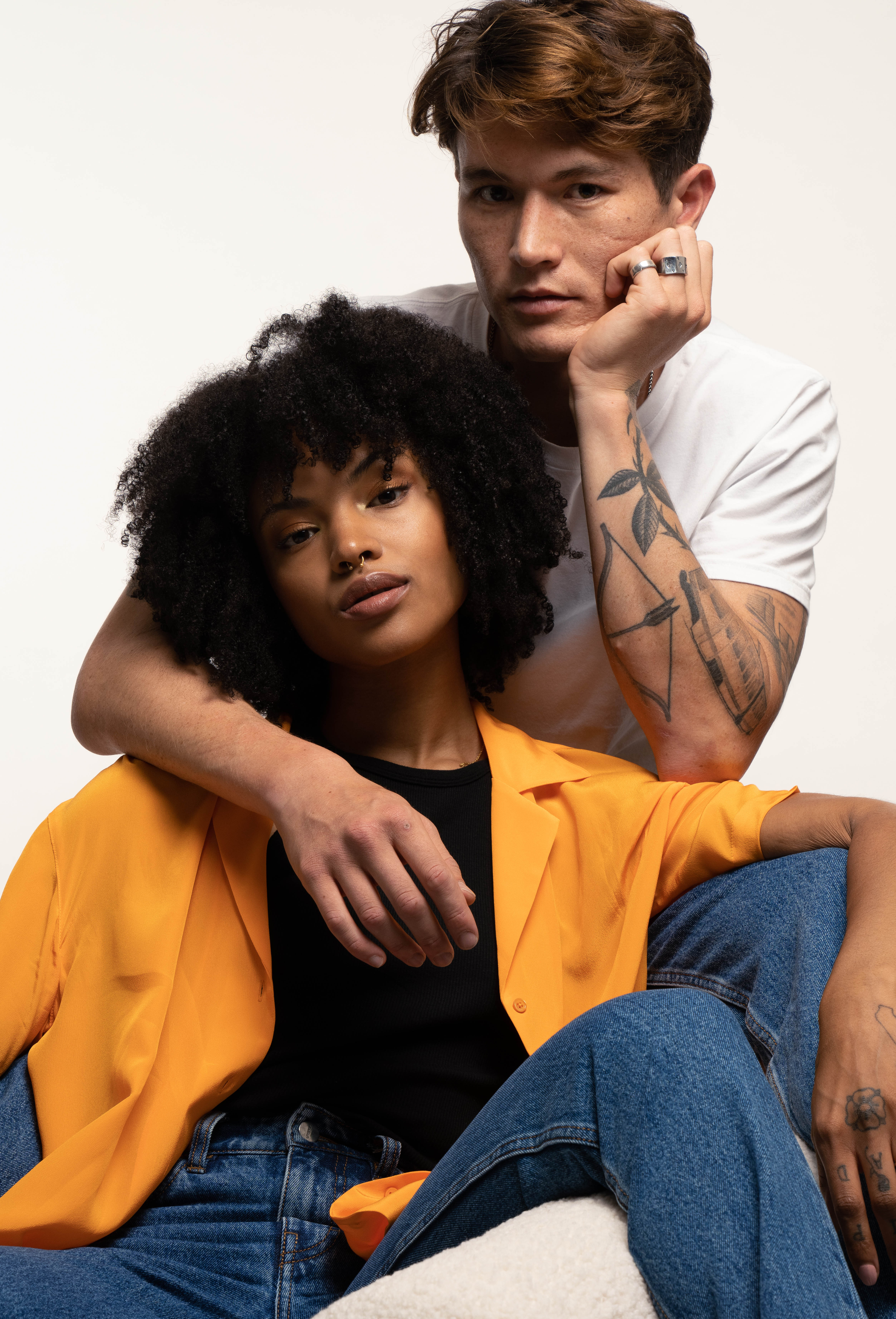
Execs have told us that their companies are committed to efficient manufacturing practices that minimize material and energy waste; reducing the textile industry’s reliance on virgin materials; building infrastructure for textile recycling; making efficient decisions on business travel and the shipment of goods; exploring regenerative agriculture and producing long-lasting, durable products. This all sounds great, but is it enough to move the needle forward? We’ve asked firms to let us in on what is working right now, what goals are for the future and where we need to go as an industry to move toward a more vibrant shade of green.
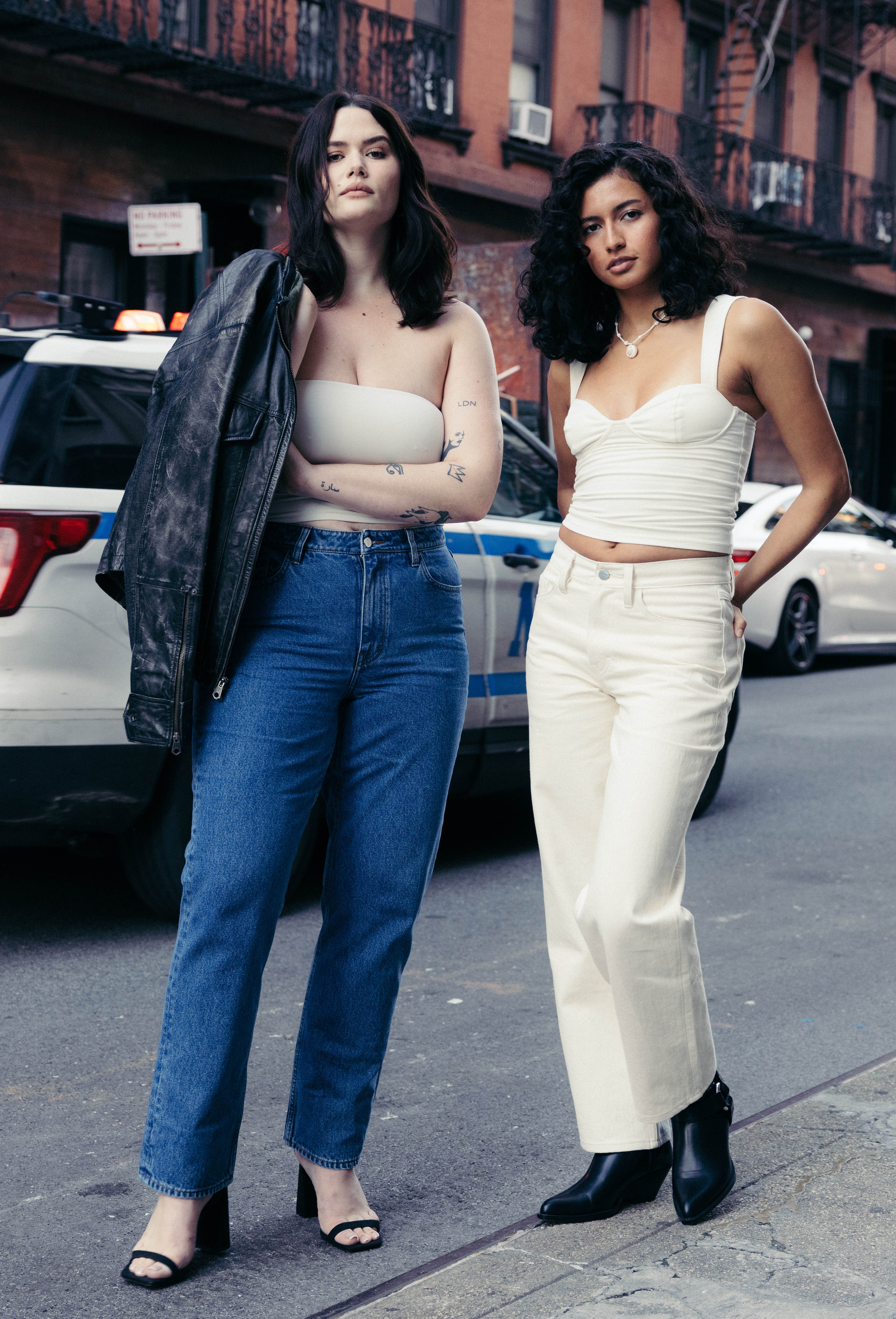
RIGHT NOW
“Our main priority is to build a global infrastructure of certified fiber manufacturers offering polyester and nylon made with CiCLO at an affordable cost so that it can be adopted as a platform solution across all products that require synthetics. We started CiCLO to create a better polyester; one that remains durable and high performance during its useful life, can be recycled and can also biodegrade.”
- Andrea Ferris, co-founder, CiCLO technology
“Our focus is on using NetPlus (Bureo’s 100% post-consumer recycled nylon from fishing nets) to displace virgin nylon materials. We’re now expanding our offering of fabrics made from NetPlus across Pertex Shield & Pertex Equilibrium categories. In terms of polyester, we’re working with Ambercycle to incorporate their cycora material into Pertex fabrics.”
- Andy Laycock, brand director, Pertex
“At Polygiene, we’ve recently embarked on our CSRD (Corporate Sustainability Reporting Directive) journey to create a comprehensive sustainability strategy. For consumers, our goal is to educate them on the importance of responsible textile care. Our initiative ‘Wear More, Wash Less’ encourages consumers to wash garments less frequently to extend the life of their clothing, so we can significantly reduce water, energy and detergent consumption, as well as minimize microplastic pollution.”
- Ulrika Björk, CEO, Polygiene
“It’s a clear focus for Hyosung – move to renewable raw materials where possible and support the industry’s goal of circular business models via textile-to-textile recycling. In line with our corporate goal of achieving net zero by 2050, we recently announced a $1 billion investment in our Vietnam plant to create the world’s first integrated production facility for bio-based spandex from raw material to fiber. In addition, we are collaborating with Ambercycle to bring post-consumer regenerated polyester fiber to the market at scale.”
- Simon Whitmarsh-Knight, global sustainability, Hyosung
“Vega 3D weaving technology weaves clothes from yarn within minutes, simplifying fashion supply chains into a vertical operation, regardless of location. It allows companies to produce faster (automated), closer to home (local), and in accordance with demand (via our on-demand production model). Our machines are also more energy-efficient than traditional air-jet weaving counterparts, cutting carbon emissions by 24% during the weaving process alone.”
- Annika Visser, brand lead, unspun
“PrimaLoft P.U.R.E. is a manufacturing method that drastically reduce emissions during the production of synthetic insulation. We’ve worked extensively with our factory partners to utilize renewable energy, like solar and more efficient, electric-powered equipment, removing the need for fossil fuels. This results in emission reduction of 50% or more. PrimaLoft P.U.R.E. is currently used to produce more than a half dozen PrimaLoft products and we’re working to expand further through our product portfolio.”
- Anne Cavassa, CEO, PrimaLoft
“In 2023, we were the first to deliver a durable EPA registered citric-based formula as an antimicrobial technology to global markets. We are showcasing our latest technology with Ionic+ Pro and PRISM – our fabric partnership with e.dye. There is a swell of misleading conversations about proven, safe, effective, technology as it relates to silver actives. We have invested heavily... to make sure we’re tracking any shift in certification and compliance globally.”
- Allon Cohne, CMO, Noble Biomaterials
“While we pioneer many new sustainability innovations, we are also thoughtful around the dynamic of developing a completely new product versus enhancing an existing product. Also, we are seeing an increase in companies/brand partners that are utilizing and highlighting a list of preferred materials with their partners. This is a great initiative and one that will continue to increase in use.”
- Stephen Kerns, president, Schoeller USA
“Our focus is on textile-to-textile regeneration and establishing a circular ecosystem. We’re doing it at a greater efficiency and scale than ever before. The end product – Reju Polyester – will have less than 50% lower carbon footprint than virgin polyester. We are committed to bringing a product to market that is demonstrably cleaner, will function and feel better than new and can be regenerated infinitely.”
- Patrik Frisk, CEO, Reju

FUTURE FOCUS
“Our ambition is to accelerate the transition to a circular polyester system. We’re focused on scale. Our first facility, Regeneration Hub Zero, is open in Frankfurt, Germany. The Hub was built in record time and is expected to begin deliveries in 2025.”
- Patrik Frisk, CEO, Reju
“Our goal is clear – move to renewable raw materials and ultimately full circularity via textile-to-textile recycling.”
- Simon Whitmarsh-Knight, global sustainability, Hyosung
“Our goal is to stop using the term ‘sustainability.’ It’s a term of ubiquity and it’s been misrepresented and misused to sell more products. Our goal is to develop product with emotional durability so that purchasing a product means you enjoy it more because you use less resources to care for it, (water/energy/detergents), the color fades less, the fabric integrity lasts longer so it doesn’t need to be replaced as quickly.”
- Allon Cohne, CMO, Noble Biomaterials
“Increased supply chain knowledge is critical in pushing sustainability forward. A McKinsey report called out that 90% of companies’ impact on the environment comes from supply chains. We have met with hundreds of companies, and I see firsthand that brands want to make more informed choices that are better for the environment, but to do so, they need to fully understand all stages of the supply chain.”
- Andrea Ferris, co-founder, CiCLO technology
“By developing innovative, effective technologies that help garments stay fresh for longer, we are enabling a future where fewer resources are used in manufacturing and fewer products end up in landfills. Also, by building increasingly stronger collaborations with our partners to help them better communicate the sustainability benefits of Polygiene treatments to customers, we can reduce environmental impact collectively.”
- Ulrika Björk, CEO, Polygiene
“We’ve been able to re-engineer our entire waterproof breathable fabric offering to be free of PFAS - both in the membranes and DWR finishes. This has been a challenge with our high-performance microporous (Pertex Shield Pro) and nanofiber (Pertex Shield Air) membrane technologies. Doing so without compromising performance and durability is key to reducing the overall impact of a fabric or garment across its lifetime.”
- Andy Laycock, brand director, Pertex
“PrimaLoft has a track record of firsts and early adoptions of sustainable technology, from the use of recycled material dating back to the ‘90s, to introducing the first biodegradable synthetic insulation for apparel. We’re currently working to establish baselines and set goals that will reduce our overall footprint, throughout the supply chain.”
- Anne Cavassa, CEO, PrimaLoft
“Our goal is to reimagine and disrupt traditional supply chains and order volumes, decrease transportation and lead times, and bring clothing brands—and their customers—closer to the source and production of goods. This year, we announced a partnership with Walmart to scale Vega 3D weaving technology, which aimed to localize parts of Walmart’s manufacturing and promote increased supply chain traceability in North America, while decreasing emissions and waste.”
- Annika Visser, brand lead, unspun
“I am probably most excited about a relatively new upcycled polyamide yarn we are working on. We are also always looking at more mono material potentials. In 2024, we started to incorporate an even greater digitization strategy in manufacturing. Overall, we remain focused reducing our Greenhouse Gas Emissions with next milestone of 46% less by 2030 and zero by 2050.”
- Stephen Kerns, president, Schoeller USA
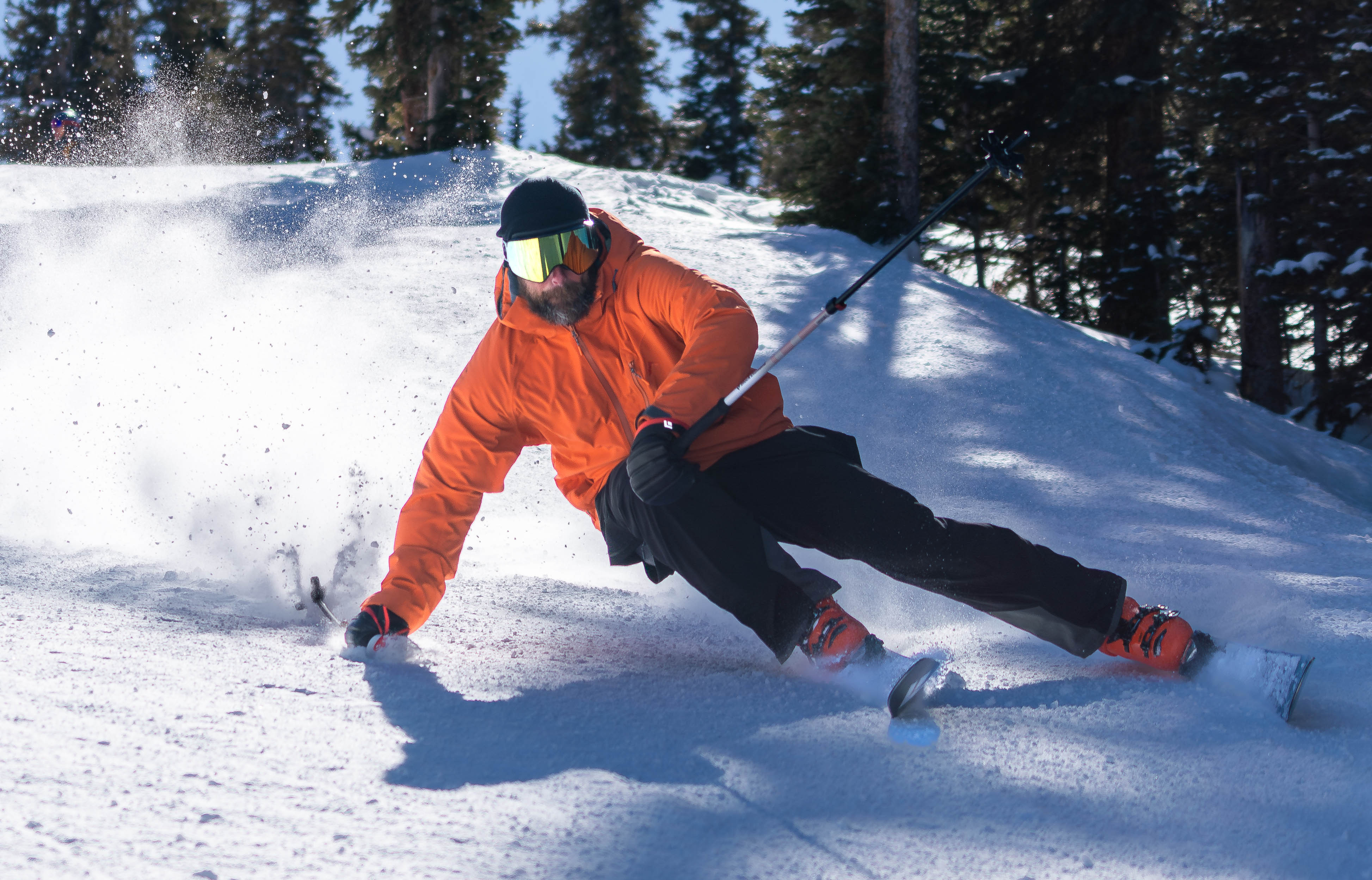
INDUSTRY ENDEAVORS
“Choosing better raw materials, more sustainable chemistries, recycling, moving to renewable energy and many more. I believe the most beneficial thing we can do is to simply make the most durable products and produce less of them.”
- Andrea Ferris, co-founder, CiCLO technology
“Educating consumers and inspiring them to adopt more mindful lifestyles, which is at the core of our “Mindful Living” philosophy. Educating people on frequent washing, overconsumption, and poor garment care can empower them to make more sustainable choices.”
- Ulrika Björk, CEO, Polygiene
“Reducing emissions through the use of renewable energy and cleaner manufacturing practices is essential. Combatting microplastic pollution by exploring biodegradable and natural material solutions is also key.” - Anne Cavassa, CEO, PrimaLoft
“Industry-wide collaboration is an important tool to start to work towards for more long-term goals of responsibility and circularity. Incoming regulations mean that supply chain transparency and co-operation is becoming crucial.”
- Andy Laycock, brand director, Pertex
“Full circularity cannot be achieved by any of us acting alone – all elements of the value chain need to work together to test new technologies, agree on focused infrastructure investment and accelerate adoptions at scale. We all need to speed up!”
- Simon Whitmarsh-Knight, global sustainability, Hyosung
“A step industry can take to lessen its impact is accepting and implementing new ways of doing things, even those that require large changes. The reluctance to do so, may be why clothing production hasn’t really changed much since the invention of the sewing machine.”
- Annika Visser, brand lead, unspun
“We should continue to work as community supporting overall knowledge building and recognize all brands’ and companies’ advancements as good overall, versus being competitive in nature.”
- Stephen Kerns, president, Schoeller USA
“By joining with upstream partners around the world to recover, collect and sort waste textiles, we’re creating a circular textile system that does not yet exist. The world produces 92 million tons of textile waste each year, yet less than 1% is recycled. The system extracts finite resources and creates textile waste with no responsibility for end-of-life.”
- Patrik Frisk, CEO, Reju
“Dig deeper. We’ve talked recently about market concerns globally as it pertains to incumbent technologies. We are now helping product, sourcing and materials teams understand what all the regulations, certifications and testing standards mean. We are engaging customers to communicate with their legal, finance and compliance teams.”
- Allon Cohne, CMO, Noble Biomaterials
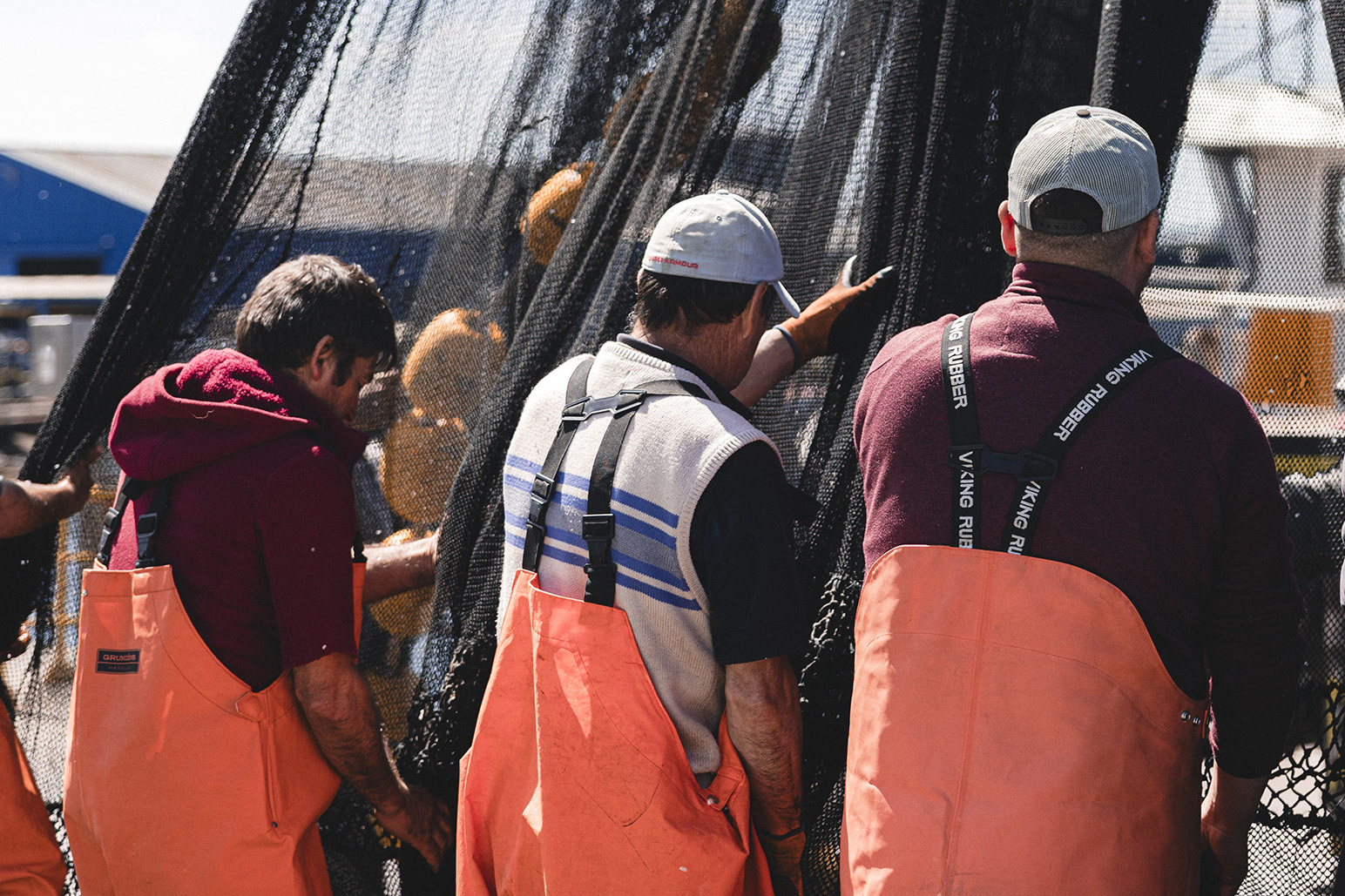