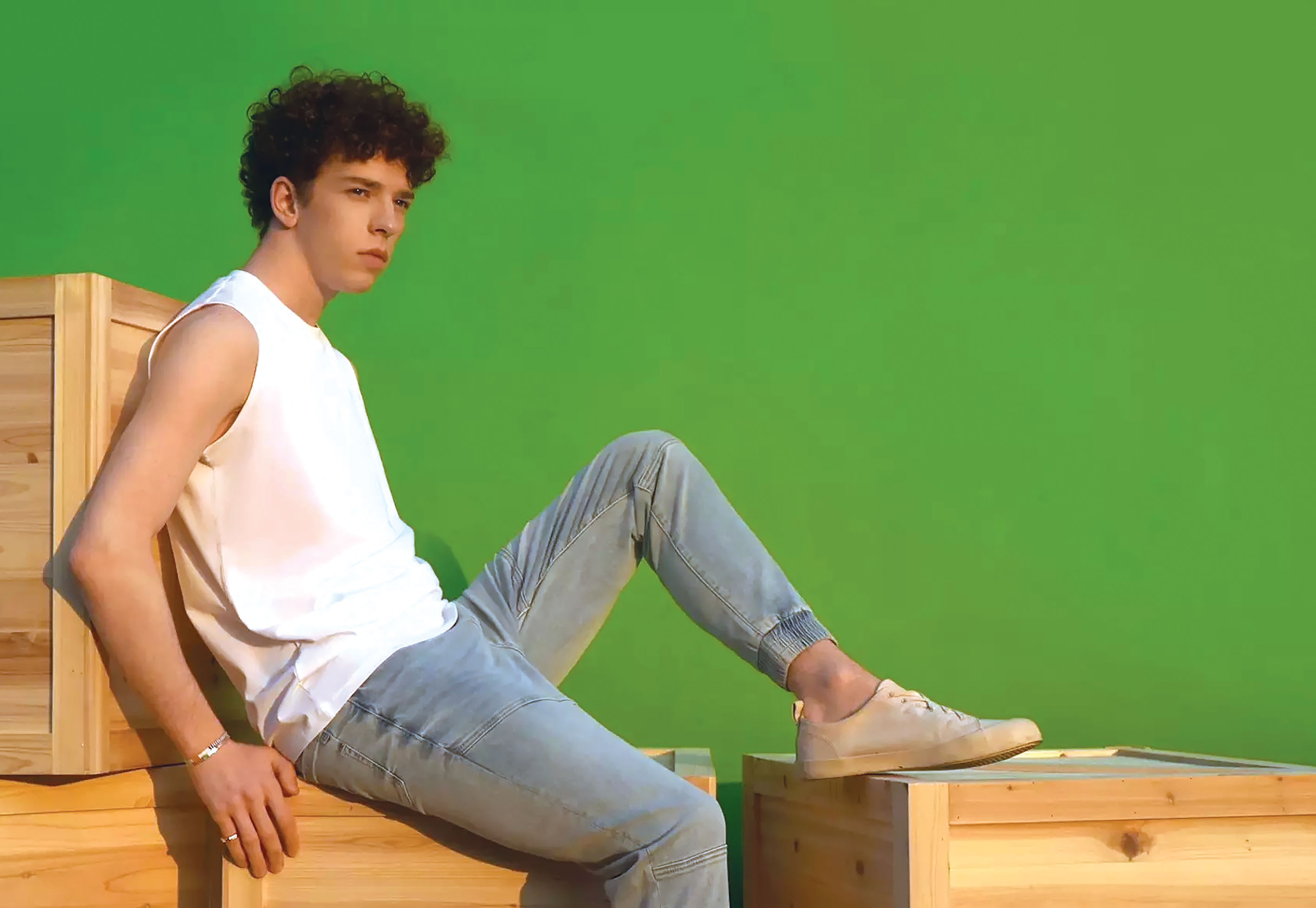
It’s difficult to imagine getting dressed in the morning without putting on something that stretches. Stretch fibers – spandex (elastane) and other elastomeric synthetics – impart comfort and performance to both knitted and woven garments.
Persistence Market Research anticipates that the global market for spandex will reach $20.19B U.S. in value by 2033.
Sadly, there’s a downside to our love affair with stretch. Most polyurethane-based spandex fibers utilize a toxic solvent in the spinning process. Once spandex fibers have been heat-set in blended fabrics, they are extremely difficult to separate from other fibers for recycling. And like other synthetics, spandex sheds microfibers.
“Spandex is a conundrum,” says Simon Whitmarsh-Knight, global sustainability director/textiles for the Hyosung Corporation, makers of CREORA spandex. “Comfort is the most important quality to consumers.”
Spandex producers are working to create more sustainable products, including spandex made from pre-consumer waste, bio-based spandex derived from renewables, and spandex fibers with improved performance and longevity.
Sustainable Stretch Starts with Inputs
The LYCRA Company’s Planet Agenda was initiated in 2008. Its product vision includes using renewable or recycled resources as inputs, and ensuring those products are recyclable at end of life and durable during wear, with de-carbonization a key goal in alignment with Science Based Target initiatives (SBTi) for 2030.
Launched in 2019, LYCRA EcoMade contains 20 percent pre-consumer spandex waste, which is blended with virgin polymer to achieve the same performance as original LYCRA fiber. “The majority of our carbon impact is in ingredients,” explains Jean Hegedus, director of sustainability. However, “Our goal is to make as little waste as possible,” she continues, which limits the scalability of fiber made from pre-consumer waste.
LYCRA T400 EcoMade is an updated version of the company’s elasterell-P bicomponent stretch fiber, using bottle-based rPET and bio-derived inputs from dent corn. There are two versions: 50 percent rPET with 18 percent bio-derived inputs; and 60 percent rPET with 15 percent bio-derived inputs.
While LYCRA T400 fiber is a go-to in the stretch denim market, LYCRA FiT400 technology is engineered for knits. It’s an EcoMade product.
Preliminary testing finds it recyclable via glycolysis in fabric blends with standard PET.
“Our goal is to develop a LYCRA fiber that you can easily extract and then re-spin into new fiber. We are working with select recyclers under NDAs,” says Hegedus. The T400 recycled products are certified under the Global Recycled Standard (GRS). The LYCRA fibers are certified under the Recycled Content Standard (RCS).
Fibers with LYCRA lastingFIT technology (aka LYCRA XTRA LIFE) resist damage from sun, heat, chlorine, and industrial laundering. Known for its performance in swimwear, it’s gaining interest in the workwear arena.
The Race to Bio-Based
Bio-based inputs help mitigate the CO2e of spandex fibers. The LYCRA Company is collaborating with Qore LLC, a joint venture of Cargill and HELM AG, to use Qore’s QIRA bio-based 1,4-butanediol (BDO) made from rain-fed dent corn in the next generation of LYCRA spandex.
Qore’s new 65 kiloton, 88 percent wind-powered plant in Iowa should be operational in December of 2024, making it possible for LYCRA to produce spandex using 70 percent bio-derived ingredients. A preliminary LCA indicates a 44 percent reduction in the product’s CO2e..
“We’re very excited,” says Hegedus. “By early next year hope to convert a third of LYCRA fiber production. The stretch and recovery parameters are equivalent, so the fiber is essentially a drop-in. While the initial product will have 70 percent bio-derived content, our long-term plan is to get as close to 100 percent bio-derived or sustainable content as possible.”
In 2021 Hyosung became the first spandex producer to begin large-scale commercialization of USDA and SGS-certified regen bio-based spandex made with 30 percent renewable resources. The company has plans to offer versions of the product with 70 percent and 98 percent renewable inputs. Hyosung partners with Covation Biomaterials to use their Susterra propanediol (PDO), derived from sustainable corn farming in the United States.
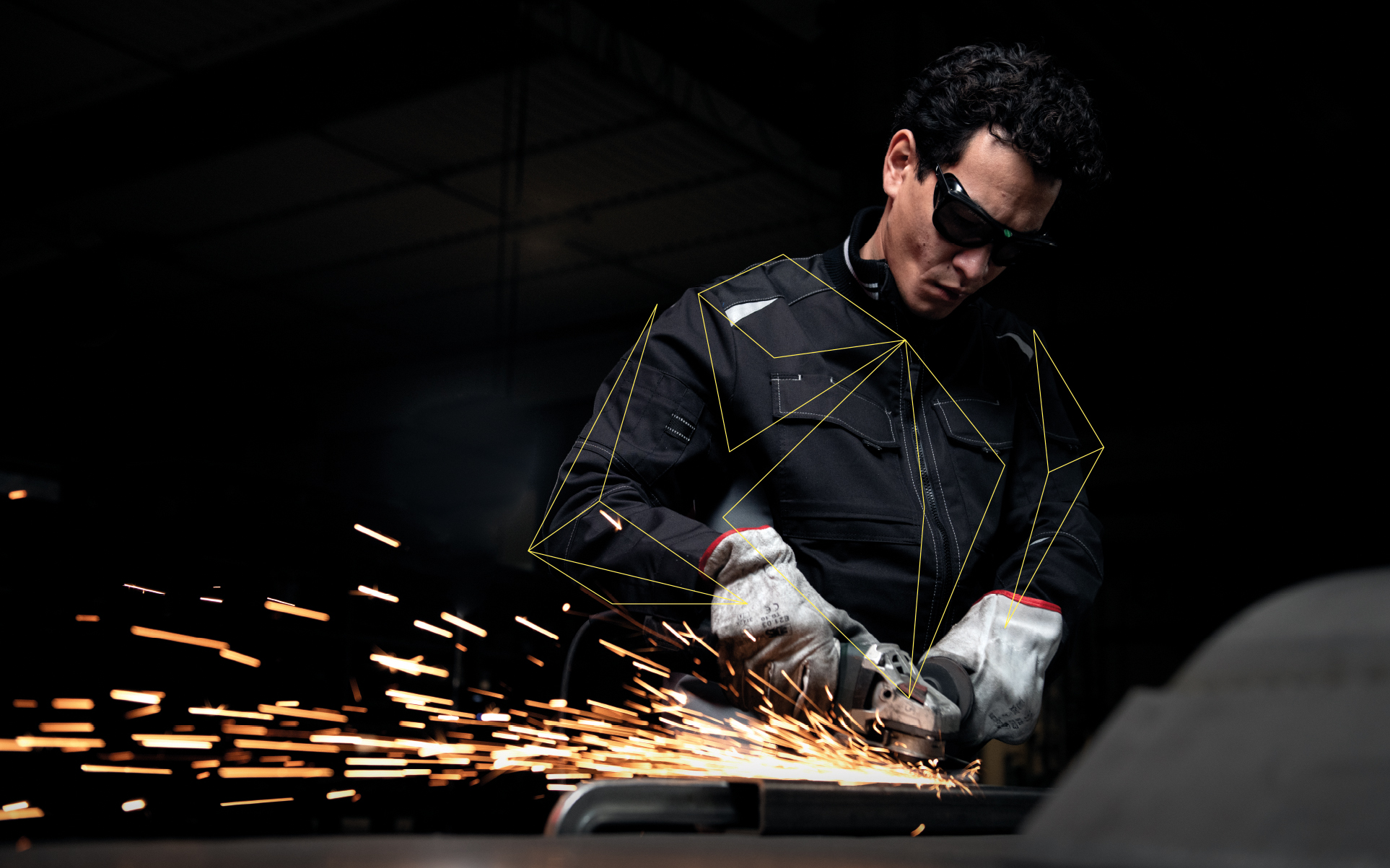
Creating a Suite of Sustainable Strategies
Recycled and recyclable options are also part of Hyosung’s portfolio. Whitmarsh-Knight emphasizes the company’s commitment to collaborating with customers, offering a range of products and supply chain solutions. “New sustainability regulations are coming into force, especially in Europe,” he points out. “Our customers need our help.”
Launched in 2020, regen spandex was the first of its kind to be made with 100 percent recycled pre-consumer factory waste. “Interest is really growing, and because we are so big, there is currently no issue with supply,” says Whitmarsh-Knight. Hyosung has 10 spandex manufacturing sites globally.
Denim is one of the biggest segments of Hyosung’s spandex market. CREORA 3D Max spandex brings stretch and recovery to cellulosic-based denim used at only two percent of the textile, increasing the fabric’s potential for recycling. The company also offers new USDA and SGS-certified regen Bio-Based 3D Max spandex and RCS-certified, 100 percent recycled regen 3D Max spandex made from reclaimed production waste.
Hyosung’s regen xanadu, made from recycled PET and bio-based inputs from corn, is a bi-component stretch option particularly suitable for everyday apparel and outerwear.
An Alternative Stretch Fiber Returns
XLANCE is a revival of Dow Chemical’s stretch fiber XLA, which was discontinued in 2010. Dow sold the trademarks and technology license to an Italian company, which became XLANCE S.r.l., part of the Carvico group.
The polyolefin-based, cross-linked fiber exhibits distinct advantages, promoting long-lasting stretch and performance; and its melt-spun production system, in contrast to the dry-spun method used for polyurethane-based spandex, does not involve solvent.
XLANCE is heat-settable at a significantly lower temperature than traditional spandex. “This difference is not trivial,” explains Laura Pesenti, XLANCE marketing manager. “Operating at a reduced temperature directly corresponds to less energy consumption, paving the way for notable reduction of CO2e as well as costs in the manufacturing process. This lower heat threshold provides a unique opportunity to merge XLANCE with thermosensitive fibers such as wool or polypropylene.”
XLANCE also exhibits a robust resistance to harsh chemicals and high temperatures, making the fiber ideal for swimwear, denim, and workwear. “The challenge lies in ensuring these garments can endure the rigors of industrial washing,” says Pesenti.
New Frontiers
It’s clear that consumers are not giving up on stretch garments anytime soon. While the quest for well-performing stretch fibers that veer away from fossil-based inputs is ongoing, the ability to recycle stretch garments seems to be the holy grail.
NEOLAST was recently introduced by Celanese Corporation in conjunction with athletic apparel brand Under Armour, Inc. The fibers are produced from recyclable elastoester polymers, using a proprietary solvent-free melt-extrusion process. “This new alternative could unlock the potential for end users to recycle performance stretch fabrics,” said company executives in a joint press release.
“Circularity is the ultimate solution over time, and we will get there,” advises Hyosung’s Whitmarsh-Knight.