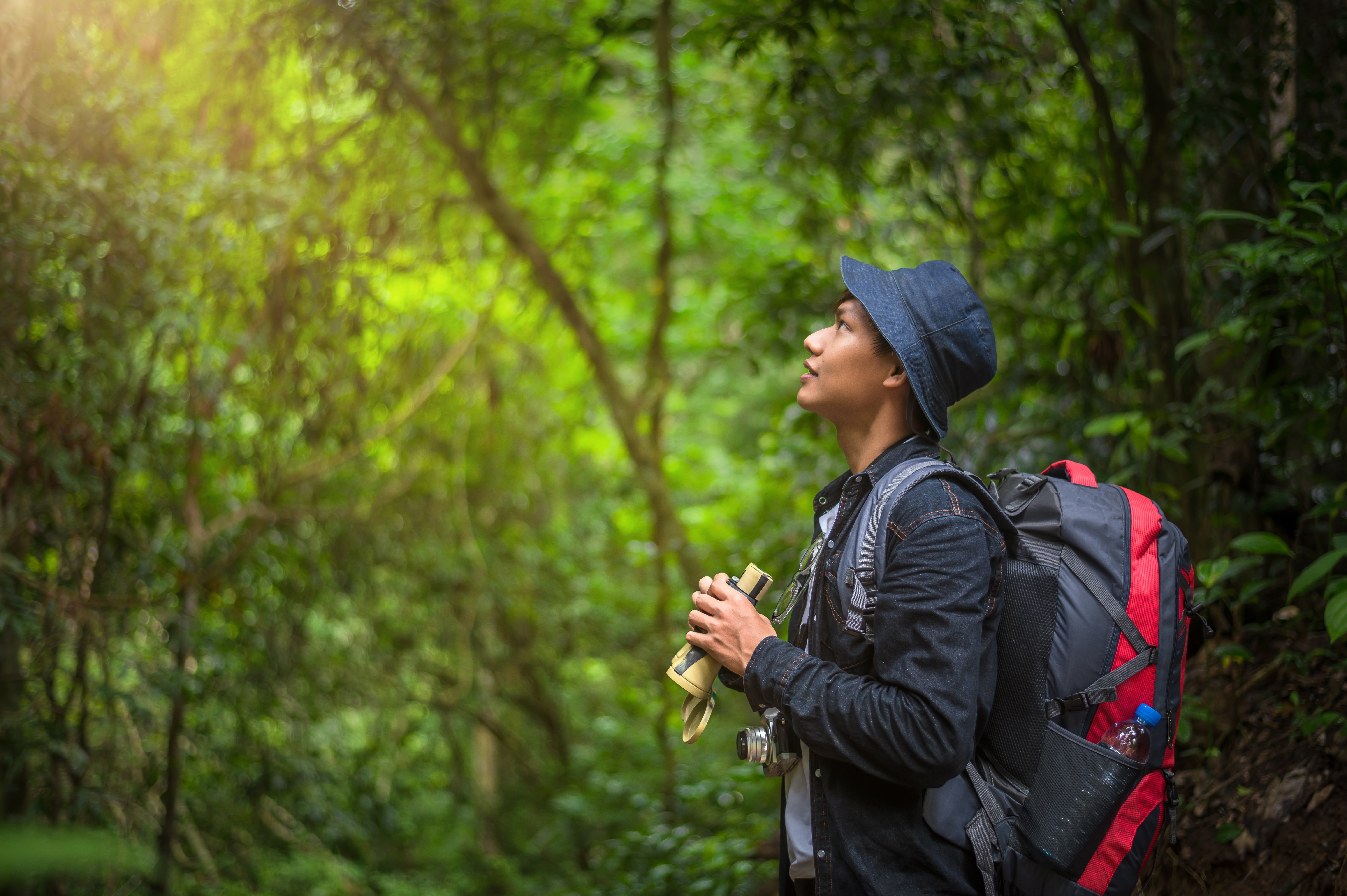
Here are a handful of factors key to determining future developments.
The Future of Fibers is Natural
As companies dig deeper into the world of natural fibers, two areas are worth watching. On land, keep an eye on advancements in hemp, while oceans are seen as the new farmland for finding opportunities using marine-derived textiles.
According to the recently released National Hemp Report, 2023 production of hemp grown in the open for fiber was estimated at 49.1M pounds, up 133 percent from 2022. Area harvested for hemp grown in the open for fiber in the U.S. was estimated at 12,106 acres, up 77 percent from last season. Textile Exchange reports the industrial hemp market size is expected to grow rapidly in the next few years, rising from $6.8 billion in 2022 to $18.1 billion in 2027, at a CAGR of 21.6 percent from 2022 to 2027.
Patagonia hemp clothing already totals 74 items, with more on the docket. The company’s Spring ‘25 Work Denim collection uses hemp grown in Alabama and Tennessee, processed in the U.S. through Bastcore, an Alabama-based company pioneering hemp textile production.
The 2024 Special Report: Marine Derived Textiles, published by World Textile Information Network (WTiN) recaps a recent event that drew a crowd focused on algal fiber innovations and ocean-harvested materials. Brands participating included: Algaeing, Keel Labs, Sway, Squitex, Phycolabs, Seaqual, Living Ink, Pneuma and Algix among many others. “It is still an emerging science and little commercially ready, yet the feeling is that there is an appetite for alternatives that marine derived can satiate,” said Fuzhong Zhang, a professor at Washington University in St. Louis, MO in a round-up of speaker comments. Adding to Zhang’s statement, Uyen Tran, founder of material science company TomTex, observed, “the sea is a great resource of materials that are high-value, high-performing and have innate functional properties.”
Attendees cited scalability, cost competitiveness and seamless integration into established facilities as big challenges. However, bright spots exist, particularly in the advancement of inks, dyes and packaging. California company Sway released a scalable seaweed-based plastic packaging alternative, following a recent close of $5M seed round. Its TPSEA (thermoplastic seaweed resin) is a 100 percent bio-based, home composable, microplastic-free ingredient that is scalable and compatible with existing infrastructure.
The Future of Clothing Is Climate-Conscious
As the planet continues to warm – 2023 was the hottest year on record, according to the website Climate.gov – fabrics that keep wearers cool is top of mind as demand for cooling technologies is likely to grow. According to Bloomberg, companies see opportunity in apparel designed to beat the heat; Market forecasts expect sales growth annually of around eight percent by 2032.
Cooling via micro-minerals permanently integrated into fabric is used by brrr to create the brand’s “triple chill effect.” The company continues to upgrade and intensify cooling action with a new biodegradable yarn made in partnership with CiCLO, creator of a technology that speeds biodegradation in landfill conditions; brrr polyester CiCLO fabrics biodegrade 3.5 times faster than a control fabric, according to the suppliers. Another sustainable option brrr has under development is a mechanical stretch fabric, made without spandex or elastane for better reuse potential and circular design.
An ISPO textile report recently highlighted the importance of cooling techniques in an age of rising temperatures. E.COOLINE takes a novel approach by cooling through trapped moisture, enabling cooling evaporation without the textile having to feel wet. It relies on a special 3D structure that binds and stores moisture directly in the 3D fibers.
The Future of Fabric Is PFAS-Free
Despite good progress bringing water repellent fabrics free of harmful chemicals to market, negating the need for PFAS in performance garments will remain a primary focus of textile suppliers and brands for years to come.
Nikwax has unveiled a new factory applied Direct.Dry DWR, that is a high performance, highly-durable, PFAS-free DWR, available this Fall via exclusive launch partner Outdoor Research. “As the PFAS-free timelines started to accelerate with regulations in California and other areas, we wanted to find a way to better support brands and retailers through the transition with a PFAS- free DWR for fabric,” explained Brian Davidson, CEO, Nikwax global / president, Nikwax NA, who added, “Our formula fits seamlessly into existing application methods, and we look forward to working with new factories and brands going forward.” Direct.Dry is currently available for all brands.
Silicone has entered the field of budding PFAS-free alternatives, but the jury is still out on permeability and durability. Alden Wicker, an authority on textile chemicals, wrote in her EcoCult newsletter, “I’ve been hearing some concerns about silicone. After all, it looks and feels and acts similar to plastic. And it’s being proposed as a safe replacement for toxic, PFAS-based, stain-resistant textile coatings. With plastic’s many hazardous properties being increasingly documented, it’s fair to question whether this synthetic material gets a special pass to be on your body and touching your food.”
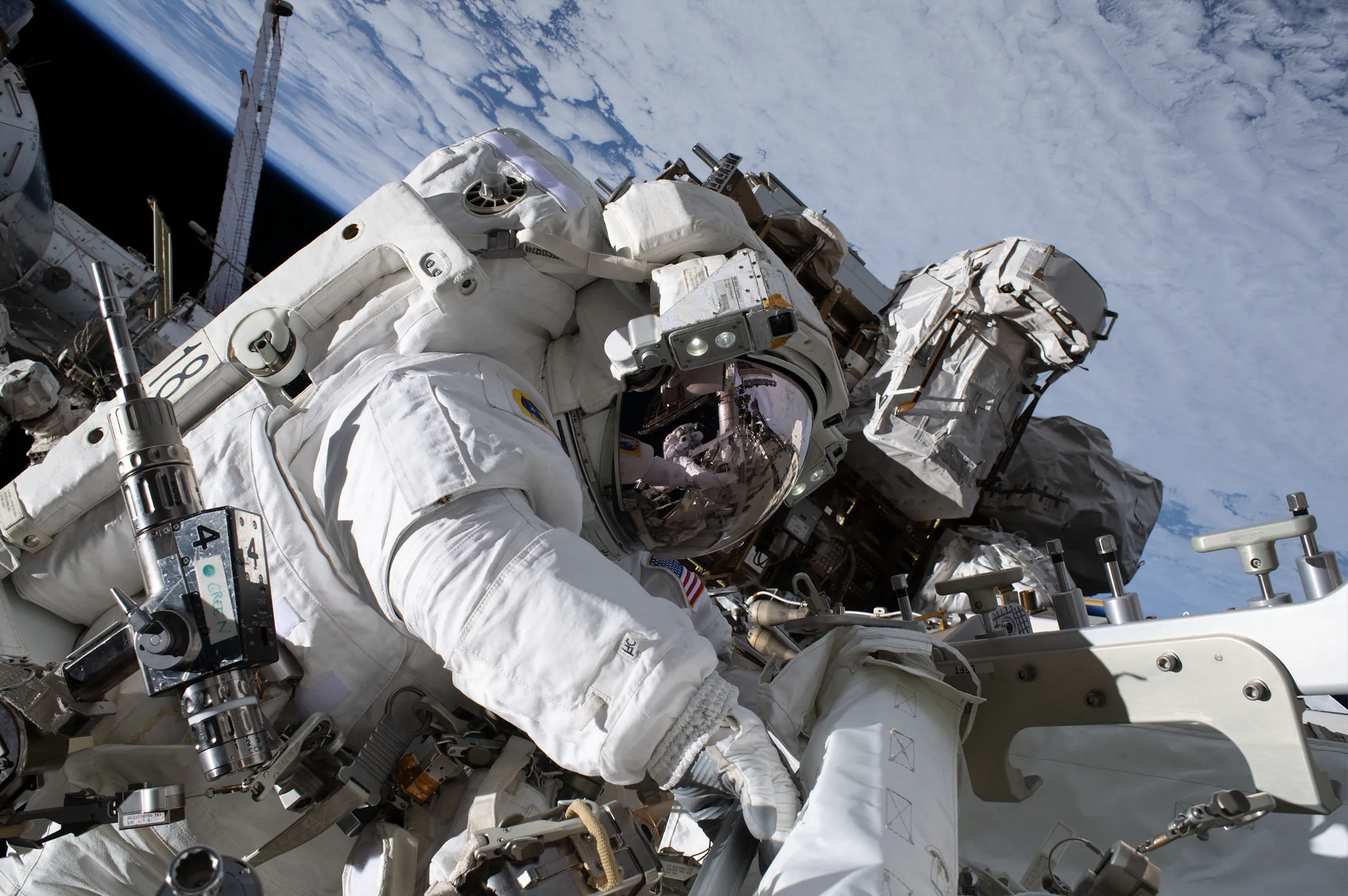
The Future of Textiles Is Net Zero
Commitment to sustainability goals is a springboard for ongoing investment in “net zero” initiatives. For example, Hyosung is investing $1B in creating the world’s first integrated production of bio spandex from raw material to fiber. Hyosung has partnered with Geno, a San Diego, CA-based biotech firm, to start construction at its plant in Vietnam of facilities to produce Bio BDO derived from sugarcane, commencing Q2 2026.
According to a company statement, the project will fast track the production of Bio BDO with an annual capacity of 50,000 tons in the second half of 2026 – with the aim of expanding capacity up to a total of 200,000 tons/year to meet expected industry demands of bio-based spandex. (BDO is the technical name for butanediol, a chemical traditionally made from fossil fuels and a major ingredient in the manufacture of spandex.)
“Through this vertical integration from raw material to yarn for regen bio spandex, our goal is to increase production efficiency, provide faster response to our customer needs and integrate value chains to help minimize carbon footprint,” said Sora Yoo, CMA, Hyosung Textiles.
Strides in net zero solutions are being made in footwear. OrthoLite subsidiary Cirql has introduced a new midsole foam called Cirql rTPU30 made with 30-percent post-consumer recycled TPU material and manufactured through a chemical-free, supercritical foaming process.
Footwear developer Marc Scepi, VP design at GREATS, states, “Cirql’s rTPU30 ushers in a pivotal shift in sneaker sustainability, marrying environmental responsibility with industry demands. This midsole, a fusion of 70 percent virgin and 30 percent post-consumer TPU, sets a new standard by reducing reliance on new materials and ensuring full recyclability. Its integration of GRS-certified recycled content like clear cell phone cases disrupts traditional production cycles, paving the way for cleaner, greener manufacturing.”
Scepi added, “With its dual applicability as a midsole and co-molded outsole, rTPU30 offers a complete recyclable unit, demonstrating that high-end sustainability is now within reach for everyday footwear.”
The Future Is Innovation
Advancing wellness benefits for lifestyle product and pushing the limits of safety for new domains reflects how the industry is always looking beyond the here and now to what’s next, whether that’s “healthy” hosiery yarns or flame-resistant clothing for astronauts operating space vehicles during a lunar landing mission.
Milliken & Company is working to design and manufacture flame-resistant (FR) baselayer fabric for NASA’s upcoming Artemis missions. Due to elevated oxygen levels that increase the risk of fire in space, Milliken, in collaboration with global professional services firm Jacobs Technology through the JSC Engineering, Technology & Science (JETS) II contract with NASA, is developing a next-to-skin textile for clothing worn by astronauts while operating space vehicles during the lunar landing mission.
Milliken and Jacobs are finalizing prototypes and manufacturing the new textile for final delivery to NASA. This phase is expected to be complete by Fall 2024. The launch date for Artemis III is slated no earlier than 2026. Ramesh Kesh, SVP, Milliken’s Textile Business, stated, “It’s the perfect marriage of the FR capabilities of our Westex brand and the knit fabrics expertise from our Polartec brand.”
Making wellness as easily attainable as putting on a pair of socks is an early-stage concept being explored at hosiery brand Vim & Vigr. “People don’t get up and move around as much working from home, especially if they live in a 600-square foot apartment! More sitting means less movement which results in tired achy legs,” explained Michelle Huie, company founder, with a background in healthcare. Infusing healthy benefits into yarns used in Vim & Vigr’s stylish compression socks, can help customers live everyday wellness, according to Huie, who continues to seek ways to evolve and elevate the therapeutic performance of graduated compression hosiery. “People are more aware, and savvy about health in general, and particularly products that offer wellness features and self-care,” said Huie. However, creating a delivery system in legwear is daunting. “Natural fibers are not consistent in density and you need consistency with delivery.” But, Huie added, “constraints spark creativity.”