.jpg)
What happened to Renewcell?
The recent bankruptcy of award-winning Renewcell, manufacturers of CIRCULOSE cellulose dissolving pulp made from cotton-rich textile waste, threw a bucket of cold water on the trajectory of circular textiles. The product’s beauty was its use of post-consumer and post-industrial textiles as its feedstock. Circulose was trialed by early adopters such as Swedish fashion brand Ganni; Levi-Strauss & Company and Triarchy; and retail brands H&M and Zara.
After twelve years in development, the company’s first industrial-scale plant opened in August of 2022 in a retired Swedish paper mill with an annual production capacity of 120,000 metric tons of Circulose pulp. Scaling up production required working with fiber and yarn spinners, who then sold to knitters and weavers. Each step in the supply chain increased cost, and products made with Circulose command premium pricing. H&M Group supported Renewcell over seven years with $29 million in orders; and in December agreed to acquire an additional 7,000 metric tons of Circulose in 2024 and 11,000 metric tons in 2025.
While the unexpected shortfall in long-term funding triggered Renewcell’s bankruptcy, many in the industry point fingers at mass market and fast fashion brands. “How many times a year do we see someone launch a new brand that is entirely dependent on fossil fuel-based fibers? It’s clearly a lack of education that allows people to keep making mistakes like this. Hopefully we see a shift in time to facilitate the growth in these (circular) technologies instead of letting them go bankrupt in favor of celebrity and fast fashion brands,” remarks Adam Taubenfligel, CEO of high-end responsible denim brand Triarchy.
As Renewcell’s operations are currently under the control of the bankruptcy administrator, “viscose made with Circulose is available for sale in the market and additional tons of Circulose pulp have been produced,” says Shannon Welch, Renewcell global brand director. “There is a supply that will satisfy the projected needs of brands and suppliers for the next 18 -24 months.”
Welch suggests that the industry is experiencing the “trough of disillusionment,” which is a natural phase of the Gartner Hype Cycle as it relates to technology innovation. “However, with disillusionment, innovations continue, and early-stage companies can iterate their products and processes to better serve the market.”
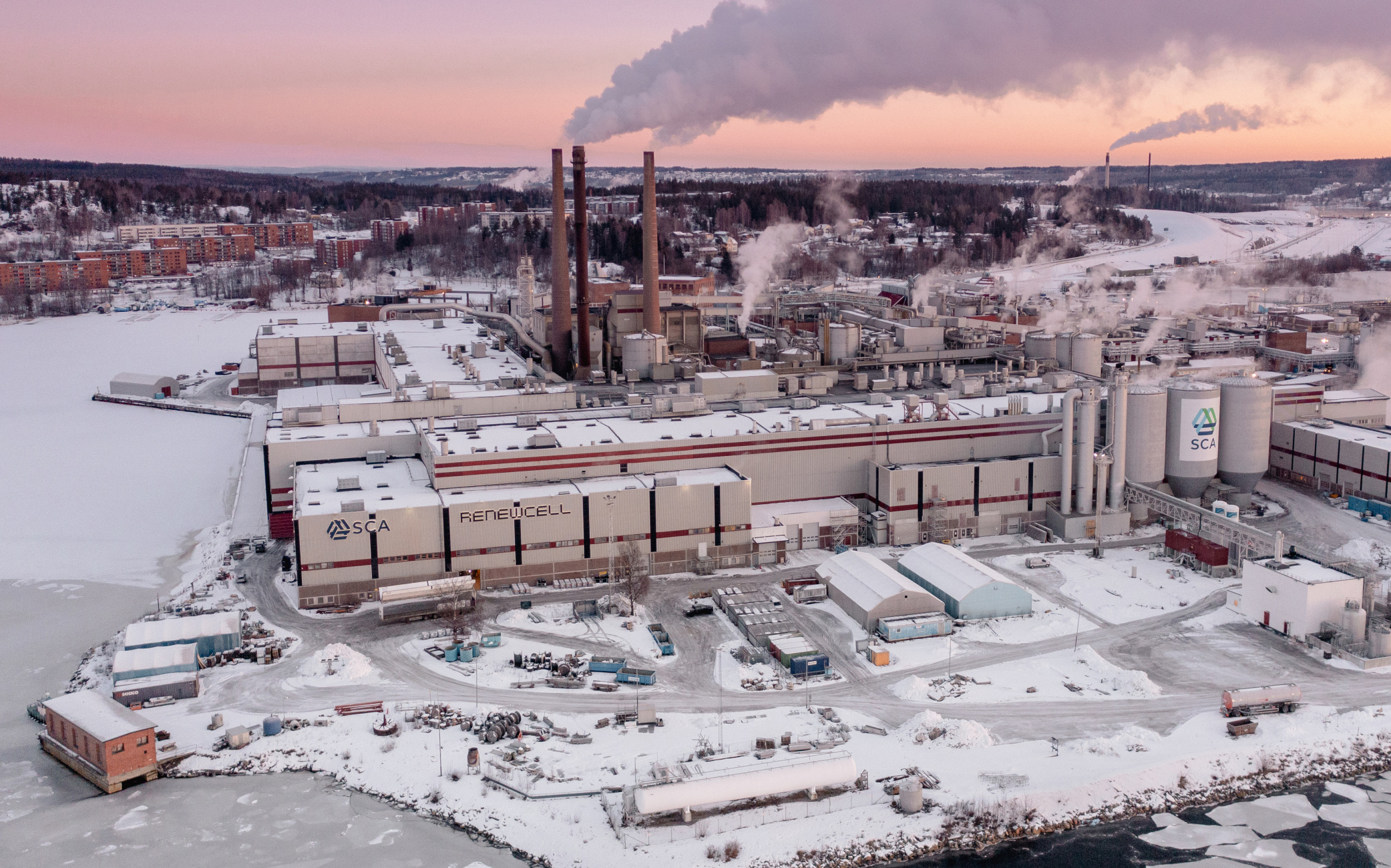
Strengthening Supply Chains
The EU’s Waste Framework Directive specifies implementation of separate textile waste collection by January 1, 2025. How the member countries will deal with this is anyone’s guess; but the potential is there to provide feedstock for textile-to-textile recycling. Proposed regulation on waste shipments will ensure that textile waste is only exported when there are guarantees that the waste is managed in an environmentally sound manner.
However, Techstyler Founder Brooke Roberts-Islam asks why Renewcell and other circular textile technologies are manufactured and marketed in Europe and the U.S., while most apparel manufacturing is in Asia and the global South. She points out in a Forbes article that circular technologies need to be integrated into those textile supply chains.
Syre, billed as a “new impact venture,” aims to counter this issue by establishing multiple production plants producing circular polyester (cPET) at “hyperscale” across the globe. “Polyester is by far the biggest and fastest growing fiber, meaning the market is substantial. We have secured a seven-year off-take agreement with H&M Group worth a total of $600 million, covering more than half of H&M Group’s long-term need for recycled polyester,” explains Dennis Nobelius, CEO of Syre. H&M Group is a founder of Syre.
The input will be textile waste from textile producers as well as post-consumer waste. “We are establishing a feedstock system with access from all industries that produce and consume polyester. We have a strong regional focus, aiming to source as close to the recycling plants and downstream demand as possible to minimize transport emissions and cost,” he continues.
Nobelius points out that “the textile industry is now at a tipping point as the European Union and other actors are introducing legislation that will regulate waste and accelerate demand for circular materials.” H&M and many other brands currently rely on rPET sourced from bottles, which is not circular.
Syre’s first plant is being built in North Carolina, where it will provide textile-to-textile cPET at a level of quality and performance on par with virgin polyester. The plant is expected to be online in 2024, with the manufacturing process scaling up for global expansion into Asia and Europe. Importantly, the platform is said to have potential to expand into other fibers and technologies in the future.
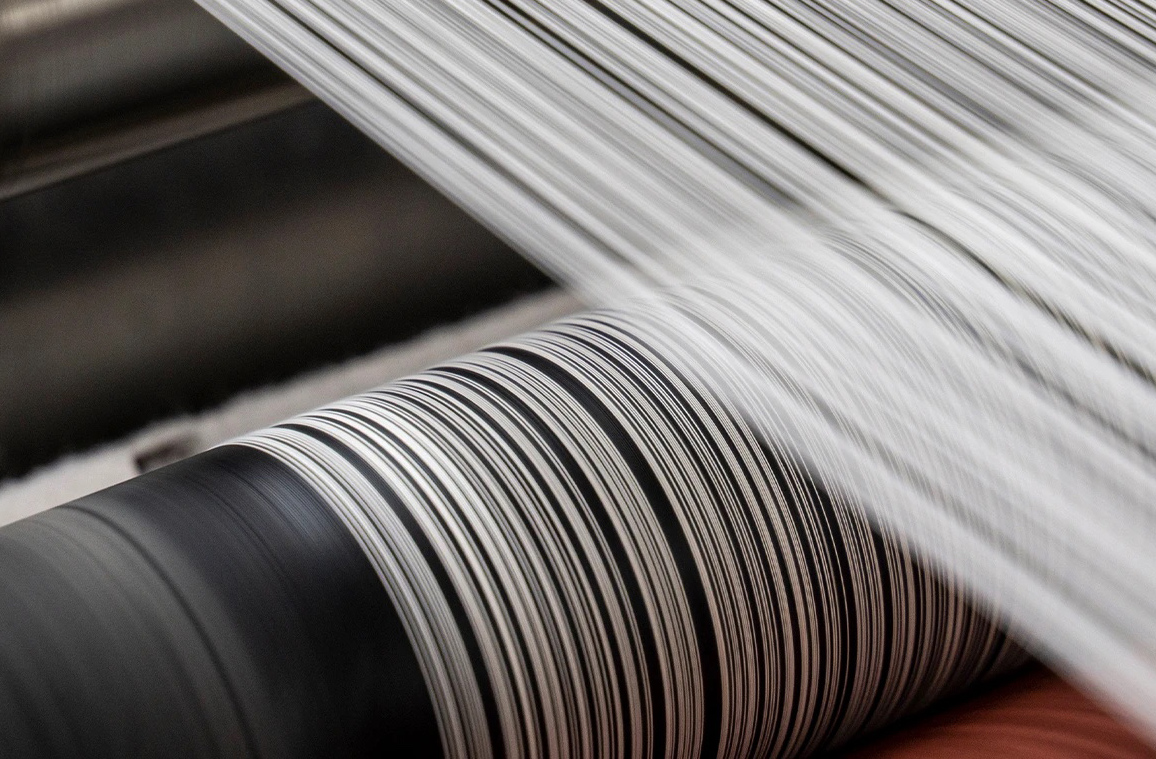
Overcoming feedstock limitations
Using molecular technology to break down mixed textile waste is another way to simplify the textile-to-textile process. BASF, with production sites in Europe, Asia, and North and South America, has developed loopamid, a recycled nylon 6 (PA6) polymer for textiles and apparel components that can be recycled multiple times. Zara has created a jacket “designed for recycling,” with fabrics, buttons, filling, hook and loop and zipper all made from loopamid.
“The technology behind loopamid enables textile-to-textile recycling of polyamide 6 (PA6) into new, virgin-quality synthetic fibers,” explains Dag Wiebelhaus, head of global product innovation, monomers division, BASF. “Our mission is to enable true circularity for the textile industry by overcoming limitations of the current recycling processes – specifically for nylon garments. We are recycling textile waste at a molecular level ready to be transformed into brand new, premium fabrics.”
Wiebelhaus points out that textile blends of various materials complicate the recycling process. “Separating the polyamide from other materials in these blends can be technically challenging. For loopamid, BASF has developed a process to regain PA6 in a robust process with high yields of pure polyamides. Only what is PA6 in the feed can be recycled back to PA6, i.e., loopamid.”
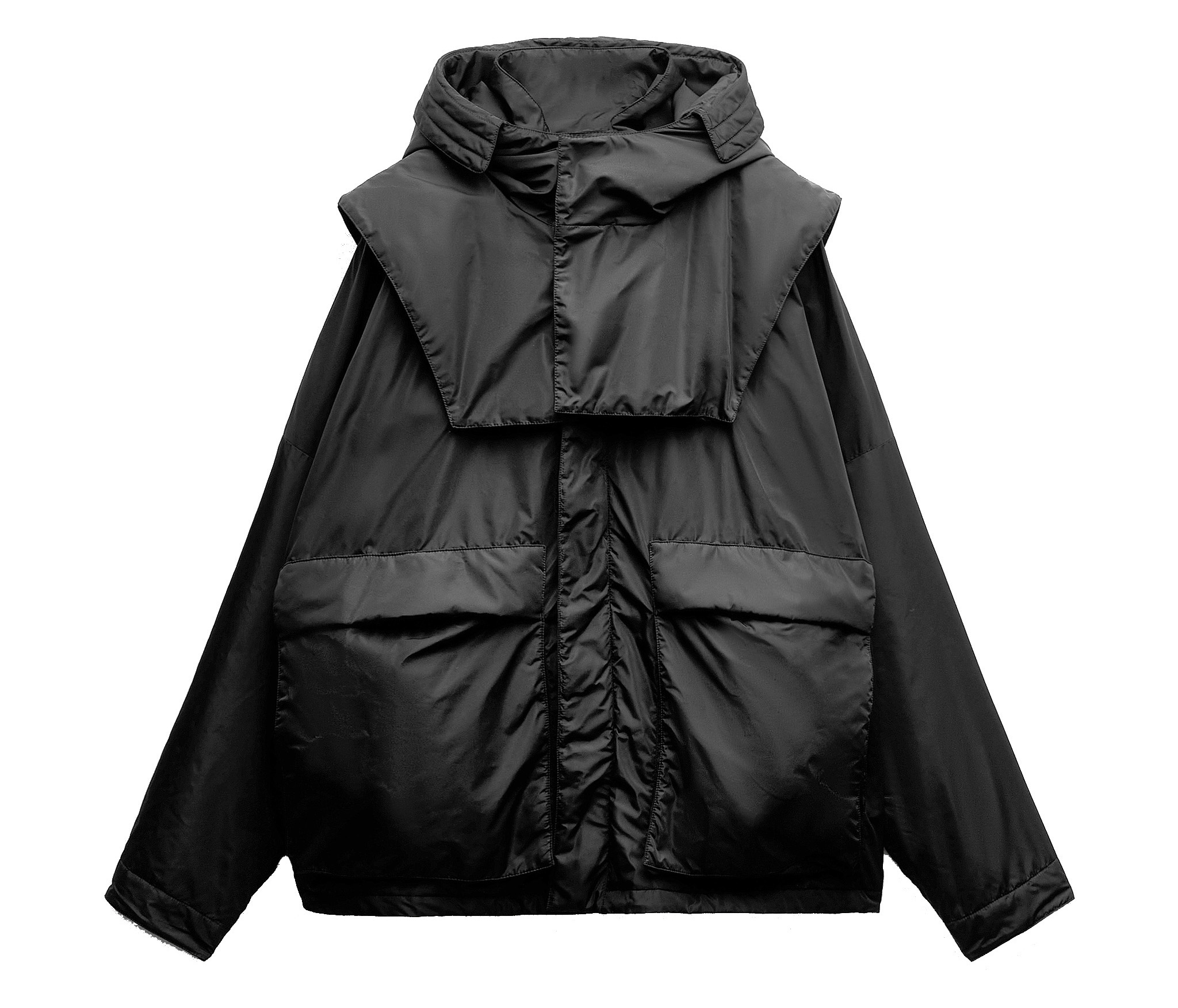
How to create a circular future
Published in January 2024, an analysis of the global circular fashion market size by Coherent Market Insights values it at $6.09 billion in 2023. The global circular fashion market is expected to reach $11 billion by 2030.
Renewcell’s Welch concludes, “One of the main learnings we’ve gained from this experience is that business cannot change an industry alone. For systemic change to happen you need the buy-in of business/brands, legislation with teeth that either comes with tax incentives or subsidies, or there must be transition funds to help off-set the higher costs of new innovations.”
