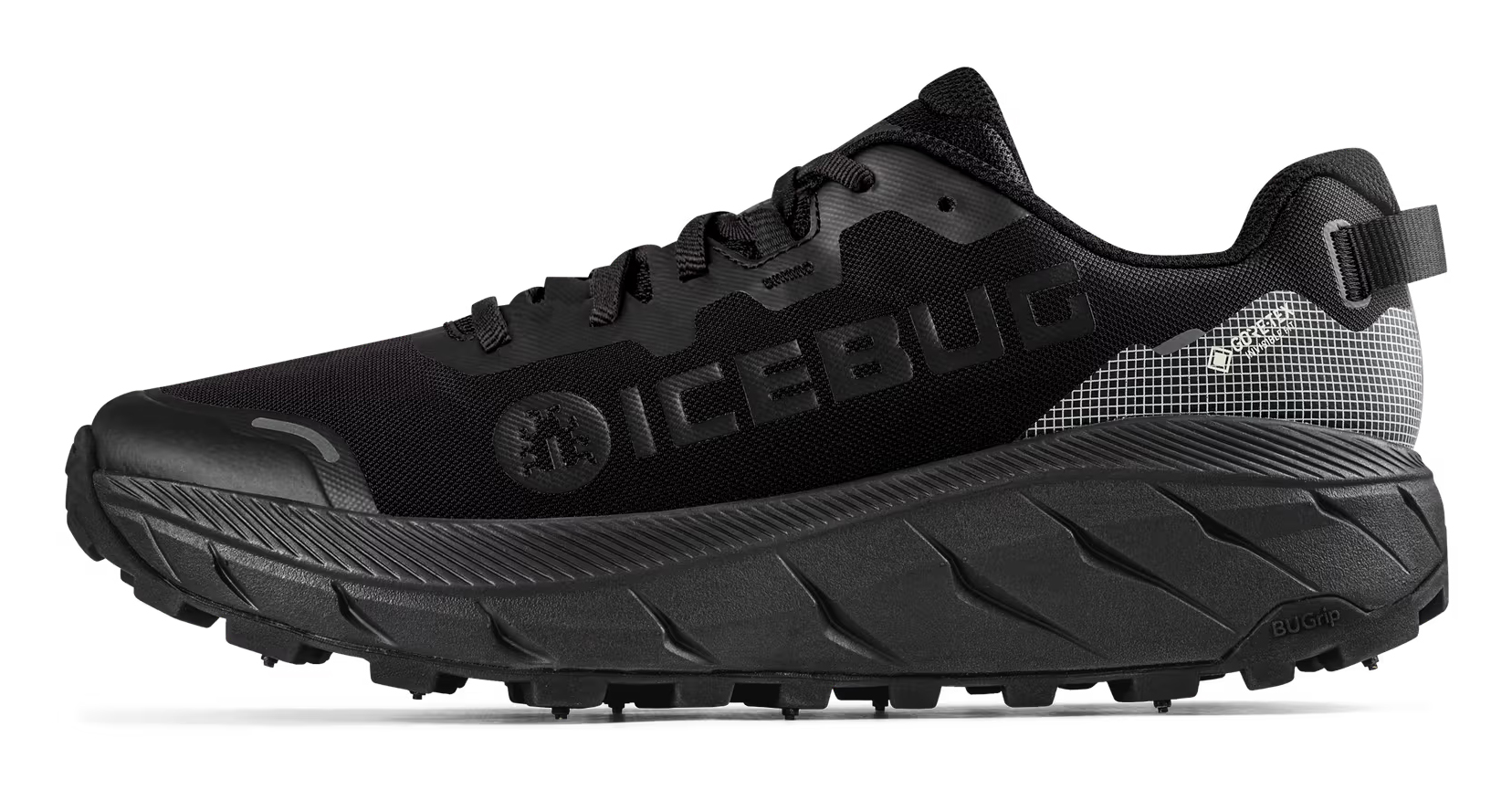
Challenging but Necessary Change
Durability and manufacturing ability are major hurdles brands face when phasing out conventional tech and integrating modern eco alternatives. Footwear brings its own list of issues; Construction is complicated, there are different materials and different processes involved as well as long lead times and the need for performance that can stand up to harsh terrain and extreme weather conditions.
Cirql, a subsidiary of OrthoLite, recently introduced Cirql Zero, an industrially compostable, biodegradable foam innovation. “Footwear brands have been searching for a trusted, fully biodegradable midsole material for many years; it’s the last piece of the puzzle,” explains Matt Thwaites, VP/ General Manager of Cirql. “The midsole has always been a challenge because brands need the performance properties to go with the compostability of a biodegradable midsole.”
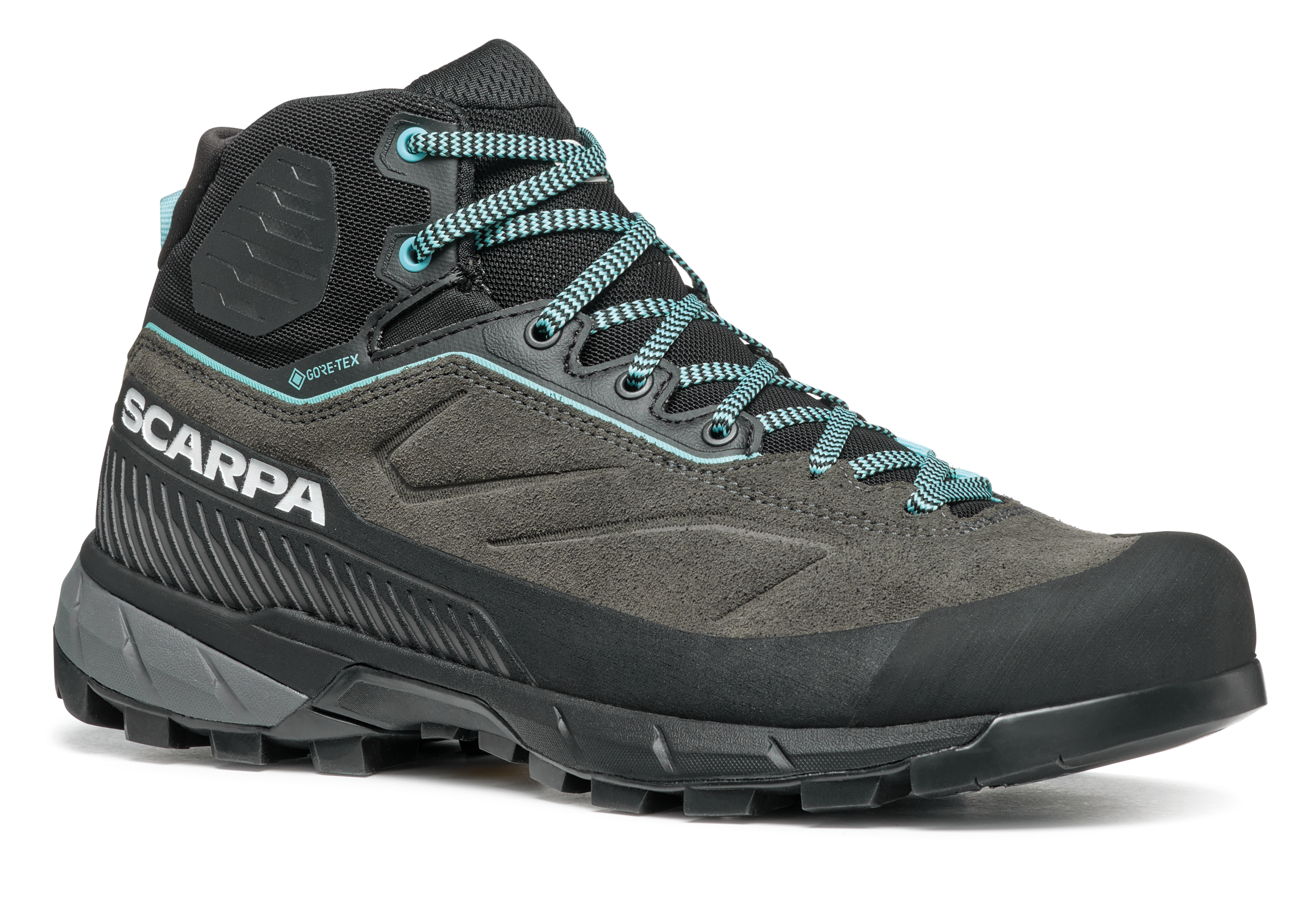
Cirql Zero features manufacturing versatility. According to the company, the midsole foam can be produced using supercritical foaming (SCF) technology in an autoclave process. This flexibility ensures that Cirql Zero is accessible to a broad range of manufacturers, streamlining its integration into existing production processes.
Beyond material concerns, another challenge is consumer engagement. At a recent visit to the Arc’teryx Alpha retail store in New York City, textile savvy sales associates noted that their customers are keen on the Norvan LD 3 light hiker, but not because of its ePE Gore-Tex membrane technology. I was told the shoe sells best based on its style and functionality and because it’s an Arc’teryx product. When I asked about it being PFAS-free and how that impacts consumer decision-making, I was told, “basically, consumers don’t care.”
This isn’t surprising. “The industry is driving the PFAS-free trend, not the consumer,” shared Kelly. “And that’s okay; the industry needs to fuel innovation and change.”
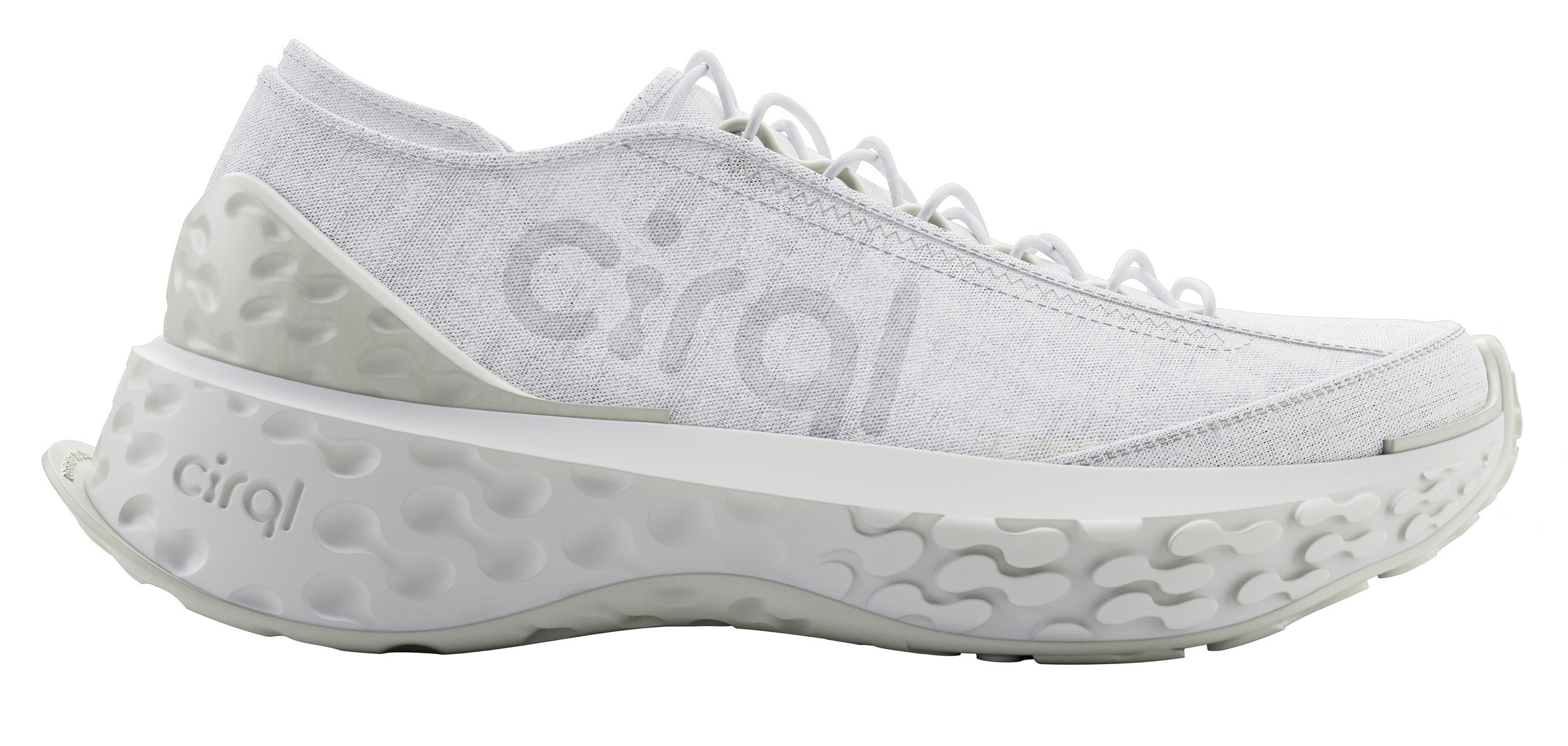