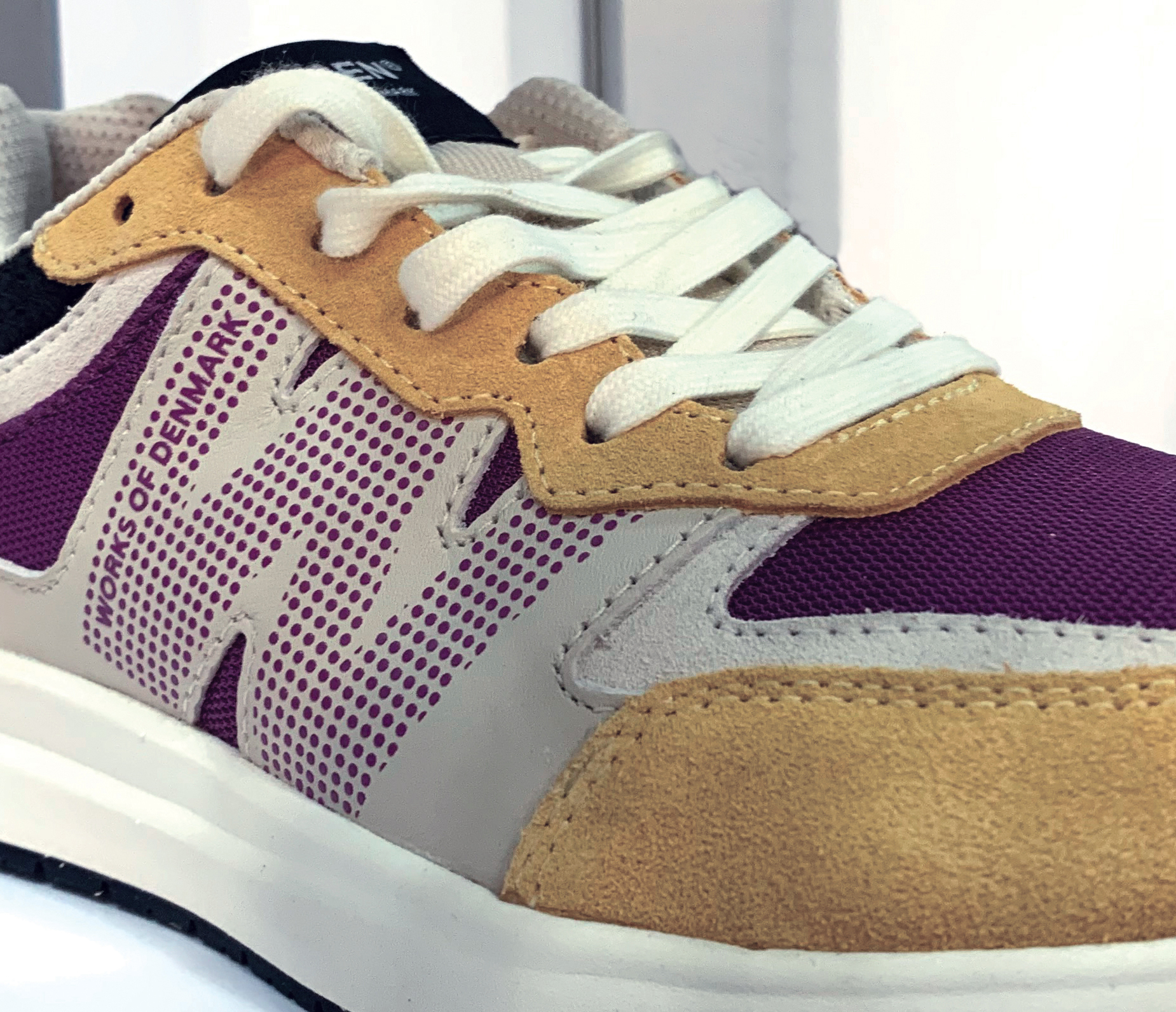
Decarbonizing footwear is no easy task. According to oft-quoted statistics, more than 20 billion shoes are made every year, using a manufacturing process that releases large amounts of carbon dioxide, declared to be responsible for 1.4 percent of global GHG emissions. Additionally, in the U.S., over 300 million pairs of shoes are discarded annually, 95 percent of which end up in landfills.
“Sustainably produced shoes should embody circularity and durability, facilitating the ability to reuse, repair, remanufacture and recycle. They should be manufactured with a focus on reducing their overall carbon footprint, using no hazardous chemicals and avoiding the release of harmful chemicals and microplastics during use,” explains Nina Conrad, a sustainability consultant for footwear. Conrad notes that, “a functional shoe today typically consists of more than 40 components, making the selection and sensible combination of sustainable components yet another hurdle.”
Strides in Next Gen Materials
It’s no secret that adoption of environmentally responsible, ethically-sourced performance-driven materials are key to a sustainable future for footwear. The Material Innovation Initiative (MII) 2023 State of the Industry Report: Next Gen Materials, shines a light on the opportunities and challenges of this emerging marketplace.
Of the material innovators listed in the recently-released MII Report, new plant-based alternative leathers dominate product offerings. Of the 137 companies represented, 52.9 percent use plant derived materials as the main input; 13.6 percent use microbe derived materials; 11.4 percent are blends; 10 percent use recycled material; 7.9 percent use mycelium; and 4.3 percent use cultivated animal cells.
“Getting from prototype to pilot launch can be long and expensive,” commented MII co-founder and CEO, Nicole Rawling. “Consumers have been hearing about these cool new materials but not seeing them in the marketplace, which has slowed acceptance and some investment numbers.” However, according to MII’s Brand Engagement Survey, partnerships between industry brands and material innovators continued to accelerate in 2023. While that bodes well going forward, Rawling believes more investment is strongly needed, from both private investors and government, in order to research, develop and scale next-gen materials.
Carbon Tech & Circular Systems Come of Age
Footwear maker, ON, has introduced CleanCloud, a new high-performance foam for running shoes created by using carbon emissions as a raw material. The launch is a collaborative effort with LanzaTech and Borealis, companies specializing in advanced, circular solutions.
This is the process: LanzaTech captures carbon emissions before they enter the atmosphere. A fermentation process converts the emissions into liquid ethanol. The ethanol is dehydrated to become ethylene gas, which is polymerized by Borealis to create EVA pellets. ON uses this next-gen EVA to engineer the foam cushioning for CleanCloud footwear.
VivoBarefoot has taken an alternative approach to footwear production with its new VivoBiome made-to-order 3D printed shoes. VivoBarefoot is now partnering with material science company Balena to expand this concept to commercialize fully compostable 3D printed footwear by 2025, featuring the development of BioCir flex, a bio-based, recyclable, industrially compostable thermoplastic.
Here are more examples of footwear made to step lightly:
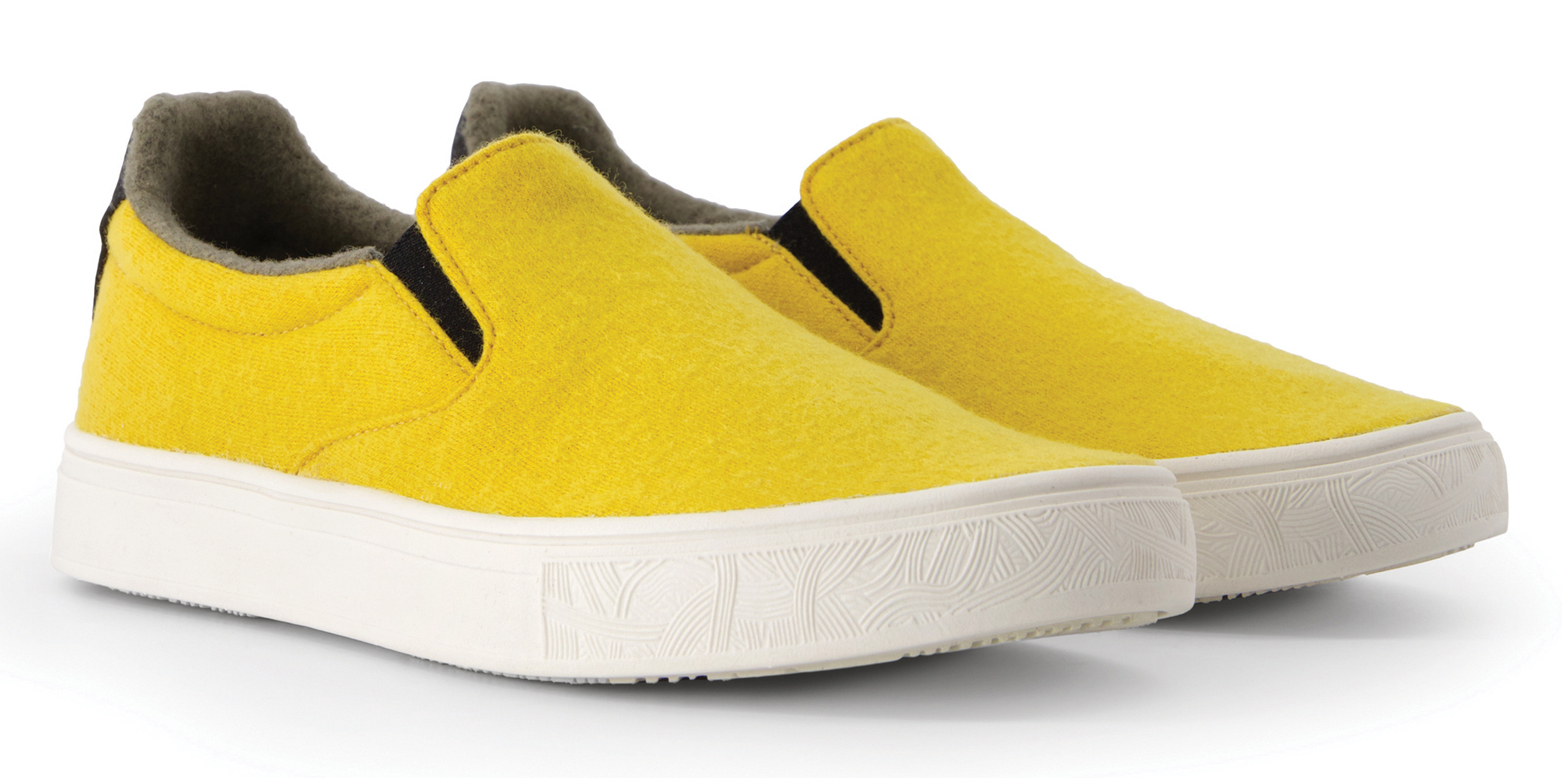
YY Nation: New Zealand based YY Nation is a Zero Carbon Certified brand by Ekos, meaning that CO2 emissions released by its shoes are balanced by removing an equivalent amount of CO2. The brand’s commitment to circularity minimizing waste via a comprehensive renew, reuse approach includes footwear takeback initiatives that extend to shoe boxes that are designed to be repurposed as shipping boxes and using sole offcuts in flooring. Merino wool, bamboo and cactus are featured in current collections.
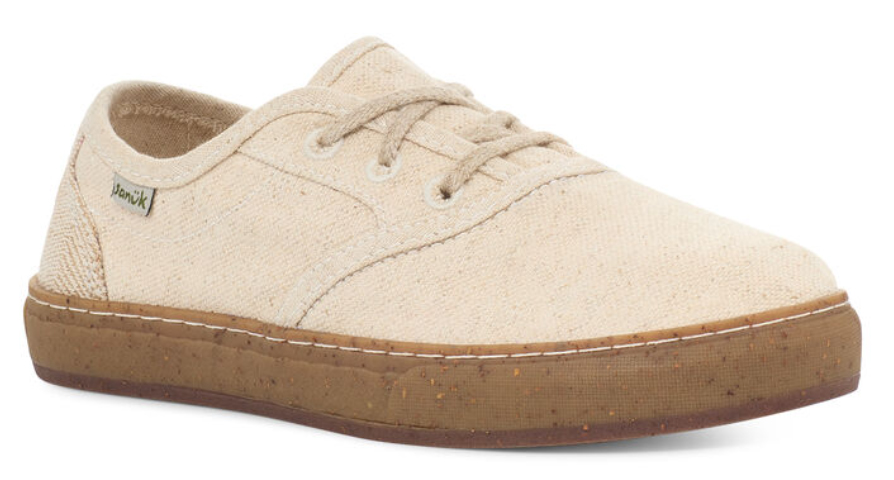
Sanuk: Winner of Good Housekeeping’s 2024 Sustainable Innovation Awards, Veg Out is a 100 percent plant-based footwear collection that includes Sidewalk Surfer styles made entirely from responsibly-sourced cotton, hemp, jute, Tencel lyocell, natural rubber, cork and recycled PLA (corn-based fiber). The use of undyed fibers was an intentional decision to further reduce environmental impact, compared to conventional fabric dyeing and finishing processes.
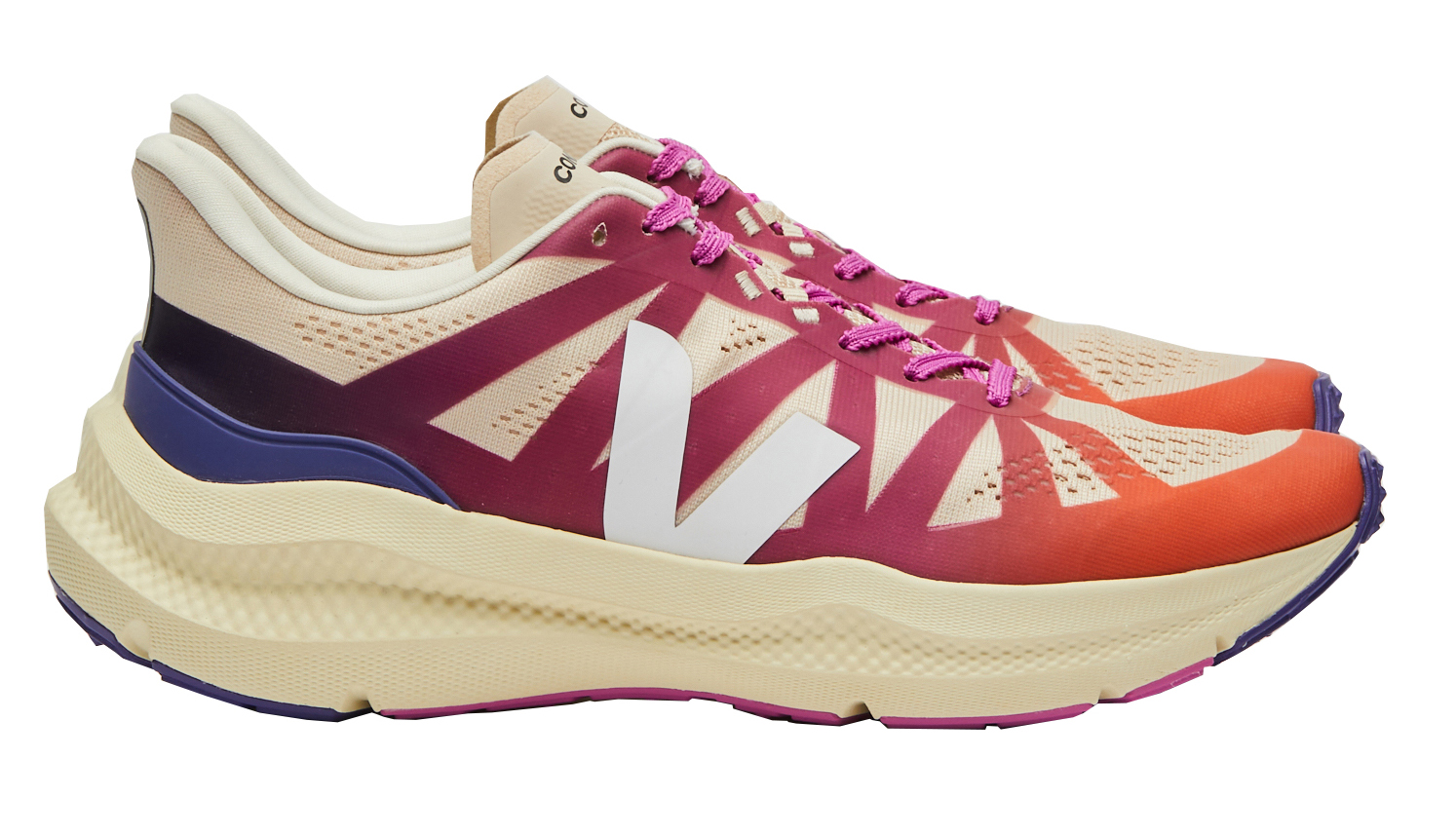
Veja: The new, advanced Condor 3 running shoe is made from bio-based and recycled materials including ricinus oil (castor oil), sugar cane, Amazonian rubber, natural latex from Brazil and recycled polyester. The company’s Beyond Petroleum Project defines its eco-forward approach in all aspects of business from material sourcing to social responsibility, and recycling and upcycling all efforted by the brands mission to reduce dependence on plastics.
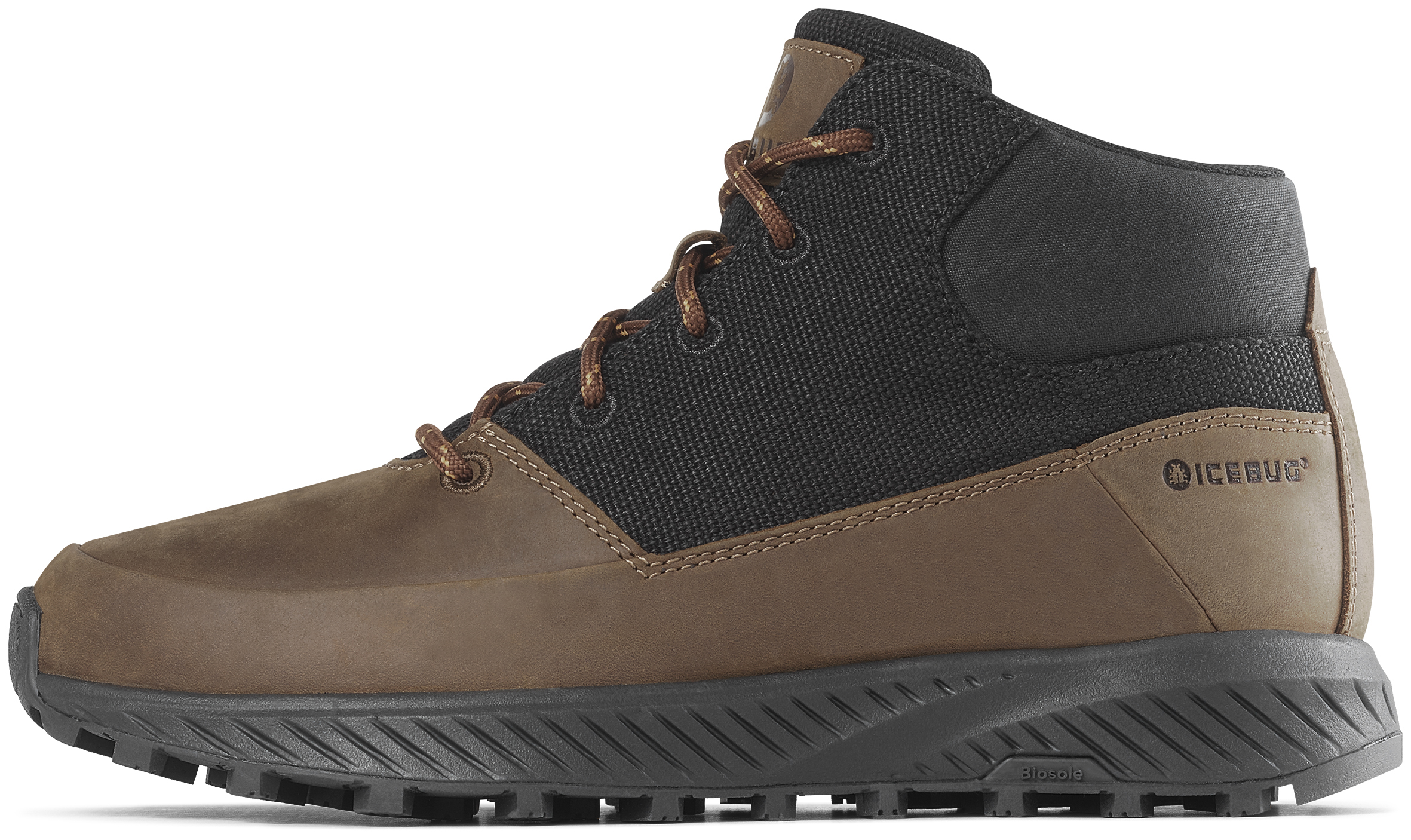
Icebug: Swedish brand Icebug is founded on minimizing chemical usage, buying sustainably grown natural rubber that does not lead to rainforest deforestation and contributing to good worker conditions in the factories making Icebug shoes. Helping factories switch to solar energy is another priority, with the goal of saving 5,000 tons of carbon dioxide annually. The Larvik Hemp Biosole, designed for everyday activities and light hiking, has a calculated carbon footprint of just 12 kg CO2 eqv. per pair.
Woden: The fish leather used in all Woden sneakers is a waste product from the Icelandic fishing and food industry; only one percent of the skin is actually used, the rest destroyed. The fish skin is hard-wearing and sustainable due to the unique cross-fiber structure that is considerably stronger than calf leather. Woden, based in Denmark, uses an eco-friendly treatment and tanning process at a factory in Iceland that produces zero carbon emissions.